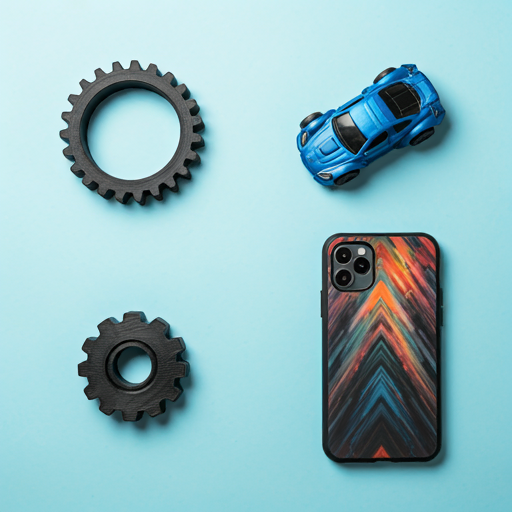
3D Printing in Automobile Industry
3D printing, also known as additive manufacturing, is a process of creating three-dimensional objects by laying down successive layers of material. In the automobile industry, 3D printing is being used to create prototype parts, tooling, and even final products.
One of the key advantages of 3D printing in the automobile industry is the ability to quickly and easily create complex, customized parts. For example, a car manufacturer can use 3D printing to create a prototype part that is designed to fit a specific make and model of car. This not only speeds up the design process, but also allows for greater flexibility in the final product. Additionally, 3D printing can be used to create tooling, such as molds and jigs, which can be used in the manufacturing process.
Another advantage of 3D printing in the automobile industry is the ability to reduce costs. Traditional manufacturing methods, such as injection molding, can be expensive and time-consuming. With 3D printing, manufacturers can create parts and tooling in a fraction of the time and at a fraction of the cost. This not only saves money but also allows for greater experimentation and innovation in the design process.
Moreover, the use of 3D printing in the automobile industry is not only limited to prototyping and manufacturing but also in creating final parts of the cars. This allows for greater customization, as well as the ability to create lightweight, strong parts that can improve the performance of the car.
3D printing technology is also being used in dental education and research. With the ability to produce realistic models of teeth, bones and other oral structures, students and researchers can gain a better understanding of dental anatomy and physiology. This helps to advance the field of dentistry and to develop new and improved treatments and technologies.
Overall, 3D printing is becoming an increasingly important technology in the automobile industry. It offers many benefits, such as the ability to quickly and easily create customized parts, reduce costs, and improve the performance of the final product. As the technology continues to advance, it is likely that 3D printing will become even more widely used in the automobile industry in the future.
Future of 3D Printing Technology in the Automobile Industry


The future of 3D printing technology in the automobile industry looks bright, as the technology continues to evolve and improve. One of the key areas where 3D printing is expected to have a significant impact is in the area of mass customization. As 3D printing technology becomes more advanced and more widely available, it will become increasingly easy for car manufacturers to create customized parts and components for individual customers. This will allow for greater flexibility in the design process and will enable manufacturers to create cars that are tailored to the specific needs and preferences of individual customers.
Another area where 3D printing is expected to have a significant impact is in the area of lightweighting. One of the key challenges facing the automobile industry is the need to create cars that are more fuel efficient and have lower emissions. 3D printing can help to achieve this by allowing manufacturers to create lightweight, strong parts that can improve the performance of the car. This will not only help to improve fuel efficiency, but also reduce emissions, making it an environmentally friendly technology.
3D printing is also expected to have a significant impact on the way cars are manufactured in the future. Traditional manufacturing methods, such as injection molding, can be expensive and time-consuming. With 3D printing, manufacturers can create parts and tooling in a fraction of the time and at a fraction of the cost. This will not only save money, but also allow for greater experimentation and innovation in the design process.
5 Best Advantages Of Using 3D printing technology in the Automobile industry
3D printing technology offers a wide range of advantages for the automobile industry. From speed and efficiency to customization and cost savings, 3D printing is set to play a major role in shaping the cars of the future. As the technology continues to evolve and improve, it is likely that more and more manufacturers will turn to 3D printing to create parts and tooling that are faster, cheaper, and more customizable than ever before. Furthermore, with the advancements in material science, 3D printing will enable the creation of parts that are more durable and sustainable than traditional manufacturing methods, making it a vital technology for the automobile industry.

- Speed and Efficiency : One of the biggest advantages of using 3D printing technology in the automobile industry is the speed and efficiency of the process. Traditional manufacturing methods, such as injection molding, can be time-consuming and labor-intensive. With 3D printing, manufacturers can create parts and tooling in a fraction of the time, which can significantly speed up the design and manufacturing process. This allows manufacturers to get their products to market faster and respond more quickly to changes in consumer demand.
- Customization : Another advantage of using 3D printing technology in the automobile industry is the ability to create customized parts and components. With 3D printing, manufacturers can create parts that are tailored to the specific needs and preferences of individual customers. This allows for greater flexibility in the design process and enables manufacturers to create cars that are more closely aligned with the preferences of their customers.
- Cost Savings : 3D printing technology can also help manufacturers save money by reducing the cost of traditional manufacturing methods. With 3D printing, manufacturers can create parts and tooling at a fraction of the cost of traditional methods. This not only saves money, but it also allows manufacturers to experiment with new designs and materials without incurring significant costs.
- Lightweighting : One of the key challenges facing the automobile industry is the need to create cars that are more fuel efficient and have lower emissions. 3D printing can help to achieve this by allowing manufacturers to create lightweight, strong parts that can improve the performance of the car. This can help to reduce the weight of the car, which in turn can improve fuel efficiency and reduce emissions.
- Advancements in Materials Science : With the recent advancements in materials science, new materials that can be 3D printed are being developed. This includes the development of metal alloys, ceramics and polymers for printing, which will enable the printing of parts that are stronger and more durable than ever before. This will not only improve the performance of the car but also give the manufacturers a wider range of options to choose from while making the parts.
Key Design Considerations for Automobile 3D printing parts

When designing parts for 3D printing in the automobile industry, there are several key considerations to keep in mind:
- Material selection : The material used for 3D printing will have a significant impact on the strength and durability of the final product. It is important to choose a material that is suitable for the intended application and that will meet the required performance specifications. Some common materials used in the automobile industry include ABS, PLA, Nylon, and various metal alloys.
- Strength and durability : Automobile parts need to be strong and durable to withstand the rigors of use. 3D printed parts should be designed with this in mind, taking into account factors such as stress points, load-bearing capacity, and impact resistance.
- Thermal expansion : 3D printed parts will expand and contract with changes in temperature. This needs to be taken into account when designing the parts to ensure that they will not warp or deform under normal operating conditions.
- Surface finish : The surface finish of 3D printed parts can affect their appearance and functionality. It is important to consider the required surface finish and to choose a 3D printing process that will produce the desired result.
- Assembly and tolerances : When designing parts for 3D printing, it is important to take into account the assembly process and the tolerances required for the parts to fit together properly. This includes considering the size and position of mating surfaces, as well as the tolerances for fit and function.
- File Format and Slicing software : The file format used for the 3D model and the slicing software used to prepare the model for printing can affect the final quality of the printed part. It is important to choose a file format and software that are compatible with the 3D printer and that will produce the desired result.
- Post-processing : Post-processing is an important step in the 3D printing process, as it can affect the final quality and functionality of the printed parts. It is important to consider the type of post-processing required, such as sanding, polishing, or painting, and to choose a 3D printing process that will produce the desired result.
3D printing technologies that are commonly used for manufacturing Automobile components
1.Fused Deposition Modeling (FDM):

FDM is a popular 3D printing technology that uses a thermoplastic material that is extruded through a heated nozzle. The material is laid down in a layer-by-layer process to create the final object. FDM is commonly used for prototyping and creating small-scale parts, such as tooling, jigs, and fixtures.
2.Stereolithography (SLA):

SLA is a 3D printing technology that uses a UV laser to cure a liquid resin into a solid object. The laser traces a cross-section of the object on the surface of the resin, solidifying it in that area. SLA is commonly used for creating high-precision parts and prototypes with fine details, such as automotive lighting systems.
3.Selective Laser Sintering (SLS):

SLS is a 3D printing technology that uses a laser to sinter a powder material, such as nylon or metal, into a solid object. The laser traces a cross-section of the object on the surface of the powder, fusing the material together in that area. SLS is commonly used for creating parts with high strength and durability, such as engine components and structural parts.
4.Direct Metal Laser Sintering (DMLS):

It's a process that uses a laser or an electron beam to melt and deposit metallic powders onto a substrate, building the object layer by layer. This technology is known for its high precision and high-quality prints, and it's the perfect fit for creating intricate and detailed automobile components.