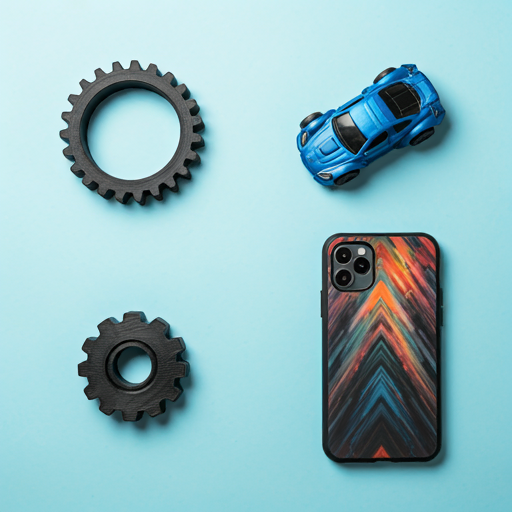
What is Additive Manufacturing?
Additive manufacturing (AM), commonly known as 3D printing, is a transformative approach to industrial production that enables the creation of lighter, stronger parts and systems. It involves building objects layer by layer from a digital file, contrasting with traditional manufacturing methods that often require cutting away material from a larger block. This layer-by-layer process allows for intricate and complex geometries that would be difficult or impossible to achieve with conventional techniques. AM is used across various industries, including aerospace, automotive, healthcare, and consumer goods, providing significant advantages in terms of design flexibility, material efficiency, and speed of production.
The key benefits of additive manufacturing include the ability to produce custom, on-demand parts without the need for expensive tooling or molds. This makes it particularly valuable for prototyping, where designers can quickly iterate and test different versions of a part before finalizing the design. Additionally, AM supports the production of highly complex structures that are both lightweight and strong, which is essential in applications such as aerospace, where reducing weight can lead to significant fuel savings. Furthermore, the technology's ability to use only the necessary material for each part results in less waste and can be more sustainable than traditional subtractive manufacturing processes.
AM applications are limitless.Before we use this to print models for visual appearance after that we started using it in fields like engineering industries,dental areas,hearing aids etc
How does additive manufacturing work?
Additive manufacturing, commonly known as 3D printing, is a process that creates objects layer by layer from a digital model. It begins with designing a 3D model using computer-aided design (CAD) software, which is then optimized for 3D printing. The digital model is converted into a compatible format like STL, and processed by slicing software to divide it into thin horizontal layers and generate G-code instructions. These instructions guide the 3D printer on how to construct each layer, considering the specific printing technology in use, such as FDM, SLA, SLS, or DMLS, which differ in their methods of material deposition or curing.
The printing phase involves the 3D printer following the G-code to build the object incrementally. Depending on the technology, this might involve extruding thermoplastic filament, curing liquid resin with a UV laser or light projector, or sintering powdered material with a laser. After the object is printed, it undergoes post-processing to achieve the desired properties and finish, which can include removing support structures, surface finishing, and thermal treatments. The final step is quality control, ensuring the printed part meets all required specifications through inspection and testing before deployment or use. This process allows for the creation of complex, custom, and high-quality parts with significant advantages over traditional manufacturing methods in terms of flexibility, efficiency, and material usage.

Additive Manufacturing Workflow

The additive manufacturing steps depend on many factors including the technology,industry,equipment,and application.Here are the five key sections of an additive manufacturing process:

Design Step
The initial stage of the design section involves conceptualizing the object. This is where the idea for the product is developed, taking into account its intended function, aesthetics, and any specific requirements.Once the concept is solidified, it is translated into a precise digital 3D model using computer-aided design (CAD) software such as SolidWorks, AutoCAD, or Blender. The CAD model serves as a detailed representation of the final product, incorporating all necessary dimensions, geometries, and design features.
Design for Additive Manufacturing (DfAM) is a critical aspect of the design section. DfAM involves optimizing the CAD model to take full advantage of the capabilities and limitations of additive manufacturing technologies. This includes designing complex geometries that are difficult or impossible to achieve with traditional manufacturing methods, minimizing the need for support structures, and optimizing the part's internal structures for weight reduction and material efficiency.
Before finalizing the design, simulation and analysis tools like Ansys, Comsol are used to predict how the part will behave under various conditions. This can include stress analysis, thermal analysis, and fluid dynamics simulations. These tools help identify potential issues such as weak points, thermal deformations, or areas prone to failure.
The business value of 3d printing is that to save money and time to produce parts which we need in a single piece manner
The last step in the design section is preparing the file for printing. The CAD model is exported into a format that is compatible with 3D printers, typically STL (Stereolithography) files. These files are then ready to be processed by slicing software in the next stage of the workflow.
Pre Processing Step

The pre-processing step in additive manufacturing is crucial for preparing the digital model for successful 3D printing. This phase begins with slicing the 3D model, where specialized software converts the digital design into thin horizontal layers. This software generates G-code, which contains precise instructions for the 3D printer regarding the path of the print head, the extrusion of material, and other essential printing parameters. Slicing also involves determining layer height, infill patterns, and density, which influence the final product's strength, weight, and print time.
In addition to slicing, the pre-processing step includes adding support structures. These temporary elements provide stability for overhanging features and complex geometries during the printing process, preventing issues like sagging or warping. Support structures are automatically generated by the slicing software but can often be manually adjusted to optimize material use and ease of removal. Finally, print simulation is conducted to visualize the printing process layer by layer, allowing for the identification and correction of potential issues before printing begins.
After pre processing there is the physical setup of the machine,these are
- Aligning and loading the build plate or substrate,
- Preparation of the printing chamber atmosphere (molten metal must be protected from oxygen), and
- Preparing and loading the feedstock for the printer. The complexity depends on the type of the feedstock.Example, metal powders require carefully handling due to their toxicity,flammability,and propensity to oxidize.
3D Printing Step

The 3D printing step in the additive manufacturing workflow is where the digital design is transformed into a physical object. This process starts with the 3D printer interpreting the G-code generated during the pre-processing step. The G-code provides detailed instructions on how to build the object layer by layer. Depending on the type of 3D printing technology used, such as Fused Deposition Modeling (FDM), Stereolithography (SLA), Selective Laser Sintering (SLS), or Direct Metal Laser Sintering (DMLS), the printer deposits material in precise locations to form each layer. For instance, FDM printers extrude heated thermoplastic filament, while SLA printers use a UV laser to cure liquid resin.
During the printing process, the printer's build platform moves incrementally after each layer is completed, allowing the next layer to be added on top in series. This layer-by-layer construction continues until the entire object is formed. The environment within the printer, including temperature and humidity, is often controlled to ensure optimal material properties and minimize defects. Each layer must adhere properly to the one below it, which is why parameters such as print speed, temperature, and cooling rates are critical and must be meticulously managed.
Throughout the 3D printing step, the printer may pause or slow down to add features like internal structures or support material, which are crucial for complex geometries. The accuracy and resolution of the printer play a significant role in determining the final quality of the printed object. Once the printing is complete, the object is allowed to cool and solidify, making it ready for the post-processing stage.
Post Processing Step

The post-processing step in additive manufacturing is crucial for refining the printed object and ensuring it meets the desired specifications and quality standards. This phase begins with the removal of support structures that were added during the printing process to stabilize overhanging features and complex geometries. Depending on the material and printing technology used, support removal can involve manual breaking, cutting, or dissolving in a suitable solvent. This step must be done carefully to avoid damaging the final part.
Following support removal, surface finishing techniques are applied to enhance the appearance and functionality of the printed object. Common surface finishing methods include sanding, polishing, and painting, which improve the surface smoothness and aesthetic appeal. For parts printed with metal or high-performance polymers, additional treatments such as heat treatment, annealing, or sintering may be required to enhance mechanical properties and relieve internal stresses. In the case of resin-based prints, post-curing with UV light can further harden the material and improve its durability.
Finally, the post-processing step includes quality control measures to ensure the printed part meets all design specifications and functional requirements. This involves thorough inspection using tools like calipers, micrometers, and coordinate measuring machines (CMM) to check dimensional accuracy. Functional testing may also be conducted to assess the part's performance under real-world conditions.
Detailed Steps in the Post-Processing Phase of Additive Manufacturing
Build Removal
The build removal step involves detaching the printed object from the build platform, which is a critical initial stage in post-processing. This step requires careful handling to avoid damaging the object and may involve specialized tools or automated systems. For certain technologies, such as resin or powder-based printing, the build platform also needs to be cleaned and prepared for future prints. Ensuring a clean and precise removal sets the stage for successful subsequent post-processing steps.
Part Separation
Part separation is necessary when multiple parts are printed together or when the object is integrated with support structures. This process involves detaching the printed parts from the supports or rafts used during the printing process. Depending on the complexity and size of the parts, this can be done manually or with automated tools. Proper part separation ensures that the individual components are ready for further refinement and finishing.
De-binding and Sintering (specific to Binder Jetting processes)
De-binding involves soaking the printed part in a solvent to remove the binding materials used during the printing process, resulting in a highly porous structure. This is followed by sintering, where the part is heated to a temperature below its melting point to fuse the particles together, reducing porosity and increasing strength and density. This two-step process is crucial for transforming the fragile printed part into a robust, solid object.
Machining
Machining is employed to remove any remaining supports and to add critical features that could not be achieved through the printing process. This step ensures that the part meets precise tolerances and specifications. Creating fixtures to hold the parts during secondary operations can be resource-intensive, especially for complex geometries. Machining enhances the accuracy and functionality of the final part, making it suitable for its intended application.
Surface Finishing
Surface finishing techniques are used to improve the surface quality and appearance of the printed part. This can include polishing to achieve smooth surfaces, and tumbling or shot peening to smooth or work-harden the surfaces, enhancing both aesthetics and mechanical properties. These processes are essential for parts that require high-quality finishes or improved surface durability.
Heat Treatment (Specific to Metal Additive Manufacturing)
Heat treatment processes are essential for relieving residual stresses, decreasing porosity, and achieving the desired material properties. This can include post-build removal treatments to relieve stresses, hot isostatic pressing to reduce porosity, pre-machining treatments to temper the material, and post-machining treatments to achieve final hardness and desired metallurgical phases. These treatments ensure the printed metal parts have the necessary strength, durability, and performance characteristics.
Quality Assurance

Quality assurance involves comprehensive testing, analysis, and documentation to ensure that the printed parts meet all required specifications and standards. This includes dimensional inspection, functional testing, surface quality checks, and material properties testing. Quality assurance is critical for verifying that each part is consistent, reliable, and suitable for its intended use, whether for aesthetic applications or demanding industrial environments.
Advantages of Additive Manufacturing
Design Flexibility
Allows for the creation of complex geometries and intricate details that traditional methods cannot achieve. Enables more innovative and optimized product designs.
Customization
Enables production of highly customized products tailored to specific requirements. Achieves customization without significant cost or time increases.
Reduced Waste
Uses only the material necessary to build the object, significantly reducing waste. Lowers material costs and benefits the environment.
Rapid Prototyping
Greatly accelerates the prototyping process, allowing for quick production and testing of prototypes. Speeds up development and reduces time to market.
Lightweight Structures
Produces parts that are both strong and lightweight, beneficial in industries like aerospace and automotive. Improves fuel efficiency and performance.
On-Demand Production
Supports on-demand production, reducing the need for large inventories. Minimizes storage costs and allows for more responsive supply chains.
Cost-Effective for Small Batches
Eliminates the need for expensive tooling and molds, making small production runs more economical. Suitable for limited quantities and customized items.
Complex Assemblies
Integrates multiple parts into a single assembly, reducing the need for joining processes. Leads to stronger, more efficient parts.
Applications of Additive Manufacturing in Various Industries
Aerospace

In the aerospace industry, additive manufacturing is used to produce lightweight and complex components that reduce aircraft weight and improve fuel efficiency. This technology enables the creation of intricate geometries that are difficult or impossible to achieve with traditional manufacturing methods. Parts such as turbine blades, engine components, and air ducts are commonly 3D printed, offering enhanced performance and cost savings through material efficiency and reduced assembly times.
Automotive

Additive manufacturing in the automotive sector is utilized for rapid prototyping, enabling faster design iterations and testing of new components. It also allows for the production of custom parts and tools, which can be tailored to specific vehicle models. Additionally, 3D printing is used for manufacturing lightweight components that contribute to better fuel efficiency and performance, as well as for producing replacement parts on-demand, reducing inventory costs.
Medical and Dental

The medical and dental industries benefit from additive manufacturing through the creation of patient-specific implants, prosthetics, and dental devices. This technology allows for the production of customized anatomical models for surgical planning and training, as well as the direct printing of implants tailored to an individual’s anatomy, improving patient outcomes.
Architecture and Construction

In architecture and construction, additive manufacturing is used to create detailed scale models and prototypes, aiding in visualization and planning. It also enables the production of complex architectural components and structures, such as customized facades and structural elements. Large-scale 3D printing technology is being explored for constructing buildings and infrastructure, offering potential benefits in terms of cost reduction, sustainability, and design flexibility.
Education and Research

Additive manufacturing plays a significant role in education and research, providing hands-on learning opportunities and enabling the exploration of new materials and manufacturing techniques. Educational institutions use 3D printers to teach design and engineering principles, while researchers utilize this technology to develop innovative solutions in fields such as material science, biotechnology, and robotics.
Conclusion
The additive manufacturing workflow involves several crucial steps to transform a digital model into a high-quality physical object. It starts with designing a detailed 3D model using CAD software, optimized for 3D printing. The model is then sliced into layers and prepared with necessary support structures. The 3D printer follows these instructions to build the object layer by layer, using different technologies like FDM, SLA, or SLS, each suited to specific materials and requirements.
Post-processing is essential to refine the printed part, including removing supports, polishing surfaces, and performing heat treatments to improve material properties. Quality assurance ensures that the final product meets all specifications and standards.

By following this comprehensive workflow, additive manufacturing enables the production of complex, customized, and high-performance parts with efficiency and precision. This technology continues to revolutionize various industries, offering unprecedented flexibility and innovation in manufacturing processes.
After reading this you will be able understand the workflow of 3D printing,How we can manage time and money according to our needs.
While additive manufacturing offers significant advantages, it also requires substantial investment in various printers and software. If you prefer to concentrate on your core projects instead of navigating the complexities and expenses of additive manufacturing, our expert team at iamrapid is ready to assist you. Instead of investing in multiple 3D printers, you can depend on us to provide the right technology for your specific needs. Reach out to iamrapid to utilize our additive manufacturing services and speed up your innovation journey. If you found this information helpful, please share it with your peers who are engaged in innovation. Together, we can inspire innovation and promote the adoption of this technology.