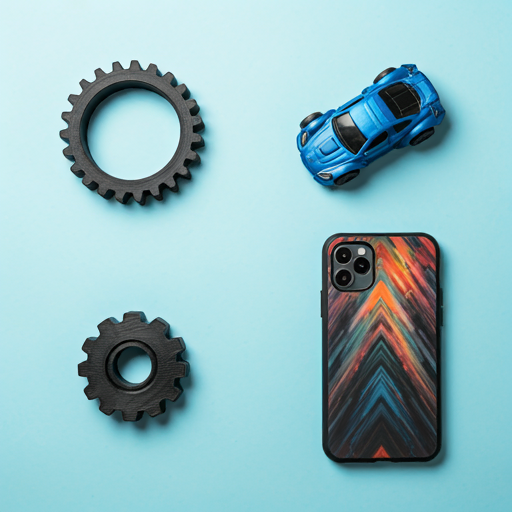
3D Printing In Robotics industry
3D printing technology has revolutionized the way we design and manufacture products, including robots. The ability to produce complex and customized parts quickly and at a relatively low cost has led to an increased use of 3D printing in the field of robotics.
One of the main advantages of using 3D printing in robotics is the ability to create highly customized parts and components. This allows for the creation of robots with unique geometries and shapes that would be difficult or impossible to produce using traditional manufacturing methods. Additionally, 3D printing allows for the creation of internal structures that can significantly reduce the weight of robots while maintaining strength and durability.
Another advantage of 3D printing in robotics is the ability to quickly and efficiently produce replacement parts. This can be especially beneficial for robots that are used in harsh environments or for those that are subject to wear and tear. By using 3D printing, engineers can produce replacement parts on-demand, reducing the need to keep a large inventory.
3D printing also allows for faster production times compared to traditional manufacturing methods, which can be especially beneficial for companies looking to quickly develop and launch new robots. Additionally, the process of 3D printing produces minimal waste, which can result in cost savings and a reduction in environmental impact.
3D printing technology also allows for the production of robots with high precision and accuracy, which is essential for various applications in fields such as medical, mining, and manufacturing. Furthermore, 3D printing technology also allows for the production of robots with high flexibility, adaptability, and dexterity, which is essential for various applications in fields such as search and rescue, space exploration, and exploration of hazardous environments.
Use of 3D printing is Accelerating Industrial Robot Development

3D printing, also known as additive manufacturing, is revolutionizing the way industrial robots are being developed. The technology allows for rapid prototyping and the creation of complex parts and structures with precision and efficiency. This has led to the development of new, advanced industrial robots that are more versatile and capable than ever before.
One of the biggest advantages of using 3D printing in the development of industrial robots is the ability to create custom, one-of-a-kind parts. This allows manufacturers to tailor their robots to specific tasks and environments, resulting in more efficient and effective machines. Additionally, 3D printing allows for the creation of complex geometries and internal structures that would be difficult or impossible to create using traditional manufacturing methods.
Another advantage of using 3D printing in the development of industrial robots is the ability to quickly and easily make changes to the design of the robot. This allows manufacturers to iterate on their designs and improve their robots in a fraction of the time it would take using traditional methods.
3D printing is also being used to create end-use parts for industrial robots. This allows for the robots to be more durable and reliable, reducing the need for maintenance and repairs.
In addition, 3D printing is helping to reduce the cost of industrial robot development. Traditional manufacturing methods can be costly and time-consuming, whereas 3D printing allows manufacturers to create parts and structures quickly and at a fraction of the cost.
Overall, the use of 3D printing is accelerating the development of industrial robots by allowing for more efficient and effective design, faster iteration, and reduced costs. As the technology continues to advance, it is likely that we will see even more advanced and capable industrial robots in the future.
Application of 3D printing in robotics industry
1.3D printed prosthetic hand

A 3D printed robotic prosthetic hand is a type of prosthetic device that is created using 3D printing technology. These hands are designed to mimic the function of a human hand and can be customized to fit the individual user's needs. They can be controlled through a variety of methods, including muscle signals, brain signals, or a combination of both. 3D printed robotic prosthetic hands can be made at a fraction of the cost of traditional prosthetic hands, and can be created in a shorter time frame. They are also lightweight, durable and can be easily adjusted. The use of 3D printing in the development of prosthetic hands is a rapidly growing field, and it is expected that this technology will continue to improve and evolve in the future.
2.3D printed robotic exoskeleton

A 3D printed exoskeleton is a wearable device that is designed to enhance the strength and mobility of the wearer. It is created using 3D printing technology, which allows for the creation of complex and customized structures. The exoskeleton is typically worn on the legs or arms and is powered by motors or other mechanical devices. It can be controlled by the wearer or by an external controller. 3D printed exoskeletons can be used to assist people with mobility impairments, such as those with spinal cord injuries or stroke. They can also be used to enhance the performance of healthy individuals, such as in the field of sports and rehabilitation. 3D printing allows for the exoskeleton to be lightweight, durable and can be easily adjusted to fit the individual wearer. The use of 3D printing in the development of exoskeletons is a rapidly growing field, and it is expected that this technology will continue to improve in the future.
3.3D printed robotic dogs

A 3D printed exoskeleton is a wearable device that is designed to enhance the strength and mobility of the wearer. It is created using 3D printing technology, which allows for the creation of complex and customized structures. The exoskeleton is typically worn on the legs or arms and is powered by motors or other mechanical devices. It can be controlled by the wearer or by an external controller. 3D printed exoskeletons can be used to assist people with mobility impairments, such as those with spinal cord injuries or stroke. They can also be used to enhance the performance of healthy individuals, such as in the field of sports and rehabilitation. 3D printing allows for the exoskeleton to be lightweight, durable and can be easily adjusted to fit the individual wearer. The use of 3D printing in the development of exoskeletons is a rapidly growing field, and it is expected that this technology will continue to improve in the future.
4.3D printed wheels for rover

3D printed wheels for rovers are a recent development in the field of space exploration, allowing for more efficient and cost-effective production of these critical components. These wheels are created using 3D printing technology, which allows for the creation of complex and customized structures with precision and efficiency. The wheels are designed to withstand the harsh conditions of space, including extreme temperatures and rough terrain. They can be made in a variety of materials, including metals, plastics, and composites. 3D printed wheels are lightweight, durable and can be easily adjusted to fit the specific needs of the rover. The use of 3D printing in the development of rover wheels is a rapidly growing field, and it is expected that this technology will continue to improve in the future, making space exploration more accessible and cost-effective.
Advantages of using 3D printing in robotic industry

The use of 3D printing in the robotic industry has brought about many advantages that have revolutionized the way robots are designed and manufactured. Here are some of the main advantages of using 3D printing in the robotic industry:
- Increased Design Flexibility : 3D printing allows for the creation of complex geometries and designs that would be difficult or impossible to produce using traditional manufacturing methods. This increased design flexibility allows for the creation of robots with unique shapes and capabilities that can perform tasks that were previously impossible.
- Faster Prototyping : 3D printing allows for the rapid prototyping of robot designs, which allows for quicker iterations and testing of different designs. This can lead to faster development times and the ability to bring new products to market quicker.
- Cost Savings : 3D printing can save costs by reducing the need for expensive tooling and molds. This is particularly useful for small-scale production runs or for creating one-off prototypes. Additionally, 3D printing can reduce the need for expensive materials as it allows for the use of a wide range of materials, including composites and plastics.
- Customization : 3D printing allows for the creation of customized robots that are tailored to specific tasks or environments. This can be particularly useful for the creation of specialized robots for use in niche industries such as agriculture, mining, and healthcare.
- Reduced Waste : 3D printing can reduce waste by only using the exact amount of material needed for a specific part or design. This can help to reduce costs and minimize the environmental impact of production.
- Greater Precision : 3D printing can produce parts with very high levels of accuracy and precision, which is important for the creation of robots that must perform complex tasks. This can help to improve the performance and reliability of robots, making them more effective and efficient.
- Better Repairability : 3D printing can also be used to repair or replace broken parts on robots, which can save costs and minimize downtime. This can be particularly useful for robots that are used in remote or hard-to-reach locations.
- Greater Accessibility : 3D printing has made it easier for small companies and individuals to enter the robotic industry, as the technology is relatively inexpensive and easy to use. This has led to an increase in innovation and competition, which can drive the industry forward.
3D printing technologies that are commonly used to develop robots
1.Stereolithography (SLA):

SLA is a technology that uses a laser to cure a liquid resin into a solid object. The laser is directed onto a surface of the resin, curing a thin layer of the material. The process is repeated until the entire object is created. This technology is commonly used to create highly detailed and precise robotic parts, such as sensors and grippers.
2.Fused Deposition Modeling (FDM):

FDM is a popular 3D printing technology that uses a plastic filament that is heated and extruded through a nozzle to create a 3D object. The plastic is extruded in a thin layer and is built up layer by layer to create the final product. This technology is commonly used to create robotic parts such as gears, actuators, and frames..
3.Selective Laser Sintering (SLS):

SLS is a technology that uses a laser to fuse powdered materials together, creating a solid object. The powder is spread over a build platform, and the laser is used to fuse the material in a specific pattern. This process is repeated until the entire object is created. SLS is commonly used to create robust and durable robotic parts, such as gears, actuators, and frames.
4.Direct Metal Laser Sintering (DMLS):

DMLS is a type of 3D printing technology that uses a laser or an electron beam to melt and deposit metal powders or wire onto a substrate. It is commonly used to create complex geometries, such as robotic parts with internal channels or lattice structures.
What 3D printing materials should you choose to develop a robot
When developing a robot, the choice of 3D printing material will depend on the specific requirements of the robot and the properties of the final product. Here are some commonly used 3D printing materials for robots:
- ABS (Acrylonitrile Butadiene Styrene) : ABS is a thermoplastic that is commonly used to create robotic parts that require a high level of strength and durability. It is also a good material for gears, actuators and frames.
- PLA (Polylactic Acid) : PLA is a biodegradable thermoplastic that is commonly used to create robotic parts that require a high level of precision and detail. It is also a good material for gears, actuators and frames.
- TPU (Thermoplastic Polyurethane) : TPU is a flexible and durable material that is commonly used to create robotic parts that require a high level of flexibility, such as grippers and flexible joints.
- Nylon : Nylon is a strong and durable material that is commonly used to create robotic parts that require a high level of strength and durability. It is also a good material for gears, actuators and frames.
- Metal : There are different types of metal that can be used in the development of robots, such as stainless steel, titanium, aluminum and others. These materials are commonly used to create robotic parts that require a high level of strength and durability.
- Carbon fiber : Carbon fiber is a composite material made of carbon fibers and resin. It is commonly used in the development of robots that require a high level of strength and lightweight.
- Ceramic : Ceramic is a hard and brittle material that is commonly used in the development of robots that require a high level of wear and corrosion resistance.
It is important to note that the selection of the 3D printing material will depend on the specific requirements of the robot and the properties of the final product. Factors such as size, strength, flexibility, precision and the environment will all play a role in determining the best material to use.