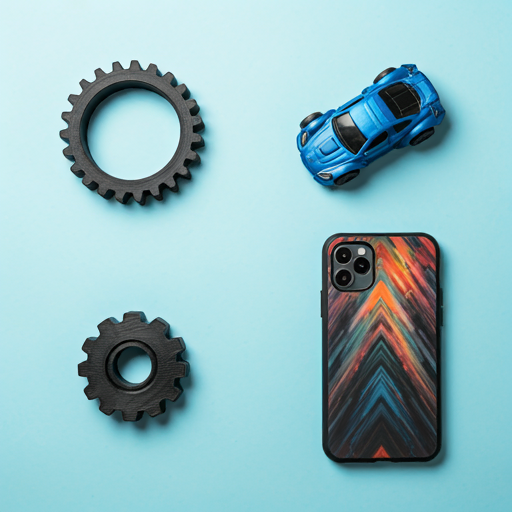
Introduction
When we think about designing products , one of the most important and challenging processes is deciding the dimensional tolerances that would be allowed to design. Speaking of this, itself is a complicated topic, therefore we have domains such as Geometrical Dimensioning And Tolerance(GD&T).
In additive manufacturing too, we have to look into this aspect, since most cases the dimensions of our design and part necessarily doesn't have to match exactly. This happens due to various parameters and strictly speaking in terms of Additive manufacturing it indeed depends on the kind of 3D printing technology that we use to print the parts.
Hence, it becomes very important for us to choose the right technology for printing our products for optimal and dimensionally perfect parts. It plays an important role when precision products are needed , for example in the aviation and space industries, the parts can have very little room for errors, therefore as designers and engineers it becomes our duty to provide dimensionally accurate products.
Variations in the dimensions between design and printed part depends on three main factors:
- 3D Printing Technology : Technique by which material is added
- Warping : Shrinkage of material when it cools
- Support : due to the use of supports which alters the surface finish and eventually the dimensional accuracy of the part.
What will you Learn ?
Understanding the accuracy and tolerances of various 3D printing technologies is crucial for selecting the right method for specific applications. Different 3D printing technologies, such as Fused Deposition Modeling (FDM), Stereolithography (SLA), and Selective Laser Sintering (SLS), each offer distinct levels of precision and accuracy. For instance, SLA printers are known for their high accuracy and fine details due to their use of photopolymer resins and a focused laser, making them ideal for applications requiring intricate designs and smooth finishes. In contrast, FDM printers, while more accessible and cost-effective, generally have lower precision and are better suited for prototyping and larger, less detailed objects.
Several factors influence the accuracy and tolerances of 3D printed parts, including printer calibration, material properties, and layer height. Proper machine maintenance and optimization of print settings can significantly enhance the precision of the final product. Understanding these variables allows users to make informed decisions and achieve the desired balance between cost, speed, and quality in their 3D printing projects.
You will therefore be able to select the most optimum 3D printing technology after gathering knowledge from the blog.
Lets get started!!
Fusion Deposition Modelling (FDM)

Fused Deposition Modeling (FDM) is one of the most widely used 3D printing technologies due to its affordability, simplicity, and versatility. In FDM, a thermoplastic filament is heated and extruded through a nozzle, which deposits the material layer by layer to create a 3D object.
Fused Deposition Modeling (FDM) is one of the most widely used 3D printing technologies due to its affordability, simplicity, and versatility. In FDM, a thermoplastic filament is heated and extruded through a nozzle, which deposits the material layer by layer to create a 3D object.
Despite its widespread use, FDM technology has limitations in terms of accuracy and surface finish compared to other 3D printing methods. The layer-by-layer deposition can result in visible layer lines and less precise details, making it less suitable for applications requiring high precision and smooth surfaces.
Factors such as nozzle diameter, layer height, print speed, and material type significantly impact the accuracy and tolerance of FDM-printed parts. The most common 3D printing technology that we have available is FDM , but due to the manner in which the molten material solidifies and due to the general functioning of the machine it becomes one of the least dimensionally accurate technique for 3D printing.
That being said, it doesn't mean that FDM produces poor parts, but when compared to other advanced techniques it stands lower in terms of dimensional accuracy of printed parts.
Tolreance
- Desktop Printing : ± 0.5mm
- Industrial Printing: ±0.15mm
Warping
Warping in Fused Deposition Modeling (FDM) 3D printing is caused by uneven cooling and contraction of the thermoplastic material, leading to deformation as the edges of the print lift from the build plate. This issue is influenced by factors such as the material's thermal properties (e.g., ABS being more prone to warping than PLA), bed adhesion quality, and temperature control. To mitigate warping, users can optimize bed temperature, enhance bed adhesion using adhesives or build surfaces, adjust print settings to improve stability, and use enclosures to maintain a consistent temperature environment.
Effect Of Supports
Supports in FDM 3D printing prevent overhangs and complex geometries from collapsing during the printing process. They ensure structural integrity and improve overall print quality but can increase material usage and require additional post-processing to remove, potentially affecting surface finish. Proper support placement and settings balance these trade-offs for optimal results.
Stereolithography (SLA)

Stereolithography (SLA) is a sophisticated 3D printing technology that uses a UV laser to cure and solidify liquid photopolymer resin, layer by layer, to create high-precision parts. The process begins with a build platform submerged in a vat of liquid resin. The UV laser traces a pattern on the resin surface, hardening it precisely where it strikes. Once a layer is cured, the platform lowers slightly, and the process repeats, building the object from the bottom up. This method is renowned for its ability to produce parts with exceptional detail and smooth surface finishes, making it ideal for applications requiring intricate designs, such as dental models, jewelry, and highly detailed prototypes.
The advantages of SLA technology lie in its accuracy and ability to produce fine details. SLA printers can achieve layer heights as small as 25 microns, allowing for highly detailed and complex geometries that are difficult to achieve with other 3D printing methods like FDM. However, SLA printing also has some drawbacks. The photopolymer resins used can be more expensive and less durable than thermoplastics, limiting their use in functional parts that require high mechanical strength.
SLA offers better dimensional accuracy compared to FDM but, lacks in terms of materials available to be printed using this method. Giving lesser structural integrity.
Tolreance
- Desktop Printing : ± 0.5mm
- Industrial Printing: ±0.15mm
Warping
Warping in Stereolithography (SLA) 3D printing occurs when parts deform due to uneven curing and internal stresses in the photopolymer resin. This issue is influenced by factors such as material shrinkage during the curing process, part orientation, and the adequacy of support structures. Although SLA generally experiences less warping than Fused Deposition Modeling (FDM) because the liquid resin provides inherent support, large or flat parts are still susceptible to warping if these factors are not properly managed.
Effect Of Supports
Supports in 3D printing are essential for maintaining the structural integrity of complex geometries, overhangs, and bridges during the printing process, ensuring dimensional accuracy and preventing collapse. While they help achieve high-quality prints, supports also increase material usage and printing time, and require post-processing to remove, which can be labor-intensive and may affect surface finish.
Selective Laser Sintering

SLS uses laser to sinter powdered material layer by layer into the desired part ,due to this technique of sintering using laser , the printing procedure is very accurate and very narrow tolerances can be met. Selective Laser Sintering (SLS) technology is highly regarded for its ability to produce parts with excellent accuracy and precision, making it suitable for demanding applications that require intricate details and tight tolerances. SLS printers typically achieve a layer thickness of around 100 microns, which allows for the creation of fine details and complex geometries. The laser sintering process ensures that each layer is fused with high precision, resulting in parts that closely match their digital designs.
Despite the high accuracy of SLS, several factors can influence the precision of the printed parts. The quality of the powdered material, the calibration of the laser, and the consistency of the layer spreading process all play crucial roles in determining the final accuracy. Additionally, SLS parts may experience slight dimensional variations due to thermal effects during the sintering process. The surface finish of the SLS printed part is very grainy or powdery in nature, because of which we need to perform post processing on the printed part. This enables us to obtain superior finish and quality.
Tolreance
- Desktop Printing : ± 0.3mm
Warping
Warping in Selective Laser Sintering (SLS) occurs when parts deform due to uneven cooling and internal stresses generated during the sintering process. As the high-powered laser fuses the powdered material layer by layer, temperature gradients can develop, leading to differential cooling rates and resulting in warping or distortion. Factors such as the design of the part, build orientation, and the thermal properties of the material can exacerbate this issue. To minimize warping, it is essential to optimize the build parameters, use proper part orientation, and employ strategies like thermal control and post-processing treatments to ensure even cooling and reduce internal stresses.
Effect Of Supports
NO supports are needed absolutely since the unsintered powder around the part will act as a support throughout the process.
Material Jetting

The most accurate technology for 3D printing is material jetting, this technology enables us to have the best dimensional accuracy in 3D printed parts. Material Jetting (MJ) is a 3D printing technology renowned for its high accuracy and precision, making it ideal for producing detailed and complex parts with smooth surfaces. In Material Jetting, print heads deposit droplets of photopolymer resin onto the build platform, layer by layer. These droplets are then cured using UV light. The process allows for exceptionally fine control over the deposition of material, resulting in high-resolution prints with layer heights as low as 16 microns and tolerances typically within ±0.1 mm.
The accuracy of Material Jetting is influenced by several factors, including the resolution of the print heads, the consistency of the droplet size, and the properties of the photopolymer resins used. The ability to jet multiple materials simultaneously also allows for the creation of parts with varying material properties and colors within a single build, enhancing the versatility and functional capabilities of the printed objects.
The supports that are used for material jetting are solid structures which can be removed completely from the main part once the printing is finished, it introduces minimum surface defects due to the supports used.
Tolreance
- Desktop Printing : ± 0.1mm
Warping
Warping in Material Jetting 3D printing can occur due to uneven cooling and curing of the deposited photopolymer droplets. This phenomenon is influenced by factors such as the material properties of the photopolymer resin, the print environment temperature fluctuations, and the complexity of the printed geometry. While Material Jetting typically produces high-resolution prints with minimal warping compared to other technologies like FDM, large or thin-walled structures are more susceptible.
Effect Of Supports
The solid support structures used for material jetting are completely removable after the printing and cause minimum damage to surface geometry. While supports facilitate the successful printing of intricate designs, they can increase material usage and require post-processing to remove, potentially affecting the surface finish of the printed object. Careful design and placement of supports are essential to achieve high-quality prints with minimal post-processing effort in Material Jetting technology.
Metal 3D Printing

Metal 3D printing, encompassing technologies such as Direct Metal Laser Sintering (DMLS) and Selective Laser Melting (SLM), is known for its exceptional accuracy and precision, making it highly suitable for producing complex and high-performance parts. These technologies use a high-powered laser to fuse metal powder layer by layer, achieving fine detail and tight tolerances. Typical layer thicknesses range from 20 to 60 microns, with tolerances often within ±0.1 mm. The precision of these processes allows for the creation of intricate geometries and internal features that would be challenging or impossible to achieve with traditional manufacturing methods.
The accuracy of metal 3D printing is influenced by several factors, including the quality of the metal powder, the calibration of the laser system, and the control of the build environment. Consistent powder size and distribution are crucial for achieving uniform layer deposition and high-quality sintering. The build chamber's temperature and atmosphere are also carefully controlled to prevent oxidation and ensure consistent material properties throughout the part.
Overall cost of the process is considerably higher when compared to other technologies, hence choosing this technology to print will require a lot of background checks and understanding of the working in order to obtain optimum results.
Tolreance
- Desktop Printing : ± 0.1mm
Warping
Warping in metal 3D printing, such as Direct Metal Laser Sintering (DMLS) or Selective Laser Melting (SLM), can occur due to residual stresses and thermal gradients during the printing process. As the high-powered laser selectively fuses metal powder layer by layer, rapid heating and cooling cycles can cause differential shrinkage and warping in the part. Factors such as part orientation, build chamber temperature control, and powder bed quality play crucial roles in minimizing warping.
Effect Of Supports
Support structures are important in metal printing to hold the part at the right orientation while the process takes place , as this technology depends a lot on the orientation of the part to be able to efficiently print.
Conclusion
In conclusion, the accuracy and precision of 3D printing technologies play pivotal roles in determining their suitability for various applications. Technologies such as Stereolithography (SLA), Selective Laser Sintering (SLS), and Material Jetting are celebrated for their ability to produce detailed and intricate parts with minimal deviations from the digital design. SLA, known for its high-resolution prints and smooth surface finishes, excels in applications requiring fine details, such as jewelry prototyping and dental models. SLS, on the other hand, offers robust mechanical properties and can fabricate complex geometries without the need for supports, making it ideal for functional prototypes and end-use parts in industries like aerospace and automotive.
However, each technology has its limitations and considerations. Factors like material properties, part orientation, and post-processing requirements significantly impact the final accuracy and surface finish of prints. Moreover, while metal 3D printing methods like Direct Metal Laser Sintering (DMLS) provide exceptional precision for industrial applications demanding high mechanical strength, they may require additional steps such as stress relief annealing to minimize warping and ensure dimensional stability. Overall, understanding these nuances enables users to leverage 3D printing technologies effectively, balancing the trade-offs between accuracy, precision, material choice, and application requirements to achieve optimal results.
At A Glance!
- Material Jetting : High dimensional accuracy and surface finish when cost is no barrier.
Good accuracy and surface finish
- SLA : Parts smaller than 1000cm3.
- SLS : Parts larger than 1000cm3.
- FDM : Quick , economic , Rapid prototyping and small models
For any further questions about how accuracy and precision impact 3D printing, we invite you to visit our iamrapid. Understanding the critical roles of accuracy and precision in technologies such as Stereolithography (SLA), Selective Laser Sintering (SLS), and Material Jetting is essential for achieving high-quality prints tailored to your specific requirements. Whether your priority is achieving intricate details, ensuring mechanical strength, or optimizing costs, selecting the appropriate 3D printing technology ensures reliable performance and quality for your projects according to your priority.
If you're interested in exploring our 3D printing services, please reach out to us at iamrapid. Share your preferences regarding accuracy and precision, and we'll assist you in finding the best solutions for your needs. Feel free to share this informative content with others to deepen their understanding of how accuracy and precision contribute to successful applications of 3D printing.