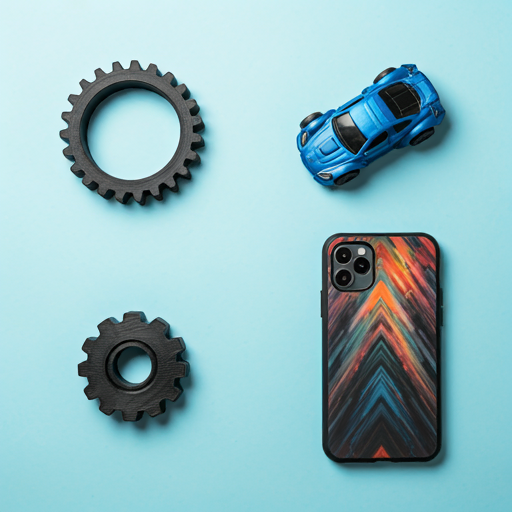
Introduction To CNC Machining
CNC Stands for Computer Numeric Control , and CNC machining is a subtractive manufacturing technique for high accuracy and complex / custom shapes . CNC (Computer Numerical Control) machining is a manufacturing process in which pre-programmed computer software dictates the movement of factory tools and machinery. This process can control a range of complex machinery, from grinders and lathes to mills and routers. With CNC machining, three-dimensional cutting tasks can be accomplished in a single set of prompts.
CNC machining offers remarkable precision, repeatability, and efficiency, making it an essential technology in modern manufacturing. It allows for the creation of complex shapes that would be nearly impossible to achieve with manual machining. The technology is used in various industries, including aerospace, automotive, electronics, and medical device manufacturing, due to its ability to produce high-quality parts with tight tolerances and exceptional surface finishes.
In this blog we will dive deeper into CNC Machining basics, tools and Operations. Let's get started!
CNC Process Guides
CNC (Computer Numerical Control) machining is a manufacturing process in which pre-programmed computer software dictates the movement of factory tools and machinery. This technology is used to control a variety of complex machinery, including grinders, lathes, mills, and routers, enabling the creation of precise and intricate parts. CNC machining is a cornerstone of modern manufacturing, offering unparalleled precision, efficiency, and flexibility.CNC machining can be utilised for machining various materials like wood , plastic , metal, foam and even composites.
The printing phase involves the 3D printer following the G-code to build the object incrementally. Depending on the technology, this might involve extruding thermoplastic filament, curing liquid resin with a UV laser or light projector, or sintering powdered material with a laser. After the object is printed, it undergoes post-processing to achieve the desired properties and finish, which can include removing support structures, surface finishing, and thermal treatments. The final step is quality control, ensuring the printed part meets all required specifications through inspection and testing before deployment or use. This process allows for the creation of complex, custom, and high-quality parts with significant advantages over traditional manufacturing methods in terms of flexibility, efficiency, and material usage.
The general workflow involved in CNC machining irrespective of the material used and operation to be performed is represented as:
- Designing the CAD Model
- Writing the machine code
- Preparing the machine
- Execution Of The codes In The Machine

1.Designing CAD Model
Designing a CAD model for CNC machining involves creating a detailed digital representation of the part or assembly using CAD software. The process begins by defining the geometry, dimensions, and features, ensuring that all specifications are accurate and manufacturable. Key considerations include selecting appropriate materials, incorporating tolerances, and optimizing the design for efficient machining. This can be done by using any standard design softwares like SolidWorks , Catia or AutodeskFusion 360.
2.G-Codes & M-Codes
After the design for the part is finalised , the next step will be to convert the design into a format which can be understood by the machine so that the respective operations can be performed on the workpiece to obtain the design. G-codes and M-codes are integral components of CNC (Computer Numerical Control) programming that dictate the machine's actions.
G-codes control fundamental operations like tool movement and positioning, specifying actions such as rapid movement (G00), linear interpolation (G01), and circular interpolation (G02/G03). M-codes, on the other hand, manage auxiliary functions such as spindle control (M03/M04 for spindle on/off), tool changes (M06), and coolant activation (M08/M09). Together, these codes enable precise and automated machining processes, ensuring efficiency and accuracy in manufacturing operations.
3.Preparing The Machine
Preparing the CNC machine involves a series of crucial steps to ensure it's ready for operation. Initially, the machine is powered on and any necessary safety checks are performed. Next, the workpiece is securely mounted onto the machine table or fixture, ensuring proper alignment and clamping to prevent movement during machining. The cutting tools are selected based on the machining operations required and installed in their respective holders, with tool offsets adjusted as per the program requirements. Finally, the CNC program, containing the G-codes and M-codes for the specific part, is loaded into the machine's control unit.
4.Execution Of Codes
The execution of codes in CNC machining involves the CNC machine interpreting and carrying out the instructions specified in the G-codes and M-codes of the program. Once the program is loaded and all preparations are complete, the machine begins executing the commands sequentially. G-codes dictate the tool movements, such as positioning, cutting paths (linear or circular interpolation), and feed rates, while M-codes control auxiliary functions like spindle rotation, coolant activation, and tool changes.
The machine reads these codes step by step, executing each command to shape and finish the part according to the design. It's like following a recipe where every detail matters to get the final product just right, ensuring precision and consistency in manufacturing.
The codes are entered into the machine and then compiled to check for errors, when the code is found to be error free , it is executed .
Different CNC Operations
Major CNC Operations:
CNC Milling

CNC milling is a manufacturing process where a computer-controlled machine uses rotating cutting tools to remove material from a workpiece. The CNC milling machine operates based on a programmed set of instructions that dictate the tool's movements and cutting paths. It can create precise, complex shapes and features in a wide range of materials, including metals, plastics, and composites.
Milling operations are performed using a milling machine, with axes of operation x, y and z. The part set on a milling system is always stationary , mounted on the bed .
Cutting tool is attached to a spindle which rotates at a predefined speed. The tool then traverses in the x , y and z directions according to the code that is fed to teh system.They are usually designed for contouring operations , tool room work , maintainance purposes or small part productions.
Basic designs for CNC machining centres :
- Vertical Machining Center : A Vertical Machining Center (VMC) features a vertically oriented spindle that allows for easy access to the workpiece and efficient chip removal. Workpieces are clamped onto the machine table, which moves along the X, Y, and Z axes to position the material under the spindle for various operations like milling, drilling, and tapping.
- Horizontal Machining Center : A Horizontal Machining Center (HMC) features a horizontally oriented spindle, allowing efficient machining of parts on multiple sides in a single setup. Workpieces are mounted on a tombstone fixture or pallet system, enabling quick indexing and continuous machining operations. The automatic tool changer (ATC) and pallet changer systems in HMCs enhance productivity by minimizing downtime.
CNC Turning

A CNC Lathe can be very versatile and is often called as a CNC Turning Center.CNC Turning is a machining process where a computer-controlled lathe removes material from a rotating workpiece using stationary cutting tools. The workpiece is clamped into a chuck and rotated at high speeds, while the cutting tool moves along various axes to shape the material into the desired geometry. This process is ideal for producing cylindrical parts and features such as shafts, bolts, and threaded components.A CNC turning center is a machine tool with two axes , the vertical X-axis and the horizontal Z -axis.
The main feature that distinguishes lathe from a mill is that the part rotatee about the machine center line. Modern lathe design can be horizontal or vertical, but horizontal lathes are more commonly used .
CNC Drilling

CNC Drilling is a precision machining process where a computer-controlled machine uses rotating drill bits to create holes in a workpiece. The workpiece is securely mounted on the machine's table, and the CNC program dictates the exact locations, depths, and diameters of the holes to be drilled. The machine's spindle, which holds the drill bit, moves along the X, Y, and Z axes to accurately position the bit and drill into the material. This process can create holes of varying sizes and depths with high accuracy and repeatability. CNC drilling is often used in conjunction with other machining operations, such as milling and tapping, to produce complex parts.The automation and precision of CNC drilling enhance production speed and quality, making it a vital process in modern manufacturing.
Other Operations:
Apart from the major operations mentioned above, the other operations that are possibl;e using CNC Centers are As mentioned below:
Broaching
CNC Broaching is a precision machining process that employs a broach tool with progressively larger cutting teeth to remove material and create specific shapes, such as keyways, splines, and intricate profiles, in a workpiece. Controlled by CNC machines, this process ensures high accuracy and repeatability, making it ideal for producing complex internal and external features with tight tolerances. CNC broaching is versatile, capable of working with various materials including metals and plastics, and is widely used in industries like automotive and aerospace. The automation and precision of CNC broaching enhance production efficiency and yield high-quality surface finishes, making it essential for high-volume manufacturing of detailed mechanical components.
Grinding
CNC Grinding is a high-precision machining process that employs a computer-controlled grinding machine to remove material from a workpiece using a rotating abrasive wheel, achieving exceptional accuracy and surface finish. The CNC system precisely controls the grinding wheel's position, speed, and feed rate, allowing for the creation of intricate shapes and tight tolerances. Versatile and capable of handling various materials, including metals, ceramics, and composites, CNC grinding is used for applications such as surface grinding, cylindrical grinding, and internal grinding.
Honing
CNC Honing is a precision machining process that uses a computer-controlled honing machine to improve the geometric form of a surface and enhance the texture of a workpiece. This process involves the use of abrasive stones mounted on a mandrel that rotates and moves in and out of the workpiece to remove material and achieve the desired finish and size. CNC honing can be used on a wide range of materials, including metals, ceramics, and composites. This versatility makes it suitable for various industries and applications.
Lapping
CNC lapping is a precision machining process where a computer-controlled machine uses a rotating abrasive tool (lapping plate) and a fine-grained abrasive slurry to remove material from a workpiece surface. This process achieves extremely flat and smooth surfaces with very tight tolerances. The CNC system controls the movement of the lapping plate and workpiece, ensuring consistent and uniform material removal across the entire surface. CNC lapping is commonly used for finishing optical components, precision bearings, and semiconductor wafers, where achieving high flatness and surface quality is crucial.
Most Common Cutting Tools for CNC Machining
These cutting tools are selected based on the material being machined, the type of machining operation required, and the desired surface finish and dimensional accuracy. The most common cutting tools used in CNC machining include:

- End Mills : Used for milling operations to remove material from the workpiece. End mills come in various types such as square end mills, ball nose end mills, and flat end mills, each suited for different cutting tasks.
- Drill Bits : Essential for creating holes in the workpiece. CNC drills can perform drilling operations with precise depth and diameter control.
- Turning Tools : Used in CNC lathes for turning operations to shape cylindrical parts. These tools include inserts and holders designed for roughing, finishing, and threading operations.
- Boring Tools :Used to enlarge existing holes or achieve precise internal diameters. Boring tools can be adjustable or solid, depending on the application requirements.
- Reamers : Used for finishing drilled holes to achieve tight tolerances and smooth surfaces. Reamers come in various types such as hand reamers and machine reamers.
- Taps : Used for threading operations to create internal threads in the workpiece. CNC taps ensure accurate thread pitch and depth.
- Milling Cutters : Include various types such as face mills, slab mills, and T-slot cutters, used for specific milling operations like facing, contouring, and slotting.
- Inserts : Replaceable cutting edges used in milling, turning, and boring tools. Inserts are available in different materials and geometries for specific machining applications.
Design Restriction for CNC Machining

Designing for CNC machining involves several key considerations to ensure manufacturability and optimize the machining process. Key design restrictions include:
- Feature Geometry : Sharp internal corners and deep cavities can be challenging to machine with standard tools. Designing internal corners with fillets or radii instead of sharp angles reduces stress on tools and improves machining accuracy. For example, using a 2 mm radius for internal corners allows standard end mills to machine the part without creating stress concentrations.
- Wall Thickness : Thin walls may lead to part deformation or breakage during machining. Maintaining adequate wall thicknesses relative to the material and machining process is crucial. For instance, in aluminum machining, a minimum wall thickness of 1 mm ensures structural integrity and dimensional stability.
- Tolerances : Tight tolerances increase machining complexity and cost. Designing with achievable tolerances based on CNC machine capabilities and material properties is essential. Specify tolerances such as ±0.05 mm for critical dimensions to ensure functional requirements are met without excessive machining costs.
- Surface Finish : Specific surface finish requirements may necessitate additional operations or finer cutting tools. Define surface finish requirements early in the design phase to minimize post-machining operations. For instance, parts requiring a smooth finish might need end mills with high helix angles or subsequent polishing processes.
How Much do CNC Machining Material Cost?
Material | Cost per 6"x6"x1" Block |
---|---|
Aluminum 6061 | $25 |
Aluminum 7075 | $80 |
Stainless Steel 304 | $90 |
ABS (Plastic) | $17 |
Delrin (Plastic) | $27 |
Nylon 6 (Plastic) | $30 |
As we can see, stainless steel 304 costs $90 per block, while a block of ABS plastic is significantly cheaper at just $17. This difference in material costs can greatly impact the total cost of a CNC machining project, especially for larger production runs. Choosing the right material based on the application requirements and budget constraints is crucial for optimizing costs in CNC machining.
Post Processing for CNC Machining

Post-processing in CNC machining encompasses essential steps performed after the primary machining operations to refine and prepare machined parts for their final use. This includes deburring to remove sharp edges and burrs, surface finishing techniques like sanding or coating for desired textures and appearances, heat treatment to enhance material properties, assembly processes for integrating multiple components, rigorous inspection for quality assurance, marking for identification, and proper packaging for shipment. These post-processing activities ensure that CNC machined parts meet precise specifications, functional requirements, and aesthetic standards across diverse industries.
Various post-processing steps like Deburring, surface finishing, heat treatment, etc. contributes to the final quality and functionality of CNC machined parts, meeting customer specifications and industry standards. Effective post-processing management ensures that machined components are ready for use in various applications across industries such as aerospace, automotive, medical, and consumer electronics.
Advantages of CNC Machining
CNC machining offers numerous advantages, making it a preferred manufacturing method for many industries. The key benefits include:
- Precision and Accuracy : CNC machines can produce parts with tight tolerances and high repeatability, ensuring consistent quality and precise dimensions across large production runs.
- Efficiency and Speed : Automation and high-speed cutting capabilities allow for faster production times compared to traditional manual machining, increasing overall efficiency.
- Versatility : CNC machines can work with a wide range of materials, including metals, plastics, and composites, and can perform various operations such as milling, turning, drilling, and grinding.
- Complex Geometries : CNC machining can create intricate and complex shapes that would be difficult or impossible to achieve with manual machining methods, enabling the production of advanced and highly detailed components.
- Reduced Labor Costs : Automated processes require less manual intervention, reducing the need for skilled labor and minimizing the risk of human error, which translates to lower labor costs.
- Scalability : CNC machining is suitable for both small-batch and large-scale production, providing flexibility to scale up operations as demand increases without compromising quality.
- Consistency and Reliability : The repeatable nature of CNC machining ensures that each part is produced to the same specifications, providing high reliability and consistency in manufacturing.
- Improved Safety : CNC machines are designed with safety features and enclosures that protect operators from moving parts and cutting tools, reducing the risk of workplace accidents.
These advantages make CNC machining an essential and highly effective manufacturing process in industries such as aerospace, automotive, medical devices, and electronics, where precision, efficiency, and quality are paramount.
Disadvantages of CNC Machining
While CNC machining offers many advantages, it also has some disadvantages that need to be considered:
- High Initial Cost : CNC machines are expensive to purchase and install, requiring significant capital investment. This includes the cost of the machines, software, and training for operators.
- Maintenance and Repair : CNC machines require regular maintenance to ensure optimal performance. Repairs can be costly and may require specialized technicians, leading to potential downtime.
- Complex Programming : Developing the necessary CNC programs to produce parts can be complex and time-consuming, particularly for intricate designs. Skilled programmers are needed to create and optimize these programs.
- Material Waste : CNC machining involves subtractive manufacturing, where material is removed from a workpiece. This can result in significant material waste, especially for complex parts or those made from expensive materials.
- Limited by Machine Size : The size of parts that can be produced is limited by the working envelope of the CNC machine. Large parts may require specialized equipment or alternative manufacturing methods.
- Setup Time : Initial setup time for CNC machines can be lengthy, particularly for custom or prototype parts. This includes fixturing, tool setup, and program verification.
- Energy Consumption : CNC machines typically consume a considerable amount of energy, which can lead to high operational costs, especially in facilities running multiple machines around the clock.
- Surface Finishing : While CNC machines can achieve high precision, additional post-processing steps such as polishing or coating may be required to achieve desired surface finishes, adding to overall production time and cost.
Considering these disadvantages is important when deciding whether CNC machining is the appropriate method for a given project, balancing the benefits of precision and efficiency against the associated costs and limitations.
Conclusion
In conclusion, CNC machining is a versatile and precise manufacturing process that offers significant advantages, including high precision, efficiency, and the ability to create complex geometries. It is widely used across various industries, such as aerospace, automotive, and medical devices, due to its ability to produce consistent, high-quality parts. However, CNC machining also comes with certain drawbacks, such as high initial costs, the need for skilled programming, and material waste. Despite these challenges, the benefits of CNC machining, particularly its scalability and reliability, make it an indispensable tool in modern manufacturing. By understanding both its capabilities and limitations, businesses can effectively leverage CNC machining to meet their production needs and achieve superior product quality.
If you found this information useful, kindly share it with your peers who are actively involved in innovation. Let's work together to inspire innovation and drive the adoption of this technology. Hope you enjoyed the content we put up. If you have any queries related to CNC machining and its specific applications, or if you would like to reach out to get your design machined, do reach out to us on our official website IamRapid.com .