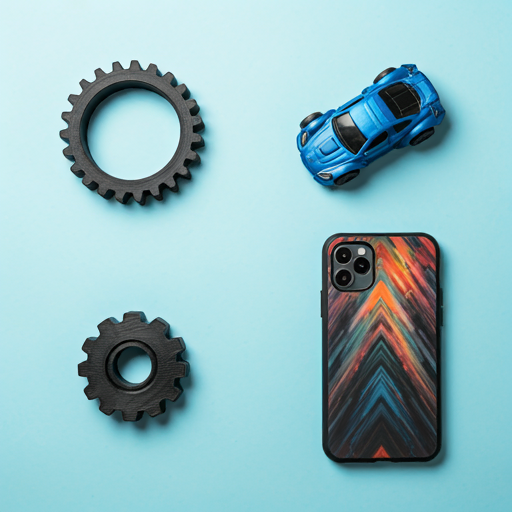
Introduction to 3D Scanning

3D scanning is widely used in various industries today. For example, game and VFX studios are transitioning from traditional modeling to 3D scanned models for their scenes. This shift helps them achieve better results in less time. The automotive industry also extensively utilizes 3D scanning. In transportation design, concept cars are initially clay modeled, then the surfaces are scanned. These scanned surfaces are then imported into software like Autodesk Alias or Catia to create precise surfaces through retopology. Additionally, 3D scanning technology plays a significant role in creating objects for 3D printing.
In this blog we will cover the answers for all your 3d scanning questions.
What is 3D Scanning ?

3D scanning is a transformative technology that allows us to capture the physical world in digital form with remarkable precision and detail. At its core, 3D scanning involves using specialized equipment, such as laser scanners or photogrammetry systems, to capture real-world objects or environments' shape, texture, and appearance. These scanners emit a beam of light or use multiple photographs to capture the object from different angles. The captured data is then processed using sophisticated software algorithms to create a digital 3D model. These models faithfully represent the geometry and surface characteristics of the scanned objects, enabling a wide range of applications across various industries.
One of the most inspiring aspects of 3D scanning is its seamless bridging of the physical and digital realms. By capturing real-world objects in digital form, 3D scanning paves the way for virtual manipulation, analysis, and reproduction of these objects using computer software and hardware. This innovation finds applications in diverse fields such as industrial design, engineering, architecture, archaeology, medicine, entertainment, and more. From creating accurate replicas of ancient artifacts for preservation and study to designing complex engineering components with precise measurements, 3D scanning inspires professionals and enthusiasts alike to interact with the physical world in novel ways.
Moreover, 3D scanning technology continues to evolve rapidly, with ongoing advancements enhancing its accuracy, speed, and accessibility. The future of 3D scanning holds even more exciting possibilities. For instance, the integration of 3D scanning with other technologies like virtual reality and artificial intelligence could open up new avenues for innovation. As hardware becomes more sophisticated and software algorithms more efficient, 3D scanning becomes more accessible to a broader audience, driving innovation and creativity across industries. With its ability to capture reality in digital form, 3D scanning is poised to play a central role in shaping the future of design, manufacturing, healthcare, entertainment, and beyond.
Difference between long range and short range 3D scanning
Long-range and short-range 3D scanners differ in their capabilities and applications. Here's a brief comparison:
Long-range 3D Scanners | Short-range 3D Scanners |
---|---|
Capture data from distances greater than 1 meter | Perform best within 1 meter of the object |
Use laser pulses to measure distance (time-of-flight technology) | Employ laser triangulation or structured light technology |
It is ideal for scanning large objects, structures, or environments | Suitable for capturing smaller objects with high detail |
Provide accuracy in the millimeter range | Offer higher precision, typically in the sub-millimeter range |
Examples: mapping underground structures, monitoring buildings and bridges | Examples: reverse engineering, quality control, medical applications |
Evolution of 3D scanning
The evolution of 3D scanning has been marked by significant advancements in technology, leading to improvements in accuracy, speed, affordability, and accessibility. Here's a brief overview of the key stages in the evolution of 3D scanning:
- Early Development (1960s-1980s) : The foundations of 3D scanning were laid down during this period, with the development of techniques such as laser triangulation and photogrammetry.
- Advancements in Technology (1980s-2000s) : The 1990s saw the commercialization of 3D scanning technology, with the introduction of more accessible and user-friendly systems. Yoshiaki Kakino and Hiroaki Kobayashi developed the first commercial laser scanner in 1980, which utilized laser triangulation for 3D shape measurement.
- Technological Innovation (2010s-2020s) : Advances in sensor technology and computational algorithms led to the development of high-resolution 3D scanners capable of capturing intricate details with greater accuracy. The synergy between 3D scanning and 3D printing technologies enabled rapid prototyping, reverse engineering, and customized manufacturing processes.
How does a 3D scanner work ?
When a 3D scanner is in action, it's like a digital artist capturing the essence of a real-world object. The scanner emits light or laser beams onto the object, which bounce back and are captured by sensors or cameras. By analyzing the geometry and intensity of this reflected light, along with the distance between the scanner and the object, the scanner calculates the three-dimensional coordinates of points on the object's surface. These points are then assembled into a point cloud, a digital representation of the object's shape in three dimensions. Finally, like a master sculptor, specialized software processes the point cloud data to generate a digital 3D model, which can be manipulated, analyzed, or reproduced using computer-aided design (CAD) software or 3D printing technology.
Note: Nowadays, we are using different types of 3d scanning technologies. Let's delve into the various technologies generally used in 3D scanning, and we will explore the principle behind them :
1.Laser 3d scanning

Laser 3D scanning is the most commonly used 3D scanning technique. This technology uses a laser to 3D scan objects to get an accurate 3D model. These can capture incredible details and generate highly accurate point clouds. This technology is the best option for getting precise measurements of complex objects. Even traditional methods will not be able to produce such detailed measurements. This technology is extensively used in various industries, including manufacturing, construction, and archaeology, for quality control, reverse engineering, and heritage preservation applications.In this process, laser dots or lines are projected onto the object, and the sensor measures the distance to the object's surface. After processing, we get a triangulated mesh.
2.Photogrammetry

Photogrammetry is the science of making 3d models from set photos taken from different angles of an object. Photogrammetry is a technique that uses photographs to measure and model the physical characteristics of objects or environments in 3D. By capturing multiple overlapping images from different angles and applying computational algorithms, photogrammetry software reconstructs detailed 3D models and maps. This method leverages the principles of triangulation and perspective geometry to derive spatial information from the photographs.
This method is inaccurate, but we can get optimal results using good photogrammetry software with an excellent feature-matching algorithm.
3.Structured Light Scanning

Structured light scanning is a 3D scanning technology that projects a series of light patterns onto an object and captures the deformation of these patterns with one or more cameras. By analyzing the distortions of the light patterns on the object's surface, the system calculates the precise geometry and creates a detailed 3D model. This method is fast and accurate, making it useful for things like checking the quality of products, designing new parts, and medical imaging.
4.Time-of-Flight (ToF) Scanning

Time of flight scanning is a 3D imaging technique that measures the time it takes for a light signal to travel from the scanner to an object and return. By emitting a laser or light pulse and calculating the round-trip time of the reflected light, the scanner determines the distance to various points on the object's surface. This information is then used to create a detailed 3D model. Time of flight scanning is particularly effective for capturing large areas quickly and is often used in applications such as mapping, surveying, and autonomous navigation.
How to use 3D Scanning ?
Here is a concise guide on how to use a 3D scanner:
- Prepare the object : Ensure the object is clean, stable, and placed on a contrasting background. Avoid reflective or transparent surfaces that can interfere with the scanning process.
- Set up the scanner : Based on the scanner's range, position the scanner at the appropriate distance from the object. If necessary, adjust settings like resolution and capture mode.
- Scanning the object : Slowly move the scanner around the object, ensuring all surfaces are captured. For larger objects, scan in sections and maintain overlap between scans for easier alignment later.
- Process the data : Use the scanner's software to align and merge the captured scans into a complete 3D model. Edit the model as needed, such as removing unnecessary data or filling holes.
- Export and use the model : Save the final 3D model in the desired format (e.g., STL ) for further use in applications like 3D printing, reverse engineering, or digital preservation.
Benefits of 3D scanning

- Enhanced accuracy and precision : 3D scanners capture intricate details of objects with remarkable precision, enabling engineers and designers to obtain accurate measurements down to the millimeter.
- Time and cost savings : 3D scanning streamlines traditional measurement and inspection processes, reducing the time and labor required to capture complex shapes and geometries.
- Versatility across industries : 3D scanning technology is applicable in a wide range of sectors, including healthcare for creating custom prosthetics, archaeology for digital preservation of artifacts, and entertainment for creating realistic digital models.
- Improved quality control : 3D scanners enable rapid verification of dimensions and tolerances of manufactured parts, detecting any deviations from the original design.
- Streamlined reverse engineering : By capturing the dimensions of an object, 3D scanning simplifies the process of deconstructing a product to understand its components and functionality.
Limitations of 3D scanning

- Line of sight : 3D scanners require a clear line of sight to the object being scanned. They cannot capture hidden or internal geometry that is not visible to the scanner, such as complex internal features or enveloped volumes.
- Surface properties : Optical 3D scanners, while versatile, can face challenges with certain surface properties. Dark, shiny, reflective, or transparent objects can be difficult to scan accurately, as they can interfere with the scanner's ability to detect and measure surfaces. However, these challenges can be overcome with the proper adjustments, showcasing the adaptability of 3D scanning technology. Resolution and accuracy: The resolution and accuracy of 3D scans depend on factors like the scanner's technology, quality of sensors, and calibration. Achieving high levels of detail and precision can be challenging, especially for smaller or intricate objects.
- Ambient conditions : Environmental factors such as lighting, temperature, and humidity can affect the performance of 3D scanners. Outdoor scanning can be particularly challenging due to varying weather conditions.
- Data processing : 3D scanning often requires extensive post-processing to align, merge, and refine the captured data into a usable 3D model. This crucial step, while time-consuming and requiring specialized software and expertise, is necessary to ensure the accuracy and quality of the final 3D model.
What are the Applications of these 3D Scans?
3D scanning has a wide range of applications across various industries. Here are some of the most common applications of 3D scanning technology:
Industrial Design and Manufacturing:

In industrial design and manufacturing, 3D scanning is employed for reverse engineering, quality control, and prototyping. It enables the digitization of physical objects, facilitating the design process by providing accurate measurements and geometric data. Manufacturers use 3D scanning to analyze and improve existing products, create custom-fit components, and streamline production processes, ultimately reducing time-to-market and costs.
Healthcare and Medicine:

The healthcare industry benefits from 3D scanning for various applications, including patient-specific medical modeling, orthotics, and prosthetics. It allows for the creation of precise anatomical models based on patient scans, which aid in surgical planning, education, and training. Dentists utilize 3D scanning for digital impressions, orthodontic treatment planning, and fabrication of dental restorations, improving patient outcomes and treatment efficiency.
Forensic Science:

In forensic science, 3D scanning is used for crime scene documentation, evidence analysis, and facial reconstruction. Crime scene investigators employ 3D scanners to capture detailed 3D models of crime scenes, preserving spatial relationships and physical evidence. Forensic anthropologists utilize 3D scanning to analyze skeletal remains and create facial reconstructions, assisting in the identification of victims and suspects in criminal investigations.
Cultural Heritage Preservation:

3D scanning is instrumental in documenting and preserving cultural heritage sites, artifacts, and artworks. It allows for the creation of high-resolution digital replicas, which can be used for conservation, restoration, and virtual exhibitions. Museums and archaeologists use 3D scanning to capture intricate details of historical objects and sites, ensuring their preservation for future generations.
Popular 3D Scanners Available

- FARO Focus : The FARO Focus is a highly versatile and precise laser scanner widely used in various industries, including architecture, engineering, construction, and forensic analysis. This scanner employs time-of-flight laser technology to capture detailed 3D measurements of large-scale environments and objects with exceptional accuracy. The FARO Focus is known for its portability, ease of use, and robust design, making it suitable for both indoor and outdoor applications.
- ATOS 5 : The ATOS 5 by GOM is a high-precision 3D scanner designed for industrial applications, particularly in quality control and manufacturing. Utilizing advanced blue light technology, it captures detailed and accurate 3D measurements of objects, ranging from small intricate components to large industrial parts. The ATOS 5 excels in speed and efficiency, offering fast data acquisition and high-resolution scanning, making it ideal for applications such as rapid prototyping, reverse engineering, and comprehensive inspection.
- Zeiss Comet : The Zeiss COMET is a high-precision structured light 3D scanner designed for meticulous industrial applications, including quality control, product development, and reverse engineering. Known for its exceptional accuracy and versatility, the COMET uses advanced blue LED technology to capture detailed 3D measurements of objects, from small intricate parts to larger components.
- Creaform HandySCAN 3D : The Creaform HandySCAN 3D is a portable, handheld laser scanner known for its high precision and versatility, making it ideal for a wide range of industrial applications such as manufacturing, aerospace, and automotive industries. Featuring a lightweight and ergonomic design, the HandySCAN 3D offers exceptional ease of use, allowing operators to capture detailed and accurate 3D measurements even in complex and hard-to-reach areas. Its advanced laser triangulation technology and dynamic referencing system ensure reliable and consistent data acquisition, regardless of the environment or object movement .
- Artec Eva : The Artec Eva is a highly regarded handheld 3D scanner known for its versatility, ease of use, and high-quality scanning capabilities. Utilizing structured light technology, the Eva captures precise 3D measurements with high resolution and speed, making it ideal for a wide range of applications including rapid prototyping, reverse engineering, and medical imaging.
Common Software for Photogrammetry 3D Scanning
OpenDroneMap
- Another free one, OpenDroneMap is mainly for making 3D models from drone photos. It's popular with people who make maps and study the Earth.
RealityCapture
- This software is really fast and good at handling lots of photos at once. It's used for making 3D models of things like buildings or movie sets.
Pix4D
- Originally for drones, Pix4D now works for both aerial and ground photos. It's good for maps and farming, making 3D models of fields and buildings.
3DF Zephyr
- 3DF Zephyr is good for beginners and pros. It can automatically make 3D models look real and is used for things like art or science projects.
MicMac
- Free and open-source, MicMac is great for people who want to work on projects with photos taken really close-up or from far away.
For more content and information on Photogrammetry, click here
Conclusion
In conclusion, 3D scanning is a powerful technology that captures the shape and details of objects in three dimensions, helping industries like manufacturing, healthcare, and design create accurate digital models. There are several types of 3D scanners, each using different methods like lasers or cameras to collect data. Laser scanners, for instance, measure distances with precision beams of light, while structured light scanners project patterns onto objects for detailed imaging. Photogrammetry uses photos from different angles to create 3D models. Each scanning method has its strengths, making 3D scanning essential for improving product quality, designing new inventions, and preserving historical artifacts with remarkable detail and accuracy.
While 3D scanning offers remarkable benefits, it also requires significant investment in various types of scanners and software. If you prefer to focus on your core projects rather than the complexities and costs of 3D scanning, our expert team at iamrapid is here to help.Rather than investing in multiple 3D scanners, you can rely on us to provide the right technology for your specific use case. Contact us at iamrapid to access our 3D scanning services and accelerate your innovation journey. If you found this information useful, kindly share it with your peers who are actively involved in innovation. Let's work together to inspire innovation and drive the adoption of this technology.