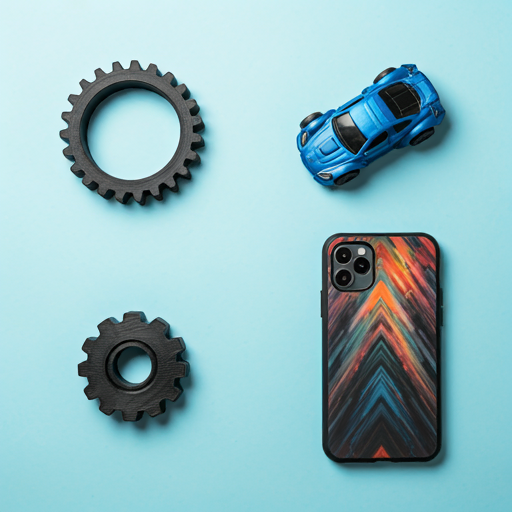



Primary Post Processing Techniques
Manual Processes
Manual post-processing techniques are essential for refining and enhancing the quality of Selective Laser Sintering (SLS) printed parts. These processes address the residual powder and surface roughness often left by the SLS printing process, ensuring that the final product meets the desired standards in terms of appearance, mechanical properties, and functionality. By employing manual methods such as brushing, sanding, and dyeing, operators can achieve a higher degree of precision and customization, catering to specific application requirements and aesthetic preferences.
The importance of manual post-processing extends beyond mere aesthetics. It plays a critical role in improving the structural integrity and durability of SLS parts. For instance, careful manual sanding can smooth out surface irregularities, reducing stress concentrators that could lead to part failure under load. Additionally, manual inspection and assembly allow for a thorough quality check, ensuring that each component meets stringent specifications before it is integrated into a larger assembly.
They are generally manual processes and serve as a prerequisite for most advanced post processing procedures to ensure optimum results.
- Manual sanding
- Brushing
- Solvent Cleaning
Let's compare these methods in detail!
1.Sanding
Sanding is a crucial manual post-processing technique for SLS printed parts, aimed at achieving a smooth and refined surface finish. The process begins with the use of coarser grit sandpaper to remove major surface imperfections and layer lines left by the SLS printing process. By carefully sanding the part, the operator can eliminate rough areas and prepare the surface for finer finishing. As the process progresses, finer grits of sandpaper are used to further smooth the surface, reducing the appearance of any remaining imperfections and creating a uniform texture.
The manual nature of sanding allows for precise control over the areas being refined, making it possible to achieve high-quality finishes even on complex geometries and intricate features. This hands-on approach ensures that delicate areas are treated with care and that the overall aesthetics of the part are significantly improved.
2. Brushing
One of the most basic methods to clean up the surface and and holes/impressions on the surface where unsintered powder is deposited.
Brushing is a fundamental manual post-processing technique used in the initial stages of cleaning SLS printed parts. After the parts are removed from the powder bed, they are often covered with residual powder that needs to be meticulously removed. Using soft brushes, operators can gently clean off this excess powder, especially from hard-to-reach areas and intricate features. The manual brushing process allows for precise and careful handling, ensuring that delicate details of the parts are preserved while effectively removing any loose powder.
This step is critical not only for improving the appearance of the parts but also for preparing them for subsequent post-processing steps like bead blasting or coating. Effective brushing ensures that the surface is free of loose particles that could interfere with further finishing processes.

3. Solvent Cleaning
Solvent cleaning is a pivotal manual post-processing technique for SLS printed parts, particularly effective in removing any remaining powder and surface contaminants that brushing and blasting might miss. This process involves immersing the parts in a solvent bath or applying solvent with a cloth or brush to dissolve and wash away residual particles.
Beyond just cleaning, solvent cleaning can also contribute to the surface finish of the parts by slightly smoothing out minor imperfections. The solvent can help to dissolve tiny burrs and surface roughness, leading to a more uniform and refined appearance. This step is particularly crucial when preparing parts for applications where a high-quality surface finish is essential, such as in medical devices or consumer products. Proper handling and safety precautions, including adequate ventilation and the use of personal protective equipment, are essential to ensure a safe and effective solvent cleaning process.
Commonly used organic solvents include acetone, butanone, tetrahydrofuran can be used to clean up surfaces, but they have a limitation that it can only be used on selective materials.This meticulous cleaning step ensures that the surface is thoroughly prepared for further finishing processes such as painting or coating.