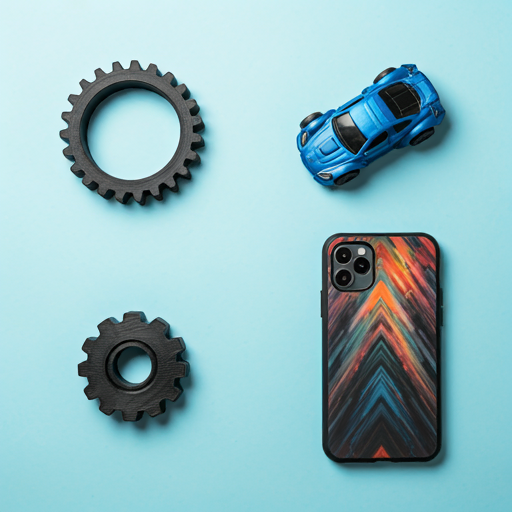
Introduction to Geometrical Constraints in 3D Printing
3D printing, also known as additive manufacturing, has revolutionized how we design and produce objects. However, despite its versatility, 3D printing has certain geometrical constraints that must be understood to fully leverage its capabilities. This article delves into the typical geometrical constraints in 3D printing, the specific challenges of different technologies, and strategies to overcome these limitations.
Overview of 3D Printing
3D printing involves creating three-dimensional objects by layering materials based on digital models. The process is used across various industries, including aerospace, healthcare, automotive, and consumer goods, due to its ability to produce complex geometries that traditional manufacturing methods cannot achieve.
Importance of Understanding Geometrical Constraints
Understanding geometrical constraints is crucial for optimizing the design and production process in 3D printing. These constraints influence the printed object's feasibility, quality, and functionality. Designers and engineers must consider these limitations to ensure successful prints and avoid costly redesigns or failures.
Common Geometrical Constraints in 3D Printing
1.Build Size Limitations
Build size limitations refer to the maximum dimensions an object can have based on the 3D printer's capabilities. This is influenced by the type of printer and the technology it employs.
Desktop vs. Industrial Printers
Desktop 3D printers typically have smaller build volumes compared to industrial printers. For instance, a desktop FDM printer might have a build volume of 200 x 200 x 200 mm, whereas an industrial SLS printer can handle larger volumes up to 750 x 550 x 550 mm.
Each printing technology boasts of various sizes ,they are listed as follows:
Technology | Typical Build Size |
---|---|
FDM | 200 x 200 x 200 mm for desktop printers; Up to 900 x 600 x 900 mm for industrial printers |
SLA | 145 x 145 x 175 mm for desktop printers; Up to 1500 x 750 x 500 mm for industrial printers |
SLS | 300 x 300 x 300 mm (up to 750 x 550 x 550 mm) |
DMLS/SLM | 250 x 150 x 150 mm (up to up to 500 x 280 x 360 mm) |
MJF | 380 x 285 x 380 mm (14.9" x 11.2" x 14.9") |
2.Minimum Wall Thickness
Minimum wall thickness refers to the thinnest walls that can be printed without compromising structural integrity. This varies by technology and material.
In FDM, this parameter depends upon the nozzle tip size; only thickness values higher than the nozzle diameter can be printed, thus constraining us.
Similarly, with advanced printing techniques, the onus is on the designer to ensure the design doesn't clash with any geometric constraints. This underscores the importance of careful design and the active role of the designer in the 3D printing process.
A detailed list of optimum minimum wall thickness for 3D printing technologies is given below:
3D Printing Process | Recommended Minimum Wall Thickness |
---|---|
FDM | 0.8 mm |
SLA/DLP | 0.5 mm |
SLS | 0.7 mm |
MJF | 0.5 mm |
DMLS/SLM | 0.4 mm |
Impact on Design and Structural Integrity
Thin walls can lead to weak structures that may not withstand functional use. Ensuring adequate wall thickness is essential for maintaining the strength and durability of the printed object. For example, Architects and game designers often aim to create 3D models with extremely thin features, such as hair, capes, and sails. Producing these elements can be difficult for even the most advanced 3D printers. Being aware of this particular limitation is crucial when dealing with such fine details.
3.Overhangs and Support Structures
Overhangs are parts of the design that extend outward without direct support beneath them. These require support structures during printing to prevent sagging or failure. Click here to know more about support structures.

Challenges with Overhangs
Overhangs greater than a certain angle (typically 45 degrees) can be problematic. Without adequate support, they can deform due to gravity during the printing process.
Techniques to Mitigate Overhang Issues
- Optimizing part orientation
- Using support structures that can be easily removed post-printingDesigning with self-supporting angles
- Designing with self-supporting angles
4.Manifold and Watertight Models
For a 3D model to be printable, it must be manifold (every edge belongs to exactly two faces) and watertight, i.e., there are no holes in the mesh (unless they’re integral to the design).
Definition and Importance :
A manifold model ensures the geometry is correctly defined and watertight, preventing gaps or missing faces that could lead to printing errors. On the other hand, non-manifold models can be misinterpreted by the slicer software that generates 3D printing instructions. This can result in prints with inconsistent layers, holes, or other errors, rendering the object likely unprintable.
Common Issues and Solutions
- Non-manifold edges : Ensure exactly two faces share all edges.
- Gaps in the mesh : Use analyzer software tools (like Netfabb or Meshmixer) to check and repair the mesh before printing.
5. Practical Tips for 3D Printing Smooth Surfaces: Understanding NURBS
NURBS, or Non-Uniform Rational B-splines, are mathematical representations that generate and represent curves and surfaces. They are instrumental in computer-aided design (CAD) for creating smooth and complex shapes.
Definition and Importance :
NURBS are defined by control points, weights, and knots, allowing for precise control over the shape of curves and surfaces. They are crucial in industries requiring smooth surfaces and intricate designs, such as automotive and aerospace engineering.
Challenges in 3D Printing
Translating NURBS-based designs to 3D printing can be challenging due to the discretization process. The smoothness of NURBS surfaces may be compromised if not correctly converted to the polygonal meshes that most 3D printers use.
Fortunately, most modeling software can export 3D models with sufficient polygons by using the default settings, leading to smooth 3D-printed parts. The export settings can be modified if a higher polygon count is needed.
Practical Tips for Printing Smooth Surfaces
- High-Resolution Meshes : Increase the resolution of the mesh when converting NURBS to STL files to preserve the surface's smoothness.
- Smoothing Algorithms: : Smoothing algorithms in CAD software reduce the appearance of faceting on curved surfaces.
- Post-Processing : To enhance the surface finish of printed parts, employ post-processing techniques such as sanding, polishing, or chemical smoothing.
- Layer Height : To improve the surface quality of curved and smooth surfaces, use a smaller layer height during printing.
- Printer Calibration : Ensure the 3D printer is well-calibrated and maintained to achieve the best possible surface finish.
Specific Constraints for Different 3D Printing Technologies
Fused Deposition Modeling (FDM)
- Layer Thickness and Printing Speed : Layer thickness in FDM can range from 0.1 mm to 0.4 mm. Thicker layers speed up the print but reduce resolution, while thinner layers enhance detail at the cost of increased print time.
- Number of Contours : The number of contours affects the strength and appearance of the print. More contours improve strength but increase print time.
Stereolithography (SLA)
- Resolution and Surface Finish : SLA offers high resolution and smooth surface finishes, making it ideal for detailed prototypes and models. However, due to the brittleness of the printed parts, it requires careful handling.
- Material Considerations : SLA materials are typically resins, which can be more expensive and have limited mechanical properties compared to other printing technologies.
Selective Laser Sintering (SLS)
- Powder Bed Fusion Constraints : SLS uses a powder bed fusion process, which can create complex geometries without support structures. However, it requires effective powder management and post-processing.
- Design for Powder Removal : Designs must allow for the easy removal of un-sintered powder, particularly in intricate internal cavities.
Direct Metal Laser Sintering (DMLS)
- Metal Printing Challenges : DMLS prints metal parts with high precision but faces challenges like thermal stress and warping. Proper support structure design is crucial to counteract these issues.
- Post-Processing Requirements : DMLS parts often require post-processing steps such as heat treatment and surface finishing to achieve desired mechanical properties and surface quality.
Conclusion
Summary of Key Points
Understanding and addressing geometrical constraints is essential for successfully applying 3D Printing. Each technology has its specific limitations, but these can be effectively managed with careful design and optimization.
Importance of Considering Geometrical Constraints in 3D Printing
Considering geometrical constraints from the design phase ensures better print quality, structural integrity, and functional performance, ultimately leading to more successful and innovative applications.
Future Outlook
Looking ahead, as 3D printing technologies continue to evolve, we can anticipate significant advancements in overcoming current constraints. The future of 3D Printing is not just promising, but holds immense potential for even more complex, functional, and high-quality prints, opening up new horizons in the field.
To get your 3D model printed today, visit https://iamrapid.com for exceptional 3D printing services with an instant quotation within seconds after you upload your 3D model on our quotation software. Our advanced quotation software also does the model analysis, including wall thickness analysis, so you can be warned of any discrepancies that might be caused before we begin printing. Our advanced quotation software assures you that your 3D model is print-ready, so you get the best quality output from our side.