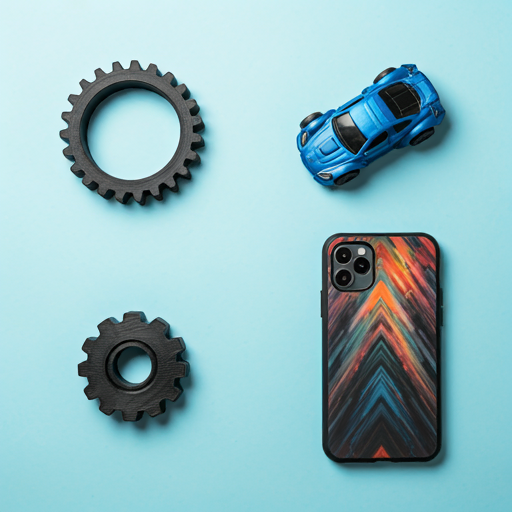
3D Printing In Aerospace industry
3D printing, also known as additive manufacturing, is a process of creating three-dimensional objects by building up layers of material. In the aerospace industry, 3D printing is being used to create a wide range of parts and components, from small mechanical parts to large structural components. This technology offers several benefits over traditional manufacturing methods, including reduced lead times, lower costs, and improved design flexibility.
One of the main advantages of 3D printing in the aerospace industry is the ability to create complex geometries that would be difficult or impossible to produce with traditional manufacturing methods. This allows for the production of lightweight and highly efficient parts, which can greatly improve the performance of aircraft and spacecraft. Additionally, 3D printing can be used to create customized parts for specific applications, which can help to reduce costs and improve the performance of aircraft and spacecraft.
Another important benefit of 3D printing in the aerospace industry is the ability to produce parts quickly and efficiently. Traditional manufacturing methods can take weeks or even months to produce a single part, while 3D printing can produce a part in a matter of hours or days. This can greatly reduce lead times and help to speed up the development of new aircraft and spacecraft.
Overall, 3D printing is a powerful tool for the aerospace industry, offering a wide range of benefits over traditional manufacturing methods. With the ability to create complex geometries, reduce costs and lead times, and improve performance, 3D printing is set to play a key role in the future of aerospace manufacturing.
Incorporating 3D printing into the aerospace design process

Implementing 3D printing in the aerospace design workflow involves several steps and considerations.
- Design : 3D printing requires a digital 3D model of the part or component to be printed. Aerospace engineers and designers must create or obtain a digital 3D model of the part that meets the necessary design specifications and requirements.
- Material selection : The aerospace industry typically uses aerospace-grade materials like titanium, aluminum, and carbon fiber for 3D printing. Engineers and designers must select the appropriate material for their application, taking into consideration factors such as strength, weight, and corrosion resistance.
- Printing process selection : Different 3D printing processes, such as Fused Deposition Modeling (FDM), Stereolithography (SLA), and Selective Laser Sintering (SLS) have different capabilities and limitations. Engineers and designers must select the appropriate printing process based on the size, complexity, and material properties of the part.
- Post-processing : 3D printed parts often require post-processing steps such as cleaning, finishing, and heat treatment to ensure they meet the necessary mechanical and material properties.
- Testing and validation : 3D printed parts must be tested and validated to ensure they meet the necessary aerospace standards and requirements. This includes testing for strength, durability, and performance under various conditions.
- Certification : 3D printed parts must be certified by the relevant regulatory bodies before they can be used in aerospace applications. This process can take time and require additional testing and validation.
Overall, implementing 3D printing in the aerospace design workflow requires a thorough understanding of the technology, materials, and regulatory requirements. It also involves close collaboration between engineers, designers, and regulatory bodies to ensure the final product meets all necessary aerospace standards and requirements.
What is future of 3D printing technology in the aerospace industry

The future of 3D printing technology in the aerospace industry looks very promising. As the technology continues to advance and improve, it will likely play an increasingly important role in the manufacturing of aerospace parts and components.
One area where 3D printing is expected to have a significant impact is in the production of complex and highly customized parts. The ability to create complex geometries and shapes that would be difficult or impossible to produce with traditional manufacturing methods will allow aerospace companies to create parts that are more lightweight and efficient. This will lead to improved performance of aircraft and spacecraft, and also help to reduce costs.
Another area where 3D printing is expected to have a major impact is in the production of large structural components. As the technology continues to improve, it will be possible to print larger and more complex parts, such as wing spars and fuselage sections. This will lead to significant cost savings as well as improved efficiency in the production process.
Additionally, 3D printing technology is also expected to play a key role in the production of low-volume and replacement parts. With 3D printing, aerospace companies will be able to produce parts quickly and efficiently, without the need for large-scale production runs. This will help to reduce lead times and improve responsiveness to customer needs.
The aerospace industry is also looking forward to the development of new materials that can be used in 3D printing. The use of advanced composites, such as carbon fiber reinforced polymer, will allow aerospace companies to create parts that are even stronger and more durable than those produced with traditional materials.
Overall, the future of 3D printing technology in the aerospace industry looks very bright, with the technology expected to play an increasingly important role in the production of aerospace parts and components. The advancements in the technology will help companies to produce parts that are more efficient, more cost-effective, and more responsive to customer needs.
Application of 3D printing technology in the aerospace industry
3D printed turbines

3D printed turbines are a promising application of 3D printing technology in the aerospace and energy industries. These turbines are typically made from aerospace-grade materials such as titanium and aluminum, which are strong and lightweight enough to withstand the high temperatures and pressures of a turbine. The use of 3D printing technology allows for the production of complex geometries and shapes that would be difficult or impossible to produce with traditional manufacturing methods. This results in more efficient and lightweight turbines that can greatly improve the performance of aircraft and power generation systems. Additionally, 3D printing can also greatly reduce lead times and costs associated with producing these components.
3D Printined UAV Drones

3D printed UAV drones are unmanned aerial vehicles that are manufactured using 3D printing technology. This allows for the creation of complex and customized designs at a relatively low cost. They are often used in a variety of applications such as aerial photography, mapping, and surveillance. 3D printing also allows for the quick and efficient replacement of parts in the event of damage. However, there are some limitations to the materials and weight that can be used in 3D printed drones. Additionally, the durability and overall performance may not be as high as those of traditionally manufactured drones. Despite these limitations, 3D printed drones are becoming increasingly popular in the industry due to their cost-effectiveness and versatility.
3D Printed Rocket Nozzle

A 3D printed rocket nozzle is a component of a rocket engine that is manufactured using 3D printing technology. This allows for the creation of complex and customized designs that are difficult or impossible to produce using traditional manufacturing methods. The nozzle is responsible for directing the high-speed exhaust gases from the combustion chamber, providing the thrust that propels the rocket. 3D printing allows for the quick and efficient production of rocket nozzles, reducing costs and lead times. However, 3D printed nozzles may not be as durable as those made using traditional manufacturing methods. Additionally, the materials used in 3D printing may not be able to withstand the high temperatures and pressures of rocket propulsion. Despite these limitations, 3D printed rocket nozzles are being increasingly used in the aerospace industry due to their cost-effectiveness and versatility.
Advantages of using 3D printing Technology in aerospace industry

- Customization : One of the main advantages of using 3D printing technology in the aerospace industry is the ability to create highly customized parts and components. This can be especially useful for creating complex geometries and shapes that would be difficult or impossible to produce using traditional manufacturing methods.
- Cost Savings : 3D printing can save a significant amount of money in the aerospace industry. Traditional manufacturing methods can be time-consuming and expensive, whereas 3D printing can produce parts and components much faster and at a lower cost. This can be especially beneficial for prototyping, small batch production, and replacement parts.
- Faster Production Times : 3D printing allows for much faster production times compared to traditional manufacturing methods. This can be especially beneficial for aerospace companies that need to produce parts quickly to meet tight deadlines or unexpected demand. Additionally, it allows for the production of replacement parts on-demand, reducing the need to keep a large inventory.
- Reduced Waste : 3D printing produces minimal waste compared to traditional manufacturing methods. The process of 3D printing is highly efficient, as it only uses the material that is needed to produce the final product. This can result in cost savings and a reduction in environmental impact.
- Weight Reduction : 3D printing technology can be used to produce lightweight parts and components for aircraft and space vehicles. This can be especially beneficial in the aerospace industry, where weight reduction can improve fuel efficiency and performance. Furthermore, by using 3D printing, engineers can create complex internal structures that can significantly reduce weight while maintaining strength and durability.
3D Printing Technologies that are commonly used in Aerospace industry
Selective Laser Sintering (SLS)

SLS is a 3D printing technology that uses a laser to selectively fuse powdered materials, such as nylon or metal, to build up the final product. SLS is commonly used in aerospace for creating complex parts, such as structural components, and for creating parts that are able to withstand high temperatures and pressures.
2. Direct Metal Laser Sintering (DMLS):

It's a process that uses a laser or an electron beam to melt and deposit metallic powders onto a substrate, building the object layer by layer. This technology is known for its high precision and high-quality prints, and it's the perfect fit for creating intricate and detailed parts.
3. Stereolithography (SLA):

SLA is a type of 3D printing that uses UV light to cure layers of a liquid resin, building up the final product. SLA is known for its high accuracy and surface finish, making it suitable for aerospace applications such as creating detailed and accurate mock-ups, and small parts with fine details.