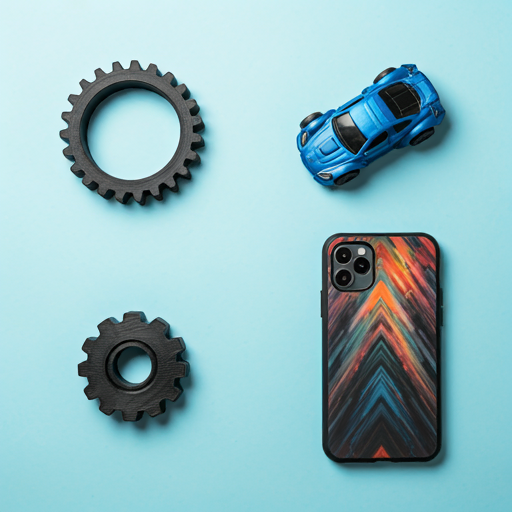
Introduction to Post Processing FDM Printed Parts

Fused Deposition Modeling (FDM) is a popular 3D printing technique known for its simplicity, cost-effectiveness, and its ability to create durable parts. However, FDM prints often exhibit visible layer lines, surface roughness, and other imperfections that may affect their aesthetic appeal and functional performance. Post-processing techniques are crucial for enhancing the quality and functionality of FDM parts, making them suitable for a wider range of applications. This guide provides a comprehensive overview of various post-processing methods, including sanding, chemical smoothing, painting, and assembling, to help users achieve professional-grade results.
Post-processing FDM parts involves a series of steps designed to refine the surface finish, improve mechanical properties, and prepare the parts for their intended use. Sanding is often the first step, which smooths out the layer lines and prepares the surface for further treatments. Chemical smoothing, using solvents like acetone for ABS prints, can significantly enhance surface finish by melting the outer layer of the material. Painting not only adds color but also provides an additional layer of protection. Finally, assembling and bonding different parts can create more complex and functional assemblies. Each post-processing technique offers unique benefits and challenges, and this guide aims to equip users with the knowledge and skills needed to select and apply the most appropriate methods for their specific projects.
Let's start with this!!
Various Post-Processing steps:
Support Removal
Support removal is a critical step in the post-processing of FDM (Fused Deposition Modeling) 3D-printed parts, ensuring that the final product is both functional and aesthetically pleasing. During the FDM printing process, support structures are often necessary to stabilize overhanging or complex features. These supports, while essential for successful printing, need to be carefully removed to avoid damaging the part. The process typically begins with manual removal using tools like pliers or cutters, followed by more precise methods such as sanding or filing to eliminate any remnants and smooth out the surface. Proper support removal not only improves the part’s appearance but also prepares it for subsequent post-processing steps like sanding, painting, or assembly.
For optimal results, it is important to consider the type of support material used. Standard support materials like the same filament as the part (e.g., PLA or ABS) require physical removal, which can be labor-intensive and potentially damaging if not done carefully. The choice of support material and removal method significantly impacts the ease of post-processing and the final quality of the printed part. By understanding and effectively implementing support removal techniques, users can enhance the overall finish and functionality of their FDM prints.Support material can be removed with less effort but it is difficult to reach to some areas like holes,hollow areas, etc. For that we use dental picks and needle nose pillers to reach to the difficult areas.
Tool kit
- Needle-nose pliers
- Dental pick set

Dissolvable Support Removal
Dissolvable support removal is an advanced post-processing technique that offers a streamlined and efficient method for achieving smooth, high-quality surfaces on FDM (Fused Deposition Modeling) 3D-printed parts. Unlike traditional supports, which are made from the same material as the printed object and require manual removal, dissolvable supports are made from a different material designed to dissolve in a specific solvent. Common dissolvable support materials include PVA (Polyvinyl Alcohol) and HIPS (High Impact Polystyrene), which dissolve in water and limonene, respectively. This method is particularly beneficial for complex prints with intricate geometries, as it eliminates the risk of damaging delicate features during support removal.
The process of dissolvable support removal begins by submerging the printed part in the appropriate solvent. For PVA supports, simply soaking the part in warm water for several hours will cause the supports to dissolve completely. For HIPS supports, the part is soaked in a limonene solution. This method is not only more efficient but also yields a cleaner and more polished final product, with minimal manual intervention. After the supports have fully dissolved, a quick rinse and a gentle drying process complete the support removal. Utilizing dissolvable supports can significantly enhance the post-processing workflow, making it easier to achieve professional-grade results, especially for complex and detailed prints.
Tool kit
- Solvent-safe container
- Solvent
- Ultrasonic Cleaner (optional)
Note : Accelerate the melting time of the soluble substance using an ultrasonic cleaner, and change the solvent solution when it is full of molten solvents. Use a warm (not hot) solvent will speed up the finishing process if an ultrasonic cleaner is not available.
Sanding
Sanding is a fundamental post-processing technique used to enhance the surface quality of FDM (Fused Deposition Modeling) 3D-printed parts. This method involves the manual or mechanical abrasion of the printed object to remove visible layer lines and achieve a smoother finish. The sanding process typically starts with a coarse grit sandpaper (e.g., 100-200 grit) to quickly eliminate major imperfections and then progresses to finer grits (e.g., 400-600 grit) for more detailed smoothing. This gradual refinement helps to even out the surface without causing significant damage to the part. Wet sanding, using water or a lubricant, can further improve the finish by reducing heat buildup and clogging, resulting in a cleaner and more polished appearance.
For best results, it is crucial to follow a systematic approach when sanding FDM parts. Begin by identifying and focusing on areas with the most pronounced layer lines or rough surfaces. Use a coarse grit sandpaper to sand these areas in a circular or linear motion, ensuring even coverage. Once the major imperfections are addressed, switch to finer grit sandpapers to refine the surface further. Patience and consistent pressure are key to achieving a smooth finish. Additionally, using sanding blocks or sponges can help maintain flat surfaces and avoid uneven sanding. Proper sanding not only improves the aesthetic appeal of the printed part but also prepares it for subsequent post-processing steps such as priming and painting, gap filling, ultimately enhancing the overall quality and functionality of the final product.
Tool kit
- 150, 220, 400, 600, 1000, and 2000 grit sandpaper
- Toothbrush
- Soap
- Face mask

Note: This method is not recommended for prints with 2 or less perimeter shells, as the sanding process may damage the print.
Gap filling
Gap filling is an essential post-processing step for FDM (Fused Deposition Modeling) 3D-printed parts to achieve a smooth, seamless finish. During the printing process, gaps, voids, and imperfections can occur due to various factors such as under-extrusion, layer misalignment, or complex geometries. Filling these gaps not only improves the aesthetic quality of the part but also enhances its structural integrity. Common materials used for gap filling include epoxy, cyanoacrylate (super glue), and specially formulated 3D printing fillers or putties. Applying these materials involves filling the gaps and voids, allowing them to cure or dry, and then sanding the filled areas to achieve a uniform surface.
To effectively fill gaps, start by cleaning the part to remove any dust or debris that could interfere with adhesion. Apply the chosen filler material carefully into the gaps using tools such as spatulas, brushes, or syringes for precision. For larger gaps, multiple applications may be needed, allowing each layer to dry before adding the next. Once the filler is fully cured, sand the area with progressively finer grits of sandpaper to blend the filled sections with the surrounding surface. Proper gap filling not only improves the visual appeal of FDM prints but also prepares the part for further finishing processes, ensuring a high-quality, professional-grade result.
Tool kit
- Epoxy resin (only for small voids)
- Autobody filler (for large voids and joining)
- ABS filament & acetone (only for small voids and ABS prints)

Note : If gaps appear on the print before adding sand, fill in the blanks with Bond-O or epoxy and the sand when dry. This will greatly reduce the total amount of time required to achieve a smooth surface.
Polishing
Polishing is a crucial post-processing step that enhances the aesthetic and tactile quality of FDM (Fused Deposition Modeling) 3D-printed parts by providing a smooth and glossy finish. After sanding the part to eliminate visible layer lines and surface imperfections, polishing is performed to refine the surface further and achieve a high-gloss or mirror-like finish. This process involves using progressively finer abrasives or polishing compounds to remove microscopic scratches and enhance the part's appearance. Polishing is particularly effective for parts made from materials like PLA, ABS, and PETG, which respond well to mechanical and chemical polishing techniques.
To polish an FDM part, start by ensuring the surface is as smooth as possible through sanding with fine-grit sandpapers (e.g., 800-2000 grit). Next, apply a polishing compound using a soft cloth, buffing pad, or polishing machine. Common polishing compounds include automotive polish, plastic polish, or specialized 3D printing polishing agents. For small or intricate parts, manual polishing with a microfiber cloth can provide excellent results. Apply the compound in circular motions, gradually increasing pressure to enhance the shine. Additionally, chemical polishing methods, such as using acetone vapor for ABS prints, can further smooth and polish the surface by slightly melting the outer layer of the material.
Tool kit
- Plastic polishing compound
- 2000 grit sandpaper
- Tack cloth
- Toothbrush
- Buffing wheel or microfiber cloth
Note : Attach the whipping wheel to a flexible speed Dremel (or other rotating tool, such as a power drill) for polishing small print. A bench press attached to a scanner can be used for more powerful printing, but make sure the print does not stay in one place for too long. This can cause the plastic to melt, due to the collision.
Priming & Painting
Priming and painting are vital post-processing steps that significantly enhance the appearance and durability of FDM (Fused Deposition Modeling) 3D-printed parts. Priming serves as a preparatory layer that fills in minor imperfections and provides a smooth, uniform surface for the paint to adhere to. It helps in achieving a professional finish by masking any remaining layer lines and enhancing the adhesion of the paint. Typically, a spray primer designed for plastic surfaces is used. Once the primer is applied, it’s essential to sand it lightly with fine-grit sandpaper (e.g., 400-600 grit) to ensure a smooth base for the paint.
After priming, painting the FDM part involves applying multiple thin coats of paint to achieve an even and vibrant finish. It's important to choose paints compatible with the 3D print material, such as acrylic or enamel paints. Start by applying a base coat using light, even strokes to avoid drips and ensure uniform coverage. Allow each coat to dry completely before applying the next. For a more durable and glossy finish, a clear coat can be applied as the final layer. This not only protects the paint but also enhances its shine and longevity. Proper ventilation and safety measures, like wearing masks and gloves, are crucial during the painting process to ensure a safe working environment.
Note : This is the process of coating the part with primer.It acts as base for painting.

Vapour Smoothing
Vapor smoothing is an advanced post-processing technique used to achieve a smooth, glossy finish on FDM (Fused Deposition Modeling) 3D-printed parts. This method involves exposing the printed part to solvent vapors, which slightly melt the outer surface of the material, eliminating visible layer lines and surface imperfections. Common solvents used for vapor smoothing include acetone for ABS (Acrylonitrile Butadiene Styrene) and isopropyl alcohol for materials like PLA (Polylactic Acid). The process not only enhances the visual appeal of the parts but also improves their mechanical properties by reducing surface roughness and sealing micro-cracks.
To perform vapor smoothing, the printed part is placed in a controlled environment, such as a vapor chamber, where it is exposed to the solvent vapors. The process requires careful monitoring to prevent overexposure, which can lead to excessive melting and deformation of the part. Typically, the part is suspended above a small amount of solvent, which is heated to create vapors. As the vapors condense on the part's surface, they dissolve the outer layer, resulting in a smooth and shiny finish. After achieving the desired smoothness, the part is removed from the vapor chamber and allowed to air dry and harden. Proper safety precautions, such as working in a well-ventilated area and wearing protective equipment, are essential when handling solvents. Vapor smoothing is particularly effective for enhancing the appearance and durability of ABS parts, making them suitable for applications where aesthetics and surface quality are critical.
Note : This step is way more complex than other steps.It’s also effective and quick..

Dipping
Dipping is a post-processing technique used to enhance the surface finish of FDM (Fused Deposition Modeling) 3D-printed parts by immersing them in a liquid solution. This method can be used for various purposes, such as smoothing, coating, or coloring the printed parts. One common application of dipping is using solvent baths, like acetone for ABS prints, to achieve a smooth, glossy surface by slightly melting the outer layer of the material. Dipping can also involve using paints, resins, or protective coatings to improve
To perform dipping, the printed part is carefully submerged in the chosen solution for a specified period, ensuring even coverage. For solvent dipping, it's important to monitor the immersion time closely to avoid over-melting and potential deformation of the part. After dipping, the part is removed and allowed to air dry, during which the solvent evaporates, leaving a smooth and polished finish. When using paints or resins, the part may require multiple dips and drying cycles to achieve the desired coverage and finish. Proper safety measures, such as using gloves, goggles, and working in a well-ventilated area, are crucial when handling chemicals and solvents. Dipping provides an efficient way to enhance the surface quality and aesthetics of FDM prints, making them suitable for a wider range of applications.
Tool kit
- Solvent-safe container
- Solvent
- Eye hook or small screw
- Heavy gauge sculpting or landscaping wire
- Drying rod or rack
- Face mask & chemical-resistant gloves
Note : One of the most exciting ways to use the deployment of printed FDM 3D components is Hydrographics. Also called Hydro Dipping.
Conclusion

Post-processing is a critical phase in the production of FDM (Fused Deposition Modeling) 3D-printed parts, transforming raw prints into refined, professional-grade objects. Techniques such as support removal, sanding, gap filling, polishing, priming, painting, vapor smoothing, and dipping each play a vital role in enhancing the aesthetic and functional qualities of the printed parts. By carefully selecting and applying these methods, users can address common issues such as visible layer lines, surface roughness, and structural imperfections, achieving results that meet specific project requirements.
The comprehensive guide provided here aims to equip users with the knowledge and skills necessary to effectively post-process their FDM prints. Understanding the benefits and challenges of each technique allows for better decision-making and improved outcomes. Whether for personal projects, prototyping, or professional manufacturing, mastering these post-processing methods can significantly elevate the quality of 3D-printed parts, making them suitable for a wide range of applications. By investing time and effort into proper post-processing, users can unlock the full potential of FDM technology, creating parts that are not only functional but also visually appealing and durable.
For any further questions about how post-processing impacts FDM 3D-printed parts, we invite you to visit our website. Understanding the critical roles of post-processing techniques such as support removal, sanding, gap filling, polishing, priming, painting, vapor smoothing, and dipping is essential for achieving superior quality parts tailored to your specific requirements. Whether your priority is achieving a flawless surface finish, enhancing mechanical properties, or adding functional coatings, selecting the appropriate post-processing methods ensures reliable performance and aesthetic appeal for your projects. If you're interested in exploring our post-processing services for FDM printed parts, please reach out to us at iamrapid. Share your preferences regarding surface finish, mechanical strength, or any specific requirements, and we'll assist you in finding the best solutions for your needs.
Feel free to share this informative content with others to deepen their understanding of how post-processing techniques contribute to successful applications of FDM 3D printing in various industries.