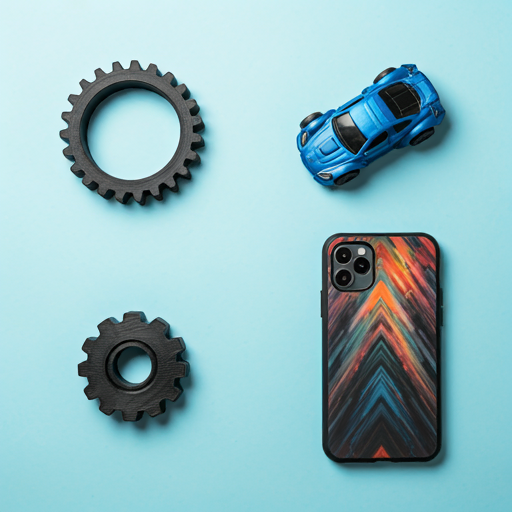
Introduction to SLS 3D Printing
Selective Laser Sintering (SLS) is an advanced 3D printing technology that uses a high-powered laser to fuse small particles of powdered material, typically nylon, into a solid structure. The process begins by spreading a thin layer of powder onto the build platform. The laser then selectively sinters the powder according to the digital design, fusing the particles together. Once a layer is complete, the platform lowers, and a new layer of powder is spread on top, with the laser fusing the new layer to the previous one. This layer-by-layer approach continues until the entire part is built.

SLS is renowned for producing durable and complex parts with excellent mechanical properties and high accuracy, without the need for support structures. This makes it ideal for creating functional prototypes, end-use parts, and complex geometries that would be difficult or impossible to achieve with traditional manufacturing methods. The versatility and robustness of SLS 3D printing have made it a popular choice across various industries, including aerospace, automotive, and consumer products.
How does SLS 3D Printing Works ?
1. Preparation
The SLS 3D printing process begins with preparing the powdered material and the printer. The chosen material, typically a thermoplastic polymer like nylon, is loaded into the material chamber of the printer. The powder bed is then preheated to a temperature just below the melting point of the material. Preheating the powder reduces the energy required from the laser to fuse the particles, ensuring a more efficient sintering process and helping to maintain the integrity of the build.
2. Layering
After preheating, a thin layer of the powdered material is spread evenly across the build platform using a roller or a blade. The printer's laser then selectively sinters the powder according to the cross-sectional design of the object, as directed by a computer. The laser precisely fuses the powder particles together to form a solid layer. This step is critical as it sets the foundation for the subsequent layers, ensuring each layer is accurately fused to the previous one.
3. Building Up Layers
Once a layer is sintered, the build platform lowers by a set layer thickness, typically between 0.05 to 0.15 mm. A new layer of powder is then spread over the previously sintered layer. The laser again selectively sinters this new layer, fusing it to the one below. This process of spreading a new layer of powder and laser sintering continues, building the object layer by layer. This repetitive layering process allows for the creation of complex geometries and detailed features within the printed object.
4. Post-Processing
After the printing process is complete, the build chamber and the printed part need to cool down slowly to avoid thermal stresses and potential warping. Once cooled, the printed part is excavated from the surrounding unfused powder, which is brushed off or blasted away using compressed air. This cleaning step is essential to reveal the final part. Additional post-processing may include surface finishing, such as sanding, polishing, dyeing, or coating, to enhance the part's appearance and properties. The unused powder can often be recycled, making the process more cost-effective and environmentally friendly.
Our SLS 3D Printing capabilities
Requirements | Description |
---|---|
Maximum build size | 381 * 330 * 460 mm |
Lead Time | 5-7 days |
Dimensional accuracy | ± 0.3 mm |
Layer thickness | 100 ÎĽm |
Materials available for SLS 3D printing
Selective Laser Sintering (SLS) 3D printing offers a versatile range of materials, each suited for different applications based on their mechanical properties, durability, and functionality. Here are some of the commonly used materials:
1. Nylon (Polyamide)
Nylon, specifically Nylon 12, is the most commonly used material in SLS 3D printing. It is known for its excellent mechanical properties, including high tensile strength, flexibility, and resistance to impact and abrasion. Nylon is also resistant to chemicals and has a low coefficient of friction, making it ideal for functional prototypes, end-use parts, and components in the automotive, aerospace, and consumer goods industries.
2. Glass-Filled Nylon
Glass-filled nylon is a composite material that combines nylon with glass fibers to enhance its strength, stiffness, and thermal stability. This material is particularly suitable for applications that require higher rigidity and dimensional stability, such as structural components, housings, and parts subjected to mechanical stress. The addition of glass fibers makes it less flexible but significantly stronger than standard nylon.
3. TPU (Thermoplastic Polyurethane)
TPU is a flexible, rubber-like material that combines the durability and strength of plastics with the elasticity of rubber. It is ideal for creating parts that require flexibility, such as gaskets, seals, and protective covers. TPU is also resistant to abrasion, chemicals, and wear, making it suitable for a wide range of industrial and consumer applications.
PA 11 (Polyamide 11)
PA 11 is a bio-based nylon derived from castor oil. It offers similar mechanical properties to Nylon 12 but with improved ductility and impact resistance. PA 11 is environmentally friendly and is used in applications that require durability and flexibility, such as medical devices, sports equipment, and automotive parts. Its bio-based origin also makes it an attractive choice for sustainable manufacturing.
5. PA 12 (Polyamide 12)
PA 12 is a widely used nylon variant in SLS 3D printing, known for its balanced properties of strength, flexibility, and durability. It has good chemical resistance and low moisture absorption, making it suitable for various applications, including functional prototypes, complex assemblies, and consumer products. PA 12’s versatility and reliability make it a popular choice in many industries.
Materials | Properties |
---|---|
Nylon White(PA12) | PA12 known for its toughness, tensile strength, impact strength and ability to flex without fracture |
Design guidelines for SLS 3D printing
1. Wall Thickness
Maintaining appropriate wall thickness is crucial in SLS 3D printing to ensure part durability and strength. The minimum wall thickness should be between 0.7 and 1.2 mm for standard nylon parts to avoid fragility. For parts that need to withstand significant stress or load, walls should be designed with a thickness of at least 1.5 to 2.0 mm. Ensuring adequate wall thickness helps in achieving the desired structural integrity and longevity of the printed parts.
2. Feature Size and Details
Designing features with proper dimensions is essential for ensuring that fine details are accurately printed and distinguishable. Features such as text or logos should have a minimum width of 1.0 mm and a depth of 0.3 mm to be clearly visible. For embossed or engraved details, a minimum depth of 0.3 mm is recommended.
3. Holes and Channels
Holes and channels should be designed with minimum diameters to ensure they are properly formed during printing. Circular holes should have a minimum diameter of 1.0 mm to avoid being closed off by residual powder. For hollow parts, incorporating escape holes with a minimum diameter of 2.0 mm is necessary to allow excess powder to be removed.
4. Clearances and Tolerances
Ensuring adequate clearances and tolerances is vital for parts that need to fit together or have moving components. A minimum clearance of 0.5 mm should be maintained between moving parts or mating surfaces to ensure proper assembly and functionality. SLS typically has a dimensional tolerance of ± 0.3% (minimum ± 0.3 mm), which should be accounted for in the design.
5. Supports and Overhangs
One of the advantages of SLS 3D printing is that it does not require support structures, allowing for the creation of complex geometries. However, overhangs should be designed with self-supporting angles, ideally at 45 degrees or more, to maintain structural integrity during printing.
6. Part Orientation
The orientation of parts during the SLS printing process can significantly impact the final quality and mechanical properties. Optimal orientation should be chosen to minimize the need for post-processing and to enhance mechanical strength. Typically, horizontal orientation produces smoother surfaces, while vertical orientation can offer better structural strength.
7. Unsupported Wall Thickness
In SLS 3D printing, designing unsupported walls requires careful consideration to ensure structural stability and print quality. Unsupported walls should maintain a minimum thickness of 1.0 mm to avoid warping or collapse during the printing process. For taller or larger unsupported walls, increasing the thickness to at least 1.5 mm is recommended to provide additional strength and rigidity.
Feature | Recommended size |
---|---|
Minimum wall thickness | 1.2mm |
Maximum wall thickness | 20mm |
Unsupported walls | 1.0mm |
Minimum detail size | 0.3mm |
Advantages of SLS 3D Printing
1. Complex Geometries production
SLS 3D printing allows for the creation of highly complex geometries that would be challenging or impossible to produce using traditional manufacturing methods. The absence of support structures enables intricate designs, including interlocking parts, internal channels, and lattice structures.
2. No Need for Support Structures
One of the significant advantages of SLS 3D printing is that it does not require support structures to hold up overhanging parts. The surrounding unsintered powder provides natural support during the printing process. This characteristic reduces material waste and post-processing efforts, making the printing process more efficient and cost-effective.
3. Material Versatility for SLS
SLS 3D printing is compatible with a wide range of materials, including various types of nylons, glass-filled nylons, aluminum-filled nylons, carbon-fiber-filled nylons, and thermoplastic polyurethanes (TPUs). This material versatility allows for the production of parts with different mechanical properties, tailored to specific applications, such as high-strength components, flexible parts, and heat-resistant items.
4. Durable Parts production
Parts produced through SLS 3D printing exhibit excellent mechanical properties, including high tensile strength, durability, and resistance to impact and abrasion. This makes SLS ideal for creating functional prototypes and end-use parts that need to withstand real-world conditions.
5. Reduced Waste and Cost-effective Production
The SLS process is highly efficient in terms of material usage. The unsintered powder can often be recycled and reused in subsequent print jobs, minimizing waste and reducing material costs. Additionally, the lack of support structures further decreases material consumption, making SLS a cost-effective option for both prototyping and production.
6. Scalability for Production
SLS 3D printing is suitable for both low-volume and high-volume production. Its ability to produce multiple parts simultaneously within the same build chamber makes it scalable and adaptable to varying production demands.
Limitations of SLS 3D Printing
1. Surface Finish
While SLS 3D printing excels in creating complex geometries and functional parts, the surface finish of the printed parts can be relatively rough compared to other 3D printing technologies. The powder-based process can leave a grainy texture on the surface, which might require additional post-processing such as sanding, polishing, or coating to achieve a smoother finish suitable for aesthetic or tactile purposes.
2. Dimensional Accuracy
Although SLS 3D printing generally offers good dimensional accuracy, it may not match the precision levels of technologies like SLA (Stereolithography) or DLP (Digital Light Processing). Parts can experience slight deviations from the intended dimensions due to factors like powder distribution, laser power fluctuations, and thermal stresses.
3. Post-Processing Requirements
SLS parts often require significant post-processing to achieve the desired final properties. This includes cleaning the parts from excess powder, surface finishing, and sometimes additional treatments like dyeing or coating. These post-processing steps can add time and cost to the overall manufacturing process, potentially reducing the speed and cost advantages of SLS.
4. Equipment and Operating Costs
The initial investment in SLS 3D printers can be high, with the machines being more expensive than some other 3D printing technologies. Additionally, the operating costs, including maintenance, materials, and energy consumption, can also be significant. These costs might make SLS less accessible for small businesses or hobbyists compared to more affordable 3D printing options.
5. Cooling and Warping
After printing, SLS parts need to cool down gradually within the build chamber to prevent warping or internal stresses. This cooling process can be time-consuming, potentially delaying the overall production timeline. Inadequate cooling or rapid temperature changes can lead to deformations, warping in the parts affecting the part's dimensional accuracy and mechanical properties.
6. Powder Handling and Safety
Handling and storing the fine powder used in SLS printing require careful management to prevent health risks and contamination. The powder can be a respiratory hazard if not handled properly, necessitating the use of protective equipment and controlled environments.
Applications of SLS 3D Printing
1. Prototyping and Product Development
SLS is extensively used for rapid prototyping in industries such as automotive, aerospace, and consumer goods. Its capability to create intricate geometries and functional prototypes allows designers to iterate designs quickly and test concepts before committing to full-scale production. This accelerates the product development cycle and enables more informed decision-making.

2. Customized Medical Devices
In the medical field, SLS 3D printing is utilized for creating customized prosthetics, orthotics, and implants tailored to individual patient anatomy. The ability to produce complex and patient-specific designs ensures better fit, comfort, and functionality, improving patient outcomes. SLS is also used for manufacturing surgical guides and anatomical models used in pre-operative planning and medical training.

3. Jigs and Fixtures
Manufacturing industries leverage SLS for producing tooling components, jigs, and fixtures used in assembly processes. These tools require high durability, dimensional accuracy, and customization to meet specific production needs.

4. Educational and Research Applications
SLS 3D printing plays a significant role in educational institutions and research facilities for prototyping, experimentation, and educational purposes. Students and researchers use SLS to explore design concepts, study material properties, and develop innovative solutions across various disciplines, including engineering, architecture, and biomedical sciences.

5. Customized Fashion product
Selective Laser Sintering (SLS) 3D printing is transforming the fashion industry by enabling the creation of custom-fit and innovative products that were previously unattainable. This technology allows designers to produce intricate and highly customized footwear, and complex lattice structures for enhanced comfort.

Conculsion
Selective Laser Sintering (SLS) 3D printing has emerged as a powerful and versatile manufacturing technology with wide-ranging applications across various industries. Its ability to produce complex geometries, durable and functional parts, and customized products without the need for support structures distinguishes it from other 3D printing methods. Despite some limitations, such as surface finish roughness and post-processing requirements, SLS remains a cost-effective and efficient solution for both prototyping and production. The technology’s adaptability and scalability make it particularly valuable for industries ranging from aerospace and automotive to medical devices and fashion.
While SLS 3D printing brings significant advantages, it requires a considerable investment in printers and materials and supporting infrastructure. If you want to focus on your core projects and avoid the complexities and expenses associated with SLS 3D printing, our team at https://iamrapid.com and is here to support you. You can rely on us to deliver the appropriate parts for your unique requirements. Contact us at out https://iamrapid.com and to utilize our SLS 3D printing services and expedite your innovation journey. If you found this information helpful, please share it with your peers who are also engaged in innovation.