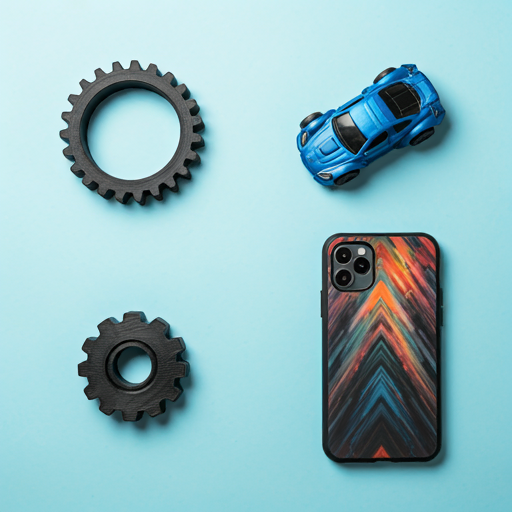
Introduction to How does Layer height Affect 3D Print?
Layer height is a crucial factor in 3D printing that significantly affects print quality, speed, and strength. Smaller layer heights, typically 0.1 mm or less, produce smoother surfaces and finer details, making them ideal for intricate models and parts where surface finish is paramount. The trade-off, however, is that these smaller layers require more time to print, as the printer needs to lay down more layers to build up the same height. This increased print time also translates to higher material usage and potentially more wear on the printer.
Conversely, larger layer heights, such as 0.2 mm or more, can drastically reduce print time and material consumption, making them suitable for rapid prototyping or printing larger objects where high detail is less important. However, this comes at the cost of reduced print quality, with more noticeable layer lines and a rougher surface finish. Additionally, larger layer heights can compromise the structural integrity of the print, leading to weaker parts due to poorer layer adhesion and increased anisotropy, where the strength varies more significantly between different axes.

What is Layer Height ?
Layer height, also known as layer thickness, is a parameter in 3D printing that determines the thickness of each individual layer of material deposited during the printing process. It is typically measured in millimeters (mm) or microns (µm). Layer height plays a critical role in determining the quality, detail, and strength of the final printed object.
In simpler terms, layer height defines how "tall" each slice of the printed object will be. For example, a layer height of 0.1 mm means that each layer added by the printer will be 0.1 mm thick. Smaller layer heights result in more layers being used to build up the object, which can produce smoother surfaces and finer details but also increases print time and material usage. Conversely, larger layer heights reduce the number of layers, leading to faster prints with potentially rougher surfaces and less detail.
Why is layer height important ?
Layer height is important in 3D printing because it directly affects the quality, strength, speed, and material efficiency of the printed object. Here are the key reasons why layer height is significant:
1.Print Quality and Detail
Layer height determines the smoothness and detail of the printed object. Smaller layer heights produce finer details and smoother surfaces, making them ideal for intricate designs and objects where appearance is critical. Larger layer heights can result in visible layer lines and a rougher finish, which may be acceptable for functional prototypes or less detailed parts.
2.Print Speed
Layer height influences the overall print time. Smaller layer heights require more layers to complete the same height, significantly increasing print time. Larger layer heights reduce the number of layers needed, thus decreasing the print time. This makes larger layer heights more suitable for rapid prototyping or large objects.
3.Structural Strength
The strength of the printed object can be affected by layer height. Smaller layer heights generally result in better layer adhesion, enhancing the structural integrity of the print. Larger layer heights can lead to weaker layer bonds, making the object more prone to splitting along the layer lines and reducing its overall strength.
4.Material Usage
Layer height also affects the amount of material used in a print. Smaller layer heights may use more material due to the increased number of layers, while larger layer heights can be more material-efficient, especially for objects where precision is not a primary concern.

Standard Layer Heights of Different 3d Printing Technologies
Fused Deposition Modeling (FDM)
Fused Deposition Modeling (FDM) is a popular 3D printing technology known for its versatility and wide accessibility. Standard layer heights for FDM typically range from 0.1 mm to 0.3 mm, with a broader range from 0.05 mm to 0.4 mm available depending on the desired balance between print quality and speed. Smaller layer heights, such as 0.1 mm or less, provide finer detail and a smoother surface finish, making them suitable for detailed prototypes and aesthetic parts. Conversely, larger layer heights, such as 0.3 mm or more, allow for faster print times and are often used for producing functional prototypes or larger objects where surface finish is less critical.
Stereolithography (SLA)
Stereolithography (SLA) is a 3D printing technology renowned for its high resolution and excellent surface finish. Standard layer heights for SLA typically range from 0.025 mm to 0.1 mm, with a typical range of 0.01 mm to 0.2 mm. This capability to produce very thin layers makes SLA ideal for applications requiring high precision and smooth surfaces, such as in jewelry, dental models, and intricate prototypes.
Digital Light Processing (DLP)
Digital Light Processing (DLP) shares similarities with SLA in producing high-resolution prints with smooth surfaces, using a digital light projector to cure resin layer by layer. Standard layer heights for DLP generally range from 0.025 mm to 0.1 mm, with a broader range of 0.01 mm to 0.2 mm. DLP is capable of achieving fine details and is particularly suited for small, intricate parts such as dental models and fine jewelry. The choice between DLP and SLA often hinges on the specific application requirements and desired speed, as DLP can offer faster curing times due to the projection-based approach.
Selective Laser Sintering (SLS)
Selective Laser Sintering (SLS) is a 3D printing technology that excels in producing durable and functional parts without the need for support structures. Standard layer heights for SLS range from 0.1 mm to 0.15 mm, with a typical range of 0.08 mm to 0.2 mm. This technology uses a laser to sinter powdered material layer by layer, resulting in robust parts suitable for engineering and manufacturing applications.
MultiJet Printing (MJP)
MultiJet Printing (MJP) is known for its ability to produce high-detail parts with smooth surfaces, using multiple jets to deposit and cure photopolymer layers. Standard layer heights for MJP range from 0.016 mm to 0.032 mm, with a typical range of 0.013 mm to 0.05 mm. This fine layer resolution allows MJP to create intricate details and smooth surfaces, making it suitable for prototyping, dental models, and jewellery.
Direct Metal Laser Sintering (DMLS) and Selective Laser Melting (SLM)
Direct Metal Laser Sintering (DMLS) and Selective Laser Melting (SLM) are advanced 3D printing technologies used for producing metal parts with high strength and precision. Standard layer heights for DMLS and SLM range from 0.02 mm to 0.05 mm, with a typical range of 0.02 mm to 0.1 mm. The ability to create complex metal components with high mechanical properties makes DMLS and SLM ideal for critical engineering applications.
Binder Jetting
Binder Jetting is a 3D printing technology that uses a liquid binding agent to fuse powdered material layer by layer. Standard layer heights for Binder Jetting typically range from 0.1 mm to 0.2 mm, with a broader range from 0.07 mm to 0.3 mm. This technology is capable of producing full-color prototypes, metal casting patterns, and sand molds, offering a good balance between detail and print speed. Binder Jetting is particularly useful for applications where the final parts need to be sintered or infiltrated to achieve the desired material properties.
When to Choose a Lower Layer Height ?
Choosing a lower layer height in 3D printing is particularly beneficial when accuracy in hole dimensions and positional stability is critical. Lower layer heights, typically 0.1 mm or less, ensure that holes and other small features are more precisely rendered, reducing the likelihood of dimensional inaccuracies. This is crucial when designing parts that require exact specifications for fitting components or aligning with other parts in assemblies. For example, in mechanical engineering, lower layer heights help maintain the integrity of threaded holes or precise alignment pins that must fit snugly and function correctly.
Furthermore, the orientation of the printed object—whether horizontal or vertical—also influences the choice of layer height. When printing horizontally, lower layer heights help minimize the appearance of layer lines on visible surfaces, enhancing the overall surface finish. This is advantageous for parts where aesthetic appeal is important, such as consumer products or display models. For vertical orientations, lower layer heights contribute to smoother, more consistent layer bonding, reducing the risk of delamination or weak points in the print. This is critical for functional parts where structural integrity and durability are paramount, such as load-bearing components or intricate architectural models.
For example think that you are creating a model which has a hole and we have print it using different layers,so in this process the layer by layer method can cause stair stepping which effects the overall output of the print.

Note: Even when we are placing the model we have to take care in mind whether keeping it vertical or horizontal or any other angle gives the best result.
How does Layer Height Impact Parts with Curves and Angles ?
- Surface Quality : Layer height significantly affects the smoothness of curves and angles in 3D printed parts. Smaller layer heights (e.g., 0.1 mm or less) result in smoother surfaces with reduced visible layer lines, ideal for achieving high aesthetic quality and detail in models and sculptures. Larger layer heights (e.g., 0.2 mm or more) can exhibit more pronounced layering, which may detract from surface finish, suitable for rapid prototyping or functional parts where surface appearance is less critical.
- Dimensional Accuracy : Smaller layer heights enhance the dimensional accuracy of curves and angles by closely adhering to the CAD model's design. This precision is crucial for parts with complex geometries or fine details, ensuring that curves are accurately represented without significant deviations. Larger layer heights may struggle to accurately reproduce sharp angles and smooth curves, potentially impacting the overall dimensional fidelity of the printed part.
- Print Time and Efficiency :Choosing the appropriate layer height involves balancing print time and efficiency. Smaller layer heights increase print time due to the higher number of layers required to build the part, as well as increased material usage. Conversely, larger layer heights decrease print time and material consumption, making them more efficient for rapid prototyping and larger-scale production where fine detail is less critical.
Visual Appearance or Functionality?
If you are considering the visual outlook its better to give lesser layer heights which will give a smooth surface but can increase the time and cost.If you are considering time and money more priority its better for you to go with more layer height as it can give mechanical properties as well.
Conclusion
In the realm of 3D printing, the choice of layer height is a crucial factor that profoundly affects the final outcome of printed objects. Lower layer heights, such as 0.1mm, offer superior surface quality and finer details, making them ideal for projects where aesthetics and precision are paramount. These settings, however, come with the drawback of significantly increased print times and potentially higher material consumption. For intricate designs, jewelry, or highly detailed prototypes, the trade-off is often worth it, as the results can be remarkably smooth and visually appealing.
On the other hand, higher layer heights, such as 0.3mm, provide a faster and more economical printing process. This is particularly advantageous for larger objects, functional parts, or rapid prototyping where surface finish and fine detail are less critical. The reduced print time and material usage make these settings more practical for everyday printing tasks, where efficiency and cost-effectiveness are prioritized. However, the compromise is in the form of less detailed and rougher surfaces, which may not be suitable for all applications.
Ultimately, the decision on layer height should be driven by the specific requirements of the project at hand. By understanding the implications of different layer heights, users can tailor their 3D printing process to achieve the best balance between quality, speed, and material efficiency. Whether the objective is to create a high-resolution model with exquisite details or to produce a functional part quickly and economically, mastering the layer height selection is key to successful 3D printing endeavors.
For any further inquiries regarding how layer height affects your 3D printing, we encourage you to contact us by visiting our website https://iamrapid.com . Please review the content above to get your object 3D printed according to your requirements by choosing the specific layer height. If you want to choose our 3D printing services, please contact us at https://iamrapid.com and provide information about the specific layer height you want to use based on surface finish, strength, and cost considerations of the part. Feel free to share this insightful content with others to enhance understanding of how layer height affects 3D printing.