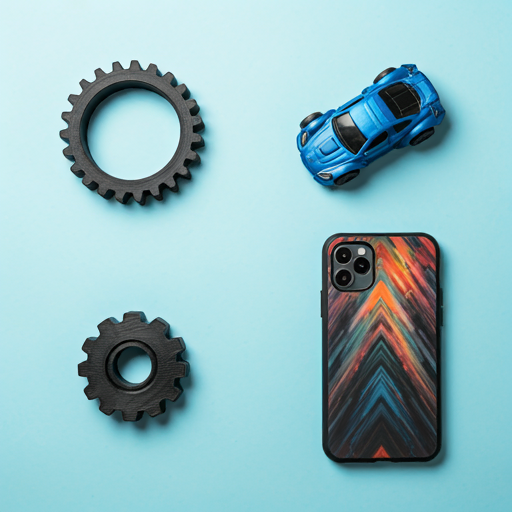
Our capabilities
Our Aerospace 3D Printing Services
Our cutting-edge 3D printing solutions revolutionize the aerospace industry by producing lightweight, complex components that meet rigorous safety and performance standards. From satellites to aircraft parts, we enable innovation in aerospace design and manufacturing.
Fuel Nozzles
Produce fuel nozzles with complex internal channels that improve fuel efficiency and reduce emissions. Our 3D printed nozzles offer enhanced performance over traditionally manufactured counterparts.
-
Optimized Fuel Flow
-
Reduced Emissions
-
Longer Component Lifespan
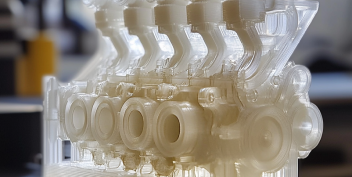
Satellite Components
Manufacture lightweight structures and brackets for satellites, maximizing payload capacity and reducing launch costs. Our materials meet the strict requirements for space applications.
-
Weight Reduction
-
High-Strength Materials
-
Customized for Mission Needs
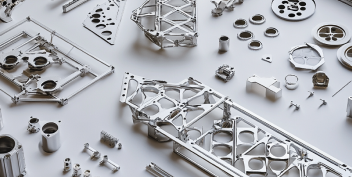
Turbine Blades
Create turbine blades with precise geometries for jet engines, improving efficiency and reliability. 3D printing allows for internal cooling channels not possible with traditional methods.
-
Enhanced Engine Efficiency
-
Complex Cooling Systems
-
Increased Durability
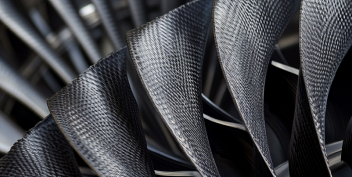
Drone Components
Design and produce parts for unmanned aerial vehicles (UAVs), including airframes and propellers, enabling rapid development and deployment of drones for various applications.
-
Lightweight Structures
-
Customized Designs
-
Quick Prototyping
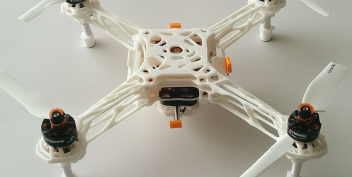
Aircraft Control System
Manufacture complex components for aircraft environmental control systems, such as air ducts and heat exchangers, improving passenger comfort and system efficiency.
-
Optimized Airflow
-
Reduced System Weight
-
Improved Thermal Management
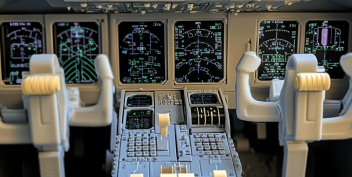
Testing Models
Produce scale models of aircraft structures for wind tunnel testing and simulation, allowing engineers to refine designs for aerodynamic performance.
-
Accurate Scale Replicas
-
Enhanced Design Validation
-
Accelerated Development Cycles
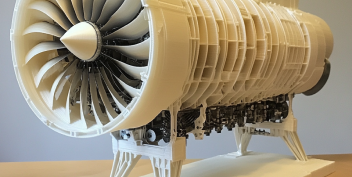
Find your queries
Frequently Asked Question(FAQ)
- General
- Materials and Technologies
- Design and Innovation
- Implementation and Integration
- Quality and Certification
-
What are the advantages of using 3D printing in the
aerospace industry?
- 3D printing offers significant advantages in the aerospace industry, including weight reduction, cost savings, and enhanced design flexibility. By enabling the production of complex geometries and lightweight structures, additive manufacturing improves fuel efficiency and performance. It also accelerates prototyping and reduces material waste, leading to faster development cycles and more innovative aerospace components.
-
How does 3D printing contribute to lightweight aerospace
components?
- Additive manufacturing allows for the creation of intricate lattice structures and optimized designs that minimize weight without sacrificing strength. By precisely controlling material placement, 3D printing reduces unnecessary mass, resulting in lighter components that enhance fuel efficiency and payload capacity in aircraft and spacecraft.
-
Can 3D printed parts meet aerospace quality
standards?
- Yes, with proper material selection, process control, and rigorous testing, 3D printed parts can meet the stringent quality and performance standards required in the aerospace industry. Certification and validation processes ensure that components comply with industry regulations and are safe for use in critical aerospace applications.
-
What aerospace components are commonly produced using 3D
printing?
- Commonly 3D printed aerospace components include engine parts, fuel nozzles, brackets, ducts, heat exchangers, and structural components. 3D printing is also used for tooling, fixtures, and prototypes, as well as for creating parts for satellites, drones, and spacecraft.
-
Is 3D printing cost-effective for aerospace
manufacturing?
- While the initial investment in 3D printing technology can be significant, the long-term benefits often outweigh the costs. Additive manufacturing reduces material waste, lowers tooling expenses, and shortens production times, leading to overall cost savings. For low-volume, complex, or custom parts, 3D printing is particularly cost-effective compared to traditional manufacturing methods.
-
What materials are suitable for aerospace 3D
printing?
- Materials suitable for aerospace 3D printing include: Metals: Titanium alloys, aluminum alloys, Inconel (nickel-based superalloys), and stainless steel. Polymers: High-performance thermoplastics like PEEK and ULTEM (PEI). Composites: Carbon fiber-reinforced materials for strength and weight reduction. Ceramics: For high-temperature applications.
-
Which 3D printing technologies are ideal for aerospace
applications?
- Selective Laser Melting (SLM)/Direct Metal Laser Sintering (DMLS): For metal parts with high strength and complex geometries. Electron Beam Melting (EBM): Suitable for high-temperature materials like titanium. Fused Deposition Modeling (FDM): Using high-performance thermoplastics for lightweight components. Selective Laser Sintering (SLS): For producing durable plastic parts. Stereolithography (SLA): For creating high-precision prototypes.
-
Can high-temperature materials be 3D printed for
aerospace use?
- Yes, materials like Inconel, titanium alloys, and certain ceramics that can withstand high temperatures are 3D printed for aerospace applications. These materials maintain their mechanical properties under extreme conditions, making them suitable for engine components and parts exposed to thermal stress.
-
How do material properties impact 3D printed aerospace
parts?
- Material properties such as strength, heat resistance, weight, and fatigue resistance are critical in aerospace applications. Selecting the appropriate material ensures that 3D printed parts can withstand operational stresses, temperature extremes, and environmental factors while meeting safety and performance standards.
-
Is metal 3D printing reliable for producing
flight-critical components?
- Yes, metal 3D printing has advanced to the point where it is reliable for producing flight-critical components. With rigorous process control, quality assurance, and certification, metal additive manufacturing can produce parts that meet or exceed the mechanical properties required for aerospace use.
-
How does 3D printing enable complex geometries in
aerospace design?
- 3D printing allows engineers to design parts with intricate geometries, internal channels, and lattice structures that are impossible or impractical with traditional manufacturing methods. This design freedom enables the optimization of components for weight reduction, improved performance, and integration of multiple functions into a single part.
-
What is topology optimization in aerospace 3D
printing?
- Topology optimization is a computational design process that optimizes material layout within a given design space for a set of performance criteria, such as minimum weight or maximum stiffness. In aerospace 3D printing, topology optimization helps create lightweight components that retain necessary strength and functionality, contributing to overall aircraft efficiency.
-
How does additive manufacturing support rapid prototyping
in aerospace?
- Additive manufacturing enables the quick production of prototypes directly from digital models without the need for tooling. This accelerates the design iteration process, allowing engineers to test and refine components more efficiently, reducing development time and costs in aerospace projects.
-
Can 3D printing be used for custom aerospace tooling and
fixtures?
- Yes, 3D printing is ideal for creating custom tooling, jigs, and fixtures used in aerospace manufacturing and assembly processes. Additive manufacturing allows for rapid production of specialized tools tailored to specific tasks, improving efficiency and reducing lead times.
-
What role does 3D printing play in space exploration
missions?
- 3D printing is crucial in space exploration for producing lightweight, complex components for spacecraft, satellites, and space stations. Additive manufacturing enables on-demand production of parts in space, reduces payload weight, and supports innovative designs that enhance mission capabilities.
-
How is 3D printing integrated into aerospace
manufacturing processes?
- Integration involves: Identifying Suitable Applications: Focusing on components where 3D printing offers clear benefits. Process Development: Establishing additive manufacturing workflows and quality control procedures. Equipment Investment: Setting up in-house facilities or partnering with specialized service providers. Training Personnel: Educating staff on design, production, and post-processing for additive manufacturing. Certification Compliance: Ensuring parts meet regulatory standards through rigorous testing and documentation.
-
What are the challenges of adopting 3D printing in the
aerospace industry?
- Challenges include: High Initial Costs: Investment in equipment and technology can be substantial. Material Limitations: Limited availability of certified aerospace-grade materials. Regulatory Hurdles: Strict certification requirements for flight-critical parts. Quality Assurance: Ensuring consistent part quality and repeatability. Knowledge Gap: Need for specialized expertise in additive manufacturing.
-
Can 3D printing reduce lead times in aerospace
production?
- Yes, 3D printing can significantly reduce lead times by eliminating the need for tooling, enabling rapid prototyping, and allowing for on-demand production. This accelerates the development cycle, enabling faster time-to-market for new aerospace components.
-
How does 3D printing affect the aerospace supply
chain?
- 3D printing streamlines the supply chain by: Reducing Inventory: On-demand production lowers the need for stockpiling parts. Simplifying Logistics: Parts can be produced closer to the point of use or even on-site. Enhancing Flexibility: Quick adaptation to design changes and customization. Localizing Production: Decreasing dependency on global supply chains.
-
Are there regulatory considerations for 3D printed
aerospace parts?
- Yes, aerospace components must meet strict regulatory standards set by authorities like the FAA or EASA. Certification involves extensive testing to verify that 3D printed parts meet safety, reliability, and performance requirements. Manufacturers must document processes and ensure traceability for compliance.
-
How is quality assurance managed for 3D printed aerospace
components?
- Quality assurance involves: Process Control: Monitoring printing parameters to ensure consistency. Material Certification: Using aerospace-grade materials with traceability. Post-Processing: Applying heat treatments and finishing processes to meet specifications. Inspection and Testing: Non-destructive testing (NDT), dimensional analysis, and mechanical testing. Documentation: Maintaining detailed records for traceability and compliance.
-
Do 3D printed aerospace parts meet certification
requirements?
- Yes, when produced under controlled conditions with proper quality management, 3D printed parts can meet certification requirements. Components undergo rigorous testing and validation to ensure they comply with industry standards and regulations for aerospace applications.
-
What testing is performed on 3D printed aerospace
components?
- Testing includes: Mechanical Testing: Assessing tensile strength, fatigue, and fracture toughness. Thermal Testing: Evaluating performance under temperature extremes. Dimensional Inspection: Ensuring parts meet precise specifications. Non-Destructive Testing (NDT): Methods like X-ray CT scanning to detect internal defects. Material Analysis: Verifying material composition and properties.
-
How does post-processing enhance aerospace 3D printed
parts?
- Post-processing improves parts by: Enhancing Mechanical Properties: Heat treatments like annealing or hot isostatic pressing (HIP) increase strength and reduce internal stresses. Improving Surface Finish: Machining, polishing, or coating enhances surface quality. Meeting Tolerances: Precision machining achieves exact dimensions. Applying Protective Coatings: Surface treatments protect against corrosion and wear.
-
Can 3D printed parts withstand the demands of aerospace
applications?
- Yes, when designed appropriately and manufactured using suitable materials and processes, 3D printed parts can meet the demanding conditions of aerospace applications. They can withstand high stresses, temperature extremes, and fatigue loads required for safe and reliable operation in aircraft and spacecraft.
Blogs
Explore Our latest Blogs
Explore our latest blogs and articles, highlighting cutting-edge 3D printing and design developments. Discover insights, success stories, and industry trends that showcase our expertise.