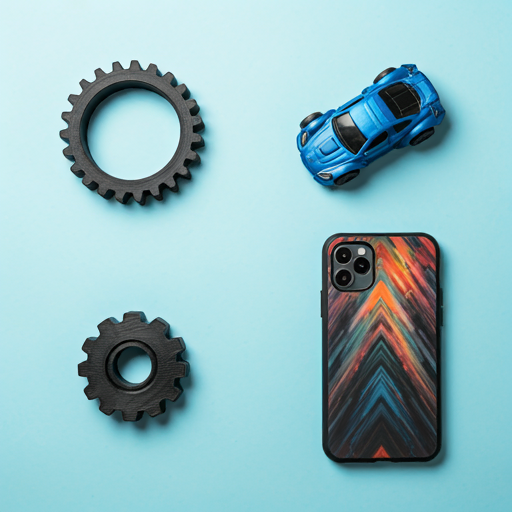
Introduction to FDM 3D Printing
Fused Deposition Modeling (FDM), also known as Fused Filament Fabrication (FFF), is one of the most widely used 3D printing technologies. FDM works by extruding a thermoplastic filament through a heated nozzle, which melts the material and deposits it layer by layer to build a three-dimensional object. The build platform moves accordingly to create the desired shape, with each layer adhering to the previous one until the entire model is complete. FDM is popular due to its cost-effectiveness, ease of use, and the availability of a wide range of materials, including PLA, ABS, PETG, and more. This technology is commonly used for prototyping, educational purposes, and small-scale production across various industries, offering a practical and accessible means of bringing digital designs to life.
FDM's ability to produce complex geometries and functional prototypes makes it a versatile choice for designers and engineers. Additionally, advancements in material science and printer technology continue to expand its applications, from consumer goods to aerospace components.

How does FDM 3D Printing Works ?
Fused Deposition Modeling (FDM) 3D printing operates through a sequential, additive process that builds objects layer by layer. Here's a detailed step-by-step explanation of how FDM 3D printing works:
- Design and Slicing : The process starts with creating a digital 3D model using computer-aided design (CAD) software. This model is then imported into slicing software, which converts the 3D model into thin horizontal layers and generates a path for the printer's nozzle to follow. The slicing software also creates instructions for the printer, detailing the movement, speed, and extrusion rate required for each layer.
- Preparation : The sliced file is transferred to the FDM printer, typically via an USB, or Wi-Fi. The printer is then prepared by loading a spool of thermoplastic filament into the extruder. Common filament materials include PLA (Polylactic Acid), ABS (Acrylonitrile Butadiene Styrene), PETG (Polyethylene Terephthalate Glycol), and more specialized materials like flexible TPU or high-strength nylon.
- Heating and Extrusion : The printer's extruder heats the filament to its melting point. The molten plastic is then pushed through the heated nozzle. The printer's build platform, also known as the print bed, moves in a precise manner, or in some printer designs, the nozzle itself moves while the platform remains stationary.
- Layer-by-Layer Deposition : Following the instructions from the slicing software, the nozzle extrudes the molten plastic onto the build platform in a precise path. The material quickly cools and solidifies as it is deposited. The platform then moves slightly down, or the nozzle moves up, allowing the next layer to be deposited on top of the previous one. Each new layer fuses with the layer beneath it, creating a solid structure.
- Supports and Overhangs : For parts with overhangs or complex geometries, the slicing software generates support structures. These temporary structures hold up any features that would otherwise collapse during the printing process. These supports are typically printed in the same material as the part or in a different, easily removable material if the printer supports dual extrusion.
- Cooling and Solidification : As each layer is deposited, it cools and solidifies almost immediately. The process continues, layer by layer, until the entire object is completed. The cooling rate and bonding between layers are crucial for the part's structural integrity and surface finish.
- Post-Processing : Once the printing is complete, the printed object is removed from the build platform. If support structures were used, they are carefully removed. Additional post-processing steps may include sanding, polishing, painting, or applying a chemical finish to improve the part's appearance and functionality.
Overview of Industrial and Desktop FDM 3D Printing
Industrial FDM 3D Printing

Industrial Fused Deposition Modeling (FDM) 3D printers are high-end machines designed for manufacturing complex, large-scale, and high-precision parts. These printers are built to handle a wide range of advanced thermoplastic materials, including high-performance polymers such as PEEK, Ultem, and carbon-fiber-reinforced composites. Industrial FDM printers feature larger build volumes, robust build platforms, and enhanced temperature control systems to ensure consistent print quality. They often include multiple extruders for multi-material printing, automated calibration, and advanced software for intricate design capabilities. Applications of industrial FDM include aerospace components, automotive parts, medical devices, and manufacturing tooling, where the need for strength, durability, and precision is paramount. These printers are also integrated into production lines for low-volume manufacturing, reducing the need for traditional tooling and enabling rapid iteration and customization.
Desktop FDM 3D Printing

Desktop FDM 3D printers are more compact, affordable, and user-friendly machines suitable for individual users, hobbyists, educators, and small businesses. These printers are typically used for creating prototypes, educational models, and custom parts with materials such as PLA, ABS, PETG, and flexible filaments. While they offer smaller build volumes compared to industrial machines, desktop FDM printers are still capable of producing detailed and functional parts. They often feature simple user interfaces, open-source software, and easy-to-replace components, making them accessible to a wide audience. Despite their smaller size, desktop FDM printers continue to advance in capabilities, with some models offering dual extrusion, improved bed leveling systems, and higher resolution printing. These printers are ideal for rapid prototyping, product development, and educational purposes, allowing users to bring their designs to life with minimal investment and technical expertise.
Our SLA 3D Printing Capabilities
Requirement | Specification |
---|---|
Maximum build size | 1000 * 1000 * 500 mm |
Standard lead tome | 4 business days |
Dimensional Accuracy | 0.5 mm |
Layer height | 100-300 um |
Infill | 20-100 % |
Available Materials for FDM 3D Printing
PLA (Polylactic Acid):
PLA is a biodegradable thermoplastic known for its ease of use and vibrant color options, making it popular for prototypes and educational projects.
ABS (Acrylonitrile Butadiene Styrene):
ABS is a strong, impact-resistant material that withstands mechanical stress well, commonly used for functional parts and consumer goods.
PETG (Polyethylene Terephthalate Glycol):
PETG offers durability, flexibility, and chemical resistance, making it suitable for mechanical components and containers, while being easier to print than ABS.
Nylon (Polyamide):
Nylon is valued for its high strength, flexibility, and resistance to wear, making it ideal for functional parts such as gears and bearings.
TPU (Thermoplastic Polyurethane)
TPU is a flexible, rubber-like material known for its excellent elasticity and impact resistance, used in applications requiring flexibility and durabilit
Materials | Melting Temperature in °C | Glass transition temperature in °C |
---|---|---|
PLA | 180-210 | ~55-60 |
ABS | 220-270 | ~105 |
PETG | 220-260 | ~88 |
Nylon | 220-250 | ~42 |
TPU | 220-240 | ~60 |
Design Guidelines for FDM 3D Printing
Designing for Fused Deposition Modeling (FDM) 3D printing requires understanding the unique constraints and capabilities of the technology to optimize print quality and performance. Here are key guidelines:
- Wall Thickness : Maintain a minimum wall thickness of 1-2 mm to ensure structural integrity. Thinner walls may not print correctly or could be fragile, while thicker walls improve durability.
- Layer Height : Choose an appropriate layer height, typically between 0.1 and 0.3 mm. Smaller layer heights result in finer details and smoother surfaces but increase print time. Larger layer heights speed up printing but reduce detail and surface finish.
- Overhangs and Support: Maintain a minimum wall thickness to ensure structural integrity. Typically, this is around 0.5 mm to 1 mm, depending on the material and part size.

- Orientation : Orient parts to optimize strength and surface finish. Layers are weakest between each other, so align critical features to minimize stress across layer lines. Consider the surface finish: the bottom layers often have a rougher finish due to bed contact.
- Fillet and Chamfer : Add fillets (rounded corners) and chamfers (angled edges) to corners to reduce stress concentrations and improve strength. Fillets can help prevent warping and enhance the overall strength of the part.
- Holes and Gaps : Design holes and gaps larger than their final intended size, as FDM printers tend to produce slightly smaller holes due to material shrinkage. A general rule is to oversize holes by 0.2-0.3 mm.
- Infill Density : Select an appropriate infill density based on the required strength and weight of the part. Common infill densities range from 20% for light, non-structural parts to 100% for maximum strength. Complex geometries can benefit from higher infill densities to improve mechanical properties.
- Design with a tolerance of 0.1-0.2 mm for parts that need to fit together. This accounts for variations in printer precision and material properties. Test and adjust tolerances based on the specific printer and filament used.
Feature | Recommended Size |
---|---|
Suggested minimum wall thickness | 1.2 mm |
Supported wall thickness | 0.8 mm |
Un-supported wall thickness | 0.8 mm |
Minimum feature size | 1.2 mm |
Minimum hole size | 2 mm |
Limitations of FDM 3D Printing
Fused Deposition Modeling (FDM) 3D printing, while versatile and accessible, has several limitations that can affect the quality and functionality of the printed objects. Understanding these limitations is crucial for optimizing designs and setting realistic expectations. Here are the main limitations of FDM 3D printing:
Surface Finish and Resolution
FDM typically produces parts with visible layer lines, resulting in a rougher surface finish compared to other 3D printing technologies like SLA (Stereolithography) or SLS (Selective Laser Sintering). Achieving fine details and smooth surfaces requires smaller layer heights, which significantly increases print time.
Anisotropy
FDM parts are anisotropic, meaning their strength varies depending on the orientation. Parts are generally weaker along the Z-axis (vertical direction) due to the nature of layer-by-layer construction, which can result in poor inter-layer adhesion and reduced mechanical properties in that direction.
Support Structures
Complex geometries and overhangs often require support structures to prevent sagging and deformation during printing. Removing these supports can be time-consuming and may leave marks or damage the surface of the part. Designing parts to minimize the need for supports can be challenging and limit design freedom.
Warping and Shrinkage
Materials like ABS and Nylon are prone to warping and shrinkage during cooling, which can lead to parts detaching from the build plate or distorting. This issue is especially prevalent in larger prints and can be mitigated with heated build plates, enclosures, and proper bed adhesion techniques, but it remains a challenge.
Material Limitations
FDM primarily uses thermoplastic materials, which may not offer the same mechanical, thermal, or chemical properties as materials used in other 3D printing technologies like metal or resin-based systems. Although advanced materials like carbon fiber composites and high-performance polymers (e.g., PEEK, ULTEM) are available, they often require specialized printers and come at a higher cost.
Post-Processing Requirements
Parts printed with FDM often require post-processing steps to achieve desired surface quality and mechanical properties. This can include sanding, smoothing, painting, or annealing. These additional steps can add time and labor costs to the overall production process.
Dimensional Accuracy
FDM printers can struggle with maintaining tight tolerances and dimensional accuracy, especially for small features and intricate designs. Factors such as nozzle diameter, layer height, and material properties influence accuracy, and achieving precise dimensions may require extensive calibration and optimization.
Environmental Impact
While PLA is biodegradable and relatively eco-friendly, other common FDM materials like ABS and PETG are petroleum-based and not biodegradable. Additionally, failed prints, supports, and excess material contribute to plastic waste. Recycling options for FDM materials are limited, although initiatives are emerging to address this issue.
Applications of FDM 3D Printing
Fused Deposition Modeling (FDM) 3D printing is widely utilized across various industries due to its versatility, affordability, and ease of use. Here are detailed descriptions of some key applications:
Prototyping

FDM is a popular choice for rapid prototyping due to its ability to quickly produce functional models and design iterations. Engineers and designers use FDM printers to create prototypes that allow for physical testing and validation of concepts before moving to mass production. This iterative process helps in identifying design flaws, making improvements, and reducing overall development time and costs.
Manufacturing Aids

In manufacturing environments, FDM is used to create custom tools, jigs, fixtures, and other aids that streamline production processes. These aids are tailored to specific tasks, improving efficiency and reducing errors. By printing these components on-demand, manufacturers can save time and money compared to traditional manufacturing methods, which often involve long lead times and higher costs.
Educational Tools

In educational settings, FDM printers serve as valuable tools for teaching students about design, engineering, and manufacturing. Schools and universities use 3D printing to create models and hands-on learning aids that help students better understand complex concepts. Additionally, FDM allows students to bring their creative ideas to life, fostering innovation and practical skills that are essential in modern industries.
Architectural Models

Architects use FDM printing to create detailed scale models of buildings and landscapes. These models help in visualizing projects, presenting designs to clients, and refining architectural concepts. The ability to quickly produce and modify models based on client feedback makes FDM an invaluable tool in the architectural design process.
Aerospace and Automotive

In aerospace and automotive industries, FDM is used to produce lightweight and complex parts that meet specific performance requirements. Engineers create functional prototypes, custom fixtures, and even some end-use parts that are critical in these high-performance sectors. The technology's ability to reduce weight while maintaining structural integrity is particularly valuable in these applications, where every gram matters.
Medical and Dental

The medical and dental fields benefit from FDM printing through the creation of patient-specific models, surgical guides, and customized medical devices. For instance, doctors can use 3D-printed models of patients' anatomy to plan surgeries more accurately. Dentists use FDM to create custom orthodontic devices and dentures, improving patient care and treatment outcomes.
Consumer Electronics

FDM is used to create custom enclosures, mounts, and components for consumer electronics. The ability to design and print specific parts allows for greater customization and innovation in product design. This application is particularly useful for hobbyists and small businesses developing new electronic gadgets and devices.
About us
If you want to get something 3D printed , please Click here to get instant quotation . You will get all the information about the necessary features , material required , cost and colour in our quotation system as you upload .stl files of your model to be 3D printed by either of the technology including FDM, SLA, SLS, etc. Please give us atleast one chance to serve you and we will not disappoint you .
Conculsion
Fused Deposition Modeling (FDM) 3D printing stands out as a versatile and accessible technology that has significantly impacted various fields, from prototyping and manufacturing to education and art. Its cost-effectiveness and ease of use have democratized access to 3D printing, enabling individuals and small businesses to innovate and create custom solutions tailored to specific needs. While it has limitations such as surface finish quality and anisotropic strength, advancements in materials and printer capabilities continue to expand its applications. As FDM technology evolves, it will play an increasingly integral role in modern manufacturing, design, and beyond, bridging the gap between digital concepts and physical reality.
For any queries related to above content on FDM 3D printing, please visit our official website https://iamrapid.com and please share this valuable content among others to spread awareness about FDM 3D printing technology.Together, we can inspire innovation and propel the adoption of this ground breaking technology.