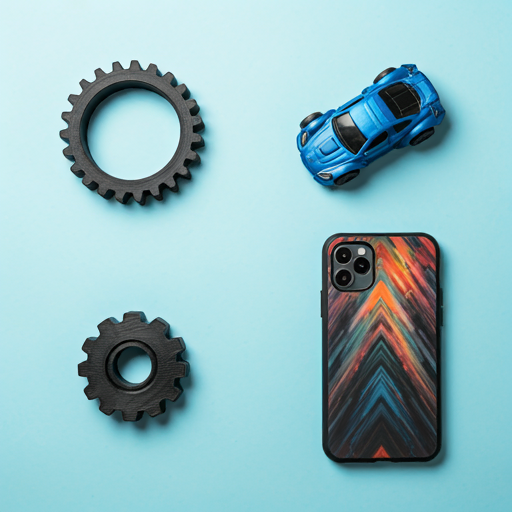
Introduction to Understanding 3D Printing Support Structures
In 3D printing, support structures play a crucial role in ensuring the success of complex prints. These temporary structures provide the necessary backing to a model's overhangs, holes, bridges, or intricate parts, preventing warping, sagging, or complete failure during printing.
In metal 3D printing, support structures provide physical stability and function as heat dissipators. They help manage the high temperatures involved in additive manufacturing by drawing heat away from the printed part, thereby reducing
Understanding when and why to use support structures can significantly enhance the quality and precision of your 3D prints. This article will delve into the various types of support structures, their importance, and how to optimize their use to achieve the best possible results in your 3D printing projects. Whether you're a novice or an experienced 3D printing enthusiast, this guide will equip you with the knowledge to make informed decisions about support structures in your future prints.
A Brief Overview
3D printing technology, a form of additive manufacturing, involves adding material layer by layer to form the component eventually. Due to the complexity of the shape or part to be manufactured, it becomes necessary to print the part along with support structures to hold the part or portions of the element in place until they solidify or until the entire printing process is complete.
Support structures are crucial for optimizing 3D printing and avoiding failures in the model. These structures must be easy to remove, typically using low-density material to ensure minimal impact on the final print.

The supports are usually printed from the same material as the parent structure. Still, sometimes, unique materials are used to preserve the surface finish of the parent element once the support is removed. Common materials for printing support structures include Acrylonitrile Butadiene Styrene (ABS), Polylactic Acid (PLA), and Polycarbonate (PC).
Note : Since these supports are not part of the final model, they must be removed after printing through post-processing techniques. Thus, choosing the best material for support structures is essential.
Thankfully, various support structure options and standard criteria for printing supports for particular elements or parts exist.
Why Should You Read This ?
This guide will be invaluable if you are an additive manufacturing enthusiast looking to learn more about printing without failure.
You will learn about:
- The use of supports in 3D printing,
- Explore various 3D printing supports, and
- Gain detailed insights into 3D printing techniques utilizing these supports.
Let's start exploring! We help you optimize your 3D printing by providing sufficient information before you begin.
Basic Rules of Support Structures
In most cases, supports are designed to hold the material in position for most of the printing. The most important aspect is that they must be easy to remove and should not pose any major drawback in terms of machining time or surface finish defects once removed.
Depending on the kind of design and cost-effectiveness, we need to decide at what points and to what degree support structure must be provided; this should be taken care of during the design of the component.
Typically, if your model includes an overhang or a bridge without underlying support, supports may be necessary for successful 3D printing. The letters Y, H, and T illustrate examples of overhangs and bridges.
Refer the "YHT" Illustration below. **The support material is shown in light gray.**

Not all overhangs require support. The general guideline is that if an overhang is tilted at an angle less than 45 degrees from the vertical, it can typically be printed without supports.

However, overhangs exceeding a 45-degree angle from the vertical need support structures. This is because 3D printers employ a minimal horizontal offset between consecutive layers, which is barely noticeable. As a result, a layer only loads perfectly over the previous one if a vertical wall is present. This allows the printer to handle overhangs that do not deviate significantly from the vertical. The preceding layers can support overhangs at angles less than 45 degrees, whereas those exceeding this angle cannot. Hence, 45 degrees is often considered the threshold for failure.
An FDM printer can easily print the arms of the letter "Y" **without** needing support structures, as these outstretched features do not extend beyond 45 degrees, As shown in the "YHT" illustration above.
Conversely, the overhangs in the letter "T" form a 90-degree angle with the vertical. Therefore, supports are necessary to print the letter T; As shown in the "YHT" illustration above.
The 10 mm Rule on Bridges
Similar to overhangs, not all bridges need support. The general guideline is that if a bridge is less than 10 mm long, it can often be printed without supports. Printers achieve this using bridging, where the hot material is stretched over short distances, allowing the printer to print the bridge with minimal sagging.
However, this technique becomes ineffective if a bridge exceeds 10 mm in length. In such cases, supports are necessary to prevent sagging.

This distance is a general guideline. Adjustments to parameters, particularly active cooling and print speed, can significantly enhance the printer's ability to produce bridges that extend well beyond the 10 mm threshold.
Lets understand this with the letter H. If the central bridge in "H" is less than 10 mm, it can be printed without support or sagging. For bridges longer than 10 mm, support structures become necessary. In the "YHT" illustration provided above, the central bridge exceeds 10 mm, so it is printed with supports.
Here are the appearances of these models when printed. The second image demonstrates the result of printing the letter "T" without support, showing significant sagging on the surface, necessitating extensive post-processing.
Here are the appearances of these models when printed. The first image shows the result of printing the letters Y H T without supports, where the overhang angle of Y is 50 degrees, the bridge distance of H is 11 mm, and the overhang angle of T is 90 degrees, with the length of its arms being 11 mm each. So, with these parameters, the printer was bound to fail, and we can see the mess created. These results are subject to the printer's performance, but the above-mentioned basic rules should be followed with most FDM printers.
The subsequent series of images showcases the same letters Y H T, this time printed with supports. The absence of any printing issues and the expected results underscore the crucial role of supports in determining the success or failure of even the most basic prints.
In the third set of images, we again tried printing Y H T without supports, but this time, we kept the overhang angle on Y at 30 degrees, which is well below the 45-degree mark. We also changed the bridge distance of H to 6 mm, again below the 10 mm threshold mark; and to experiment with the printers ability, we printed the letter T again without supports obviously, but with the length of its arms as 6 mm each, the overhang angle still being the same which is 90 degrees. Ideally, it shouldn't have been printed correctly without support, but the results were surprising as it did a pretty decent job, although it was not perfect. This again shows that support plays a vital role in the print quality.






Shown below is an example of complete failure in printing

Evaluating Your Printer's Performance
The suggested angles for overhangs and bridges are flexible. Your printer's abilities, maintenance, and the type of material being used all play a significant role. Printers that are not well-maintained may encounter difficulties with overhangs at 35—or 40-degree angles from the vertical, while accurately calibrated printers can manage much steeper overhangs and bridges. Therefore, it is a good idea to evaluate your printer's performance before attempting to print intricate models.
Types of Support Structures
By Geometry
There are two common types of support structures: lattice and tree-like supports:
Lattice Support
Also known as linear support, this is the most common type of support used in 3D printing. It consists of vertical pillars that make contact with the entire overhang length. This type of support works for almost every overhang and bridge. However, it is more difficult to remove and is more likely to damage the model's surface.

Tree-like Support
Tree-like support features a structure resembling a tree, supporting the model's overhangs. This support type only contacts the overhang at specific points.
The advantage of tree-like support is that it is easier to remove and causes less damage to the underside of the overhang. However, it is suitable only for non-flat overhangs, such as nose tips, fingertips, or arches, typically found in more organic models. It does not offer sufficient stability for flat overhangs.

By Ease of Removal
There are two types of supports classified by ease of removal: Break-away and dissolvable supports:
Break-Away Support Structures for Single Extruder Printers
Printers with a single extruder use break-away support structures by default.
With a single extruder, the same material used for the model must also be used for the support structures. While you can adjust the density of the supports to be lower than that of the model, this is the only control you have over the support material.

Since both the model and the supports are made from the same material, the only way to remove the supports is to break them off by hand or carefully cut them with a knife.
These removal methods pose a significant risk of damaging the model, requiring careful technique and extreme vigilance during the removal process.
Dissolvable Support Structures for Dual Extruder Printers
Dissolvable support structures are easier to remove but require a dual extruder printer.
With a dual extruder printer, you can load one extruder with PLA for the model and the other with a water-soluble material like PVA or a Limonene-soluble material like HIPS for the supports. After printing, you can dissolve the supports by immersing the model in water or Limonene.
This method reduces the risk of damaging the model and simplifies post-processing, making it ideal for complex prints.

Support Structure Patterns

When you, as the designer, are creating supports, it's crucial to consider the shape's strength, ease of removal, and compatibility. The slicing software provides various patterns and densities with which you can experiment. To adjust the pattern, access the hidden 'Support Pattern' setting in the Settings section to quickly apply this knowledge in your 3D printing projects.
- The Zig-Zag pattern is the quickest to print and the easiest to remove.
- Lines pattern is the next step up. They are relatively easy to remove but slightly more potent than zig-zag patterns.
- Concentric pattern is best for models with shapes near spheres or cylinders. It is more potent than zig-zag and lines.
- Triangle pattern offers great structural strength and is, hence, tough to remove, but since its overall strength is excellent, it is used for many critical sections.
- The Grid pattern is more rigid than lines and zig-zags, offering strong, stable support but more challenging to remove.
Support Structure Density

Like infill density, support density influences speed, ease of removal, and strength in 3D printing.
High-Density Support
High-density supports are rigid and perfect for high-detail models. They provide more reliable support, although they increase printing time. Post-processing also takes longer with high-density supports.
Low-Density Supports
Low-density supports are ideal for areas that don't require extensive contact points. They reduce printing costs and allow for faster removal. A support density of 20% is generally acceptable for these purposes.
Disadvantages of Support
Now that we have understood the know-how of supports in 3D printed models let's examine how they affect the final product. Despite their necessity, supports can introduce certain drawbacks that impact the finished model's overall quality, efficiency, and aesthetics. Let's explore these disadvantages in detail.
Increased Material Cost
While necessary, support structures can increase the material cost of 3D printing as they consume extra material that is later discarded. This, in turn, raises the overall production cost of the model. The price per part is critical for hobbyists and those in production settings. However, by strategically minimizing the use of supports, you can reduce these costs and maintain control over your production budget.
Specialized materials, such as carbon-fiber-reinforced filaments, can further drive up costs, making exploring options like dual extruders beneficial. These allow the printer to switch between different materials, potentially reducing waste and expense.

Increased Print Duration
Support structures also contribute to longer print durations, another cost factor. While operating costs for FDM 3D printers aren't excessively high, extended print times, especially for volume production, can add up. In some instances, using more support than necessary can ensure a successful print on the first try, which might be more efficient than multiple failed attempts.

Additional Post-processing
After printing, support structures need to be removed, which adds to post-processing work. This additional task increases the overall production cost, mainly if the supports are in hard-to-reach places or need to be separated easily from the model. In some cases, removing supports can even damage the model. Consider using soluble supports or integrating supports into the design to reduce post-processing time.

Risk of Damaging the Model
Support structures often adhere to the downward-facing surfaces of models to provide necessary support. However, removing them can sometimes leave blemishes or even cause parts of the model to break.

Note : To avoid such issues, it's best to minimize the use of supports and only add them where necessary. In the following sections, we'll explore how to apply this approach from the CAD design phase through to the printing phase.
How to Minimize Support Structures
Minimize Support Structures Through Design
-
Integrate Supports into the Model
A clever way to avoid using traditional support structures is to incorporate supportive elements directly into the model's design. Sculptors have utilized this technique for centuries. For example, consider Antonio Canova's "Venus Vitrix" sculpture.

In this sculpture, the right arm, an overhang, is supported by pillows, while the left leg is supported by bunched togas, effectively acting as built-in supports.
Another example is a model called "The Guardian" by designer Fantasygraph. Here, the legs and buttocks are supported by a flowing gown, and the spear attached to the bottom supports the left arm.

Integrating support elements into the design requires creativity and technical skill. These elements must fit into the overall design and provide the necessary support for overhangs or bridges. When done correctly, this approach enhances the model's aesthetic appeal and eliminates the need for separate support structures, thereby saving time, money, and effort.
-
Chamfers
Chamfers offer another method to eliminate the need for support. They transform problematic overhangs into manageable ones with angles less than 45 degrees.

For instance, a gently sloping or curved edge can be replaced with an angular edge, creating a chamfer that doesn't require support.
Similarly, the model's holes can be redesigned as chamfered holes in a teardrop shape. This modification typically doesn't affect the model's overall aesthetics but significantly reduces the need for supports during printing.

Integrating support elements into the design requires creativity and technical skill. These elements must fit into the overall design and provide the necessary support for overhangs or bridges. When done correctly, this approach enhances the model's aesthetic appeal and eliminates the need for separate support structures, thereby saving time, money, and effort.
Minimize Support Structures Through Re-Orientation
Reducing the need for support structures can often be achieved simply by reorienting the model on the print bed. For instance, consider printing an open box with its open face positioned at the top, as shown below.

By strategically adjusting the orientation of your model, you can optimize how layers are built during printing. This can minimize or eliminate the need for support in certain areas.
Moreover, re-orientation affects support requirements and influences other aspects of the print, such as overall strength and surface finish. It's a technique that combines practicality with an understanding of how the printing process interacts with design elements.
Factors such as the intended use, structural integrity, and aesthetic considerations should be considered when re-orienting a model. Experimenting with different orientations during the design phase can significantly improve print quality and efficiency.
How to Remove Breakaway Supports for FDM
Manual Removal:
Identify exposed support structures and gently break them away using your fingers. Carefully maneuver to ensure most of the support structure comes off easily.
Tools for Hard-to-Reach Areas:
Use tools like needle-nose pliers, putty-type knives, or an Exacto knife for difficult-to-access support structures. Heating the tool or the model slightly can make the supports easier to slice through. Exercise caution with sharp tools like Exacto knives.
Sanding for Finishing:
Use sandpaper, preferably wet sanding with high grits (220 to 1200), to smooth out any remaining bumps and polish the model. Apply water to the part and sand gently until the desired surface quality is achieved.
These steps ensure the effective removal of breakaway supports while maintaining the integrity and appearance of your printed models.
Are Support Structure Required for All 3D Printing Tecgnologies?
Most 3D printing technologies require support structures to some extent. The table below shows which technologies require support.

So far, the discussed points primarily pertain to FDM printing technologies. Now, let's explore the roles of support structures in other additive manufacturing technologies.
Role Of Support Structures In Stereo Lithography (SLA) & Digital Light Processing (DLP)


Stereolithography (SLA) and Digital Light Processing (DLP) are advanced 3D printing technologies that create objects from liquid photopolymer resin using a light source to solidify the material.
SLA and DLP printers operate by pulling a model out of a vat containing liquid resin and solidifying it through a light source from below (bottom-up) or submerging the model into the resin. At the same time, the top layer is cured by light from above (top-down).
Support structures, a key component of SLA and DLP printers, are not just essential, but they are also highly efficient.
- They ensure that prints adhere to the build platform and maintain their intended shape during printing.
- These supports are designed as thin ribs, with minimal contact points on the model to conserve material and reduce printing time, providing a streamlined and efficient printing process
- Based on their count, these Supports can be Low, Medium, and High-density.

Despite the need for supports, SLA and DLP technologies are renowned for their high accuracy and can produce intricate and finely detailed objects. Proper post-processing techniques can effectively remove supports without compromising the quality of the final printed part.

Removing Support Materials from SLA & DLP Prints
Breakaway techniques or Dissolvable materials are mostly used here too,the methods are chosen depending upon the kind of complexity of design and surface finish required .
To remove support materials from SLA and DLP prints, follow these steps:
- Clean the finished parts by rinsing off any residual liquid resin with isopropyl alcohol (IPA).
- Remove the support structures either by breaking them off from the surface of the model or using pliers to carefully detach them.
- After removing the supports, sand down the areas where the supports were in contact with the object to eliminate any remaining marks or roughness.
These steps ensure that the final printed objects are smooth and free from any visible traces of support structures, resulting in a clean and finished appearance.
Role Of Support Structures In Metal Printing (SLM, EBM, DMLS, DED)

Powder Bed Fusion (SLM, DMLS, EBM)
Metal powder bed fusion technologies, such as Selective Laser Melting (SLM), Direct Metal Laser Sintering (DMLS), and Electron Beam Melting (EBM), involve surrounding 3D printed parts with loose powder. Supports are crucial in these processes to anchor parts to the base plate and manage residual stresses effectively.
Supports are strategically placed at the contact area between the bottom of the printed part and the build plate, where residual stress concentration is highest. This placement helps dissipate heat from the part, minimizing thermal distortion which can lead to issues like cracking, warping, and delamination.
Direct Energy Deposition (DED)
Direct Energy Deposition encompasses various metal 3D printing technologies that melt and fuse materials to build parts. Similar to powder bed fusion methods, DED printing requires support structures to ensure part stability, enable complex feature printability, and facilitate thermal dissipation.
Support Design and Removal
-
Design Considerations :
Supports for metal parts are typically lattice structures designed for accessibility during post-processing support removal. These structures act as heat sinks, aiding controlled cooling to prevent distortion and optimize material usage and build time.
-
Support Removal :
Removing supports from metal parts is generally challenging and requires precise cutting tools. Achieving a smooth surface finish may also involve additional post-processing steps such as sanding.

Role Of Support Structures In Material Jetting

Support structures are necessary for Material Jetting technologies. Similar to inkjet printing, these 3D printers jet layers of liquid photopolymer onto a build tray and cure them instantly using UV light.
Supports are essential whenever there are overhanging features, regardless of their angle. They can be water-soluble or removed during post-processing using methods like plyers, water jetting, ultrasonic baths, and sandblasting.
Unlike FDM printing, supports in Material Jetting do not compromise a part’s cosmetic appearance, surface quality, or technical properties. With proper post-processing, it is nearly impossible to discern where support materials were removed from the final part.
The videos below will help you better understand support structures in the 3D printing process.
Conclusion
support structures is essential for achieving successful outcomes in additive manufacturing. These supports enable the creation of complex geometries and intricate details, ensuring print stability and minimizing distortions. While they increase material costs and require post-processing, their benefits in producing high-quality, functional parts are significant. Mastering support structure design is key to optimizing print processes and maximizing the potential of 3D printing technologies.
Explore the world of 3D printing and discover more at our website https://iamrapid.com. Experience our seamless 3D printing services, where you can get instant and transparent quotations within seconds.
Get your 3D model printed today at https://iamrapid.com