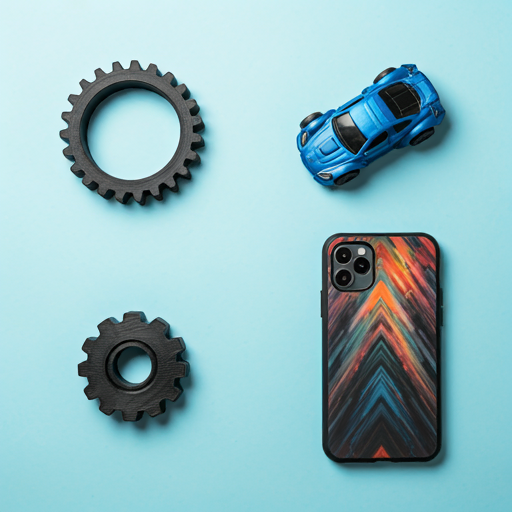
Introduction to 3D Printing Technology should you Opt for
While choosing the right 3D printing technology, it is crucial to achieve the desired quality, cost-effectiveness, and feasibility of your project. Among the various options available, Fused Deposition Modeling (FDM) stands out for its affordability and ease of use, making it ideal for prototyping, educational purposes, and producing functional parts. FDM works by extruding thermoplastic filament through a heated nozzle, layer by layer, creating objects with a focus on cost efficiency. While it offers a wide range of materials like PLA, ABS, and PETG, it tends to produce lower resolution and surface finishes compared to other technologies, often requiring post-processing.
For projects demanding high detail and smooth finishes, Stereolithography (SLA) and Selective Laser Sintering (SLS) are superior choices. SLA uses a laser to cure liquid resin, creating highly detailed and intricate parts, making it perfect for applications like jewelry, dental models, and finely detailed prototypes. However, it is more expensive and limited in material options. On the other hand, SLS uses a laser to sinter powdered material, producing strong, durable parts without needing support structures. This makes it suitable for functional prototypes and small to medium production runs, although it comes at a higher cost and requires longer production times. Understanding the strengths and limitations of each technology helps in selecting the most appropriate method to meet your project's specific needs.
Let's get started!!

Types of 3D printing Technologies
- Fused Deposition Modeling (FDM)
- Stereolithography (SLA)
- Selective Laser Sintering (SLS)
- Digital Light Process (DLP)
- Multi Jet Fusion (MJF)
- PolyJet
- Direct Metal Laser Sintering (DMLS)
- Electron Beam Melting (EBM)

In this article we will provide a quick introduction to the first 3 topics.
Fused Deposition Modeling (FDM)
Fused Deposition Modeling (FDM) is one of the most widely used 3D printing technologies due to its affordability and accessibility. It operates by extruding thermoplastic filament through a heated nozzle, depositing material layer by layer to build the desired object. FDM is particularly well-suited for rapid prototyping, educational purposes, and creating functional parts. It supports a variety of materials, including PLA, ABS, PETG, and TPU, making it versatile for different applications. The technology is user-friendly, with many affordable desktop models available, which has contributed to its popularity in both professional and hobbyist communities.
However, FDM does have some limitations along with benefits. The resolution and surface finish of FDM prints are generally lower compared to other 3D printing technologies like Stereolithography (SLA) or Selective Laser Sintering (SLS). The layer lines can be visible, and the parts often require post-processing, such as sanding or acetone vapor smoothing, to achieve a better finish. Despite these drawbacks, FDM remains a practical choice for many users due to its low cost, ease of use, and the broad range of materials it can print with. For those needing functional prototypes or parts quickly and affordably, FDM is a reliable and effective option.
Stereolithography (SLA)
Stereolithography (SLA) is a 3D printing technology renowned for its ability to produce high-resolution, intricate, and finely detailed parts. SLA works by using a laser to cure liquid photopolymer resin into solid plastic, building objects layer by layer. This method is particularly effective for applications requiring precision and smooth surface finishes, such as jewelry, dental models, and detailed prototypes. The high level of detail achievable with SLA makes it ideal for creating complex geometries and parts with fine features that would be challenging to produce with other 3D printing technologies.
However, SLA does come with some limitations. The materials used in SLA are typically more expensive than those for Fused Deposition Modeling (FDM), and the resins can be messy and require careful handling. Additionally, post-processing is often needed to remove support structures and to cure the printed parts fully, adding to the overall production time. Despite these challenges, the exceptional quality and detail that SLA can achieve make it a preferred choice for projects where precision and surface finish are paramount. For professionals in fields like dentistry, jewelry design, and engineering, SLA offers a reliable solution for producing highly detailed and accurate prototypes and parts.
Selective Laser Sintering (SLS)
Selective Laser Sintering (SLS) is a highly versatile 3D printing technology that excels in producing strong, durable parts with complex geometries. SLS operates by using a laser to sinter powdered materials, such as nylon or polyamides, layer by layer to create solid structures. One of the significant advantages of SLS is that it does not require support structures, as the unsintered powder surrounding the part provides the necessary support during the printing process. This capability makes SLS ideal for producing intricate and interlocking designs that would be difficult or impossible to achieve with other 3D printing technologies.
The strength and durability of SLS-printed parts make this technology particularly suitable for functional prototypes, small to medium-sized production runs, and end-use components. Industries such as aerospace, automotive, and healthcare often utilize SLS for its ability to produce high-performance parts that can withstand mechanical stress and environmental factors. However, SLS machines and materials tend to be more expensive compared to Fused Deposition Modeling (FDM) and Stereolithography (SLA), and the post-processing can be time-consuming, as excess powder must be removed and parts may need additional finishing. Despite these costs, the ability to create complex, high-quality, and durable parts without the need for support structures makes SLS a powerful tool for professional and industrial applications.
Selecting a Process by Material
3D printing materials usually come in the form of filament, powder or resin (depending on the 3D printing processes used). Polymers (plastics) and metals are the two main 3D printing materials, while other materials (such as ceramics or composites) are also available.
What is material selection process?
Material selection is the process of building any tangible
object. In the context of product design, the main purpose
of material selection is to reduce costs while meeting
product performance objectives.
If the required equipment is already known, choosing a 3D printing process is much easier, as only a few technologies produce parts from the same materials. In such cases, the selection process is usually costly.
Thermoplastics :
Thermoplastics is best suited for active applications, including the production of storage components and functional prototypes.They have good mechanical properties and great impact, abrasion and chemical resistance. They can also be supplemented with carbon, glass or other additives to enhance their physical properties. 3D printed engineering thermoplastics (such as Nylon, PEI and ASA) is more widely used to produce the final components for use in many industrial applications.
SLS components have better mechanical and physical properties and better accuracy, but FDM 3d printing technology is way more economical and has low lead times.

Thermosets(resins) :
Thermosets (frames) are best suited for use in systems where aesthetics are important, as they can produce components with a smooth surface such as injection and fine details.In general, they have high durability but are much brittle than thermoplastics, so they are not suitable for active applications. Special resins are available, designed for engineering applications (which mimic ABS and PP structures) or for dental implants.
Material Jetting produces components with very high accuracy and already smooth, but at a higher cost than SLA / DLP. Both processes use the same acrylic-based acrylic frames.
Metals :
The printed parts of Metal 3D have excellent mechanical features and can operate at high temperatures. The power of freeform 3D printing that makes them ideal for lightweight use of aviation and medical industries.DMLS / SLM components have high mechanical and tolerant features
Due to the added size of the technology, 3D printed parts tend to have anisotropic mechanical properties, which means they will be weak in z-direction. In the functional parts, this feature should be taken into account during design.
Selecting a Process by Use-Case
- When creating a component or type that will interfere with other things, it is important to define the level of patience required. As a sixth rule, choosing a process with high accuracy increases costs. Another option is to eliminate features with critical size or small details after 3D printing (for example by digging holes or pressing threads).
- The total strength of the separation depends on the various mechanical and physical properties. To make the choice easier, the strength of the strength can be used as a guide. When high strength and durability are required, 3D metal printing or FDM printing reinforced with continuous carbon fibers are the best solutions.
- 3D Engineering printing materials are available in specialized areas, such as heat-resistant, flame-resistant, chemical-resistant or certified as material or food safe.
- Flexibility can be defined as high altitude during breaks, where thermoplastics such as TPU are available in SLS and FDM, or as low hardness, where rubber-like materials are obtained by SLA / DLP and Material Jetting.
Visual Appearance
Both SLA / DLP and Material Jetting can produce smooth, injection-mold components as a ground finish. The main difference between the two processes (at no cost) is that the support for Material Jetting melts, while in SLA / DLP it needs to be removed by hand after printing, leaving small marks on the surface that need to be processed (sanded or polished).
-Material Jetting produces completely transparent parts, while printed SLA / DLP parts are transparent and can be processed by post to be 100% clear.
-Parts with special texture, such as wood or metal-like finishes, can be printed using woodfill or metalfill FDM filaments. The rubber-like components are soft (sea hardness <70A) and are able to bend and compress, but fortunately the performance of real rubber.
-Material Jetting and Binder Jetting are the only 3D printing processes currently that offer full colour printing capabilities. Material Jetting is advantageous, as it offers better body building materials and more capabilities. Another way you can draw models after printing or use an FDM printer with dual extrusion capabilities (in two colors only).

Selecting a Process by Manufacturing Capabilities
-The accuracy of the measurement is linked to the level of detail each process can achieve and the built-in quality of each 3D printer. Processes that provide high accuracy can create parts with good features. Industrial grade machines have a higher accuracy and duplication than desktop printers.
The construction size determines the maximum size of the part the printer can produce. For parts that exceed the normal construction size, consider moving to another technology or splitting the part into several parts that can be assembled later.
The need for support structures determines the degree of design freedom. Procedures that do not require support, such as SLS, or soluble support, such as Material Jetting or dual-extrusion FDM (industrial or desktop), have limited limitations and can display free form structures with great ease.
Layer Height
Another important way of selecting the 3d printer is by checking the layer height.

When selecting a 3D printing technology based on layer height, it's essential to understand the primary options: Fused Deposition Modeling (FDM), Stereolithography (SLA), Digital Light Processing (DLP), and Selective Laser Sintering (SLS). FDM is known for its affordability and versatility, with typical layer heights ranging from 0.1mm to 0.3mm. It is particularly suitable for prototyping and functional parts but often results in visible layer lines and lower resolution compared to other technologies.
SLA and DLP both offer higher resolution and smoother surface finishes, with layer heights typically between 0.025mm and 0.1mm. These technologies are ideal for creating detailed models and intricate designs. SLA uses a laser to cure liquid resin, while DLP uses a digital light projector to cure an entire layer at once, making DLP often faster. However, both require post-processing and have higher costs and limited material choices, primarily resins.
Selective Laser Sintering (SLS) operates with layer heights between 0.08mm and 0.15mm and excels in producing functional and durable parts without the need for support structures. This makes it suitable for creating complex geometries and parts with good mechanical properties. SLS uses powdered materials, including plastics and metals, but the equipment and materials are expensive, and the resulting parts typically have a rough surface finish that may require additional processing. For projects requiring high detail and smooth finishes, SLA or DLP are the best options despite their higher cost and post-processing needs. For producing robust, functional prototypes, SLS is the superior choice due to its material versatility and structural integrity. FDM remains the go-to for cost-effective and versatile prototyping, especially for larger parts where extreme detail is not critical. The choice of technology should align with the project's specific requirements, balancing detail, material properties, and budget considerations.
Conclusion
In conclusion, choosing the right 3D printing technology depends on your specific needs and project requirements. For high-detail, smooth surface finishes, Stereolithography (SLA) and Digital Light Processing (DLP) are excellent options. These technologies offer superior resolution and are ideal for intricate designs, but they require a higher investment and post-processing due to the use of resin materials. If your priority is producing functional, durable parts, Selective Laser Sintering (SLS) is a standout choice. SLS can handle complex geometries without the need for support structures, making it suitable for robust, mechanical parts. However, it comes with a higher cost and often results in a rougher surface finish that may require additional processing to achieve the desired quality. For versatile and cost-effective prototyping, Fused Deposition Modeling (FDM) is a reliable option. It is particularly suited for larger parts where extreme detail is not critical. FDM offers a wide range of materials and is the most budget-friendly, making it a popular choice for general prototyping needs. Ultimately, your decision should balance the need for detail, material properties, and budget to ensure the best outcome for your project.
For any further questions about selecting the best 3D printing technology, we encourage you to visit our website https://iamrapid.com. It's crucial to understand the key aspects of 3D printing, such as material selection, design optimization, rapid prototyping, and customization, to achieve outstanding results tailored to your specific needs. Whether you prioritize high-detail models, functional prototypes, or cost-effective solutions, choosing the right 3D printing method ensures reliable performance and efficiency for your projects. If you're interested in exploring our 3D printing services, please contact us at https://iamrapid.com. Share your design specifications, material preferences, or any specific requirements, and we'll help you find the optimal solutions for your needs.
Feel free to share this valuable information with others to enhance their understanding of how various 3D printing technologies contribute to successful applications in different fields.