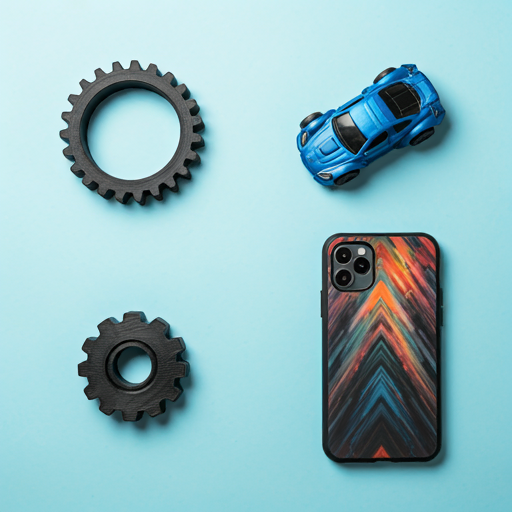
What is 3D printing ?
3D printing, or additive manufacturing, is a transformative process that constructs objects layer by layer from digital designs, revolutionizing how products are created and customized. This technology spans various fields, from rapid prototyping in industries to custom medical implants. Time is a significant factor in many industries. This technology not only saves time but also reduces waste in the industry. Neil Gershenfeld, Director of MIT's Center for Bits and Atoms, emphasizes its potential: "3D printing represents a new frontier in manufacturing, where digital data can be transformed into physical objects at the click of a button," showcasing its ability to disrupt traditional manufacturing and supply chains.
Understanding 3D printing and Rapid prototyping
3D Printing and rapid prototyping are intrinsically linked, with 3D Printing serving as a fundamental technology that enables rapid prototyping. Rapid prototyping involves creating scale models or functional parts from digital designs to test and refine ideas during product development. 3D Printing excels in this context by allowing designers and engineers to produce physical prototypes directly from CAD files created in Design software (Solidworks, Fusion360, etc.) by the user, layer by layer, in a matter of hours or days rather than weeks. In this way, the most critical factor (time) is saved by using 3D Printing. This technology accelerates the iteration process, allowing faster testing, feedback, and improvements.

Understanding 3D printing and Additive Manufacturing
3D Printing, also known as additive manufacturing, is an innovative technology that constructs objects layer by layer from digital models, transforming how products are designed and manufactured. This process allows for creating complex geometries and customized items with high precision, using materials such as plastics, metals, and ceramics. As Terry Wohlers of Wohlers Associates highlights, "3D printing is a powerful technology that has the potential to disrupt traditional manufacturing and supply chains," reflecting its transformative impact across various industries.
The Invention of 3D printing : A Brief History
The invention of 3D printing dates back to the 1980s, when it marked a significant milestone in manufacturing and design. Here is a brief history :
1980s: The Birth of 3D Printing
- 1981: Hideo Kodama of the Nagoya Municipal Industrial Research Institute in Japan first conceived the idea of a rapid prototyping system using photopolymers, materials that harden when exposed to ultraviolet light. He developed a layer-by-layer approach to manufacturing prototypes but did not commercialize his work.
- 1984: Charles Hull, an American engineer, invented stereolithography (SLA), a process that allows for creating 3D objects using photopolymerization. This process involves curing a liquid resin into solid plastic using a UV laser.
- 1986: Charles Hull co-founded 3D Systems and patented the SLA printer, launching the first commercial 3D printer, the SLA-1, in 1988.
1990s: Expanding Technologies and its Commercialisation
- 1991: The Fused Deposition Modeling (FDM) technique was developed and patented by Scott Crump, the co-founder of Stratasys. FDM works by extruding thermoplastic material (PLA, ABS, etc.) layer by layer to build objects
- 1992: Selective Laser Sintering (SLS), another pivotal 3D printing technology, was developed by Carl Deckard and Joe Beaman at the University of Texas. SLS uses a laser to sinter powdered material, fusing it to form a solid structure.
- 1993: Massachusetts Institute of Technology (MIT) developed the technology known as binder jetting, where a liquid binder is deposited onto a powder bed to build parts layer by layer.
2000s: Advancements
- 2009: The expiration of essential patents, particularly those related to FDM, led to a surge in the development of consumer-level 3D printers. This democratized access to 3D Printing, allowing hobbyists and small businesses to explore its potential.
- 2010: The first 3D-printed organ (a kidney) was created by Anthony Atala and his team at Wake Forest Institute for Regenerative Medicine, showcasing the potential of bioprinting.
- 2012: "Additive manufacturing" became more widely used, reflecting the broader range of applications beyond prototyping, including producing end-use parts
- 2015: Local Motors produced the first 3D-printed car, the Strati, illustrating the potential for 3D Printing in the automotive industry.
2020s: Continued Growth and Innovation
- 2020s: Technology continues to evolve with advancements in materials science, software, and hardware. Applications in aerospace, healthcare, construction, and other fields are expanding, demonstrating the versatility and transformative potential of 3D Printing.
3D Printing's journey from a theoretical concept and prototyping to a robust manufacturing tool reflects continuous innovation and expanding possibilities. Now, thousands of companies are running to provide all sorts of services related to 3D printing parts and their manufacturing.
In only 30 to 40 years since its discovery, this technology evolved very rapidly and became rooted in various industries, such as Aerospace, Automobiles, medicine, and health, across the globe.
How 3D printing works : A step by step guide

- Creating a Digital model: The process starts with creating a digital model using computer-aided design (CAD) software or by scanning an existing object to create a 3D model.
- Slicing the Model: The digital model is then sliced into thin horizontal layers using slicing software (CURA , Raise3D , etc.) . This software converts the 3D model into instructions that the 3D printer can understand, often in the form of G-code.
- Setting printer: The 3D printer is set up with the appropriate materials, which can include plastics, metals, resins, or other substances depending on the printing technology (FDM , SLA , SLS ,etc.) being used. The printer bed is also prepared, and the machine is calibrated to ensure precision.
-
Printing the Object: For printing the object
depending on its complexity and material , different 3D
printing technologies are used :
Different types of 3D printing processes are explained in detail below . - Layer by Layer printing: The printer constructs the object layer by layer, with each new layer bonding to the one below it. The build platform lowers incrementally after each layer is completed, allowing the next layer to be added on top.
- Curing and Post processing: Depending on the material and printing method, the object might need to cool or cure between layers or after the entire printing process. For example, objects printed with thermoplastics need to cool down, while those made with resins may require additional UV curing. Once the printing is complete, the object is removed from the printer and may undergo various post-processing steps which are discussed in detail below .
Additive vs Traditional manufacturing
Traditional Manufacturing is of two types :
- Formative Manufacturing : Formative manufacturing involves shaping materials into desired forms using moulds, dies, typically through processes like injection moulding, casting, and forging. This method relies on applying pressure or heat to mould the material into specific design and shape . It is highly efficient for mass production, as once the initial mould or die is created, thousands or even millions of identical parts can be produced quickly and cost - effectively . This method has limitations that it requires more investment in tooling and is less flexible for small batches or custom designs.
-
Subtractive Manufacturing : Subtractive
manufacturing, on the other hand, involves removing material
from a solid block or bar to create the final product. This
method is characterised by its accuracy and its ability to
create detailed products with precision.
This method has limitations that it generates a considerable amount of material waste and is generally less efficient for mass production due to the time consuming nature of the material removal processes. It also requires machinery and skilled operators, adding to the overall cost.

- Additive Manufacturing : Additive manufacturing, commonly known as 3D printing, is a manufacturing process that builds objects by fusing layers of material . This method enables the creation of complex geometries and customised items with high precision. Additive manufacturing is particularly beneficial for rapid prototyping and small production runs, as it shortens the development cycle and allows for quick modifications. Another advantage is that it significantly reduces material waste, as it only uses the material necessary to construct the object, making it more sustainable. The main limitation of additive manufacturing is that the mechanical properties of 3D-printed parts can sometimes be inferior to those produced through traditional methods, with issues such as anisotropy, where the material properties vary depending on the direction of the print layers and fluctuation in curing across the object . The initial cost of high-quality 3D printers can be very high .

Exploring 3D printing technology
Exploring the different 3D printing processes is like uncovering a toolkit of innovative possibilities, each method unlocking unique ways to transform ideas into reality with precision and creativity.
Different type of 3D printing processes :
- Material Extrusion (e.g. FDM) : A thermoplastic filament is heated and extruded through a nozzle, depositing material layer by layer.
- VAT Photopolymerisation (e.g. SLA) : Uses UV light to cure liquid resin into solid layers.
- Powder Bed Fusion (e.g. SLS) : A laser or electron beam fuses powder particles together in a bed of powdered material.
- Binder Jetting : A liquid binder is deposited onto a powder bed to fuse the material layer by layer.
- Material Jetting : Droplets of material are deposited layer by layer, similar to how an inkjet printer works but in 3D and cured by light .
- Electron Beam Melting (EBM) : Uses an electron beam to melt and fuse metal powder into solid parts in a high vacuum environment, suitable for aerospace and medical applications.
Overview of 3D printing processes :
Material Extrusion (e.g., FDM) :
Fused Deposition Modeling (FDM) involves heating a thermoplastic filament until it melts and then extruding it through a fine nozzle. The printer deposits the material layer by layer, starting from the bottom and building up to create the final object.
Advantages:
- Cost effective
- Ease of Use
- Material Variety (PLA , ABS , etc.)
Limitations:
- Lower Resolution
- Mechanical Properties
- Support Structures
VAT Photopolymerisation (e.g., SLA) :
Stereolithography (SLA) uses a UV laser or light source to cure liquid photopolymer resin layer by layer. The build platform moves down incrementally as each layer is solidified.
Advantages:
- High Resolution
- Detail and Accuracy (Excellent for intricate designs )
- Material Properties (Wide range of resins)
Limitations:
- Material Cost
- Brittle.
- Requires Post-Processing
Powder Bed Fusion (e.g., SLS) :
Selective Laser Sintering (SLS) uses a laser to fuse powdered material, such as nylon or metals, layer by layer. The unfused powder supports the part during printing, eliminating the need for support structures.
Advantages:
- No Support Structures
- Strong Parts
- Material Versatility
Limitations:
- Expensive
- Requires Post-Processing
- Energy Consumption
Binder Jetting :
Binder Jetting involves depositing a liquid binding agent onto a bed of powder, bonding the powder particles layer by layer. After printing, the object is usually cured to harden.
Advantages:
- Full Color options.
- Speed (Relatively fast)
- Material Range
Limitations:
- Requires Post-Processing
- Mechanical Properties
- Surface Finish (rougher surface finish and lower resolution.)
Material Jetting :
Material Jetting works by jetting droplets of photopolymer material, which are then cured by UV light layer by layer. This method is similar to inkjet printing but in 3D.
Advantages:
- High Resolution
- Multi-Material printing
- Accuracy
Limitations:
- Expensive
- Brittle Parts
- Requires Support Structures
Electron Beam Melting (EBM) :
EBM uses an electron beam to melt and fuse metal powder in a high vacuum environment. The process builds the part layer by layer, which is then cooled to form a solid metal object.
Advantages:
- Strong and Dense Parts
- High-Performance Applications
- Less Thermal Stress
Limitations:
- High Cost
- Energy Intensive (requires significant energy)
- Material Limitation
Optimising and evaluating 3D printing processes :
Selecting the right 3D printing process depends on several factors, including the material properties required, the complexity and resolution of the part, production speed, cost, and the intended application of the 3D printing process .
Here’s a guide to help choose the most suitable 3D printing process:
Fused Deposition Modeling (FDM)
- Best for Functional prototypes, simple geometries, budget-conscious projects.
- Material:Thermoplastics like PLA, ABS, PETG.
VAT Photopolymerisation (SLA)
- Best for High-detail parts, smooth surface finish, small to medium-sized parts.
- Material:Photopolymer resins .
Powder Bed Fusion (SLS)
- Best for Complex geometries, functional parts with high strength, no support structures needed.
- Material:Polymers, metals (DMLS/SLM for metals).
Binder Jetting
- Best for Full-color prototypes, medium volume production, variety of materials.
- Material:Metals, ceramics, sand, and composites.
Material Jetting
- Best for High-resolution, multi-material, and full-color parts.
- Material:Photopolymers.
Electron Beam Melting (EBM)
- Best for High-performance metal parts, aerospace and medical applications.
- Material:Titanium, cobalt-chrome alloys, and other metals.
3D printing materials
Comprehensive overview of 3D printing materials
3D printing has revolutionised manufacturing by enabling the creation of complex designs using a wide variety of materials. From plastics to metals to composites, the range of materials compatible with 3D printing processes continues to expand, opening up new possibilities for functional prototypes, end-use parts, and customised products.
Emerging Trend
In 2023, several emerging trends in 3D printing materials are set to revolutionise the industry. One notable trend is the increasing use of metal 3D printing, particularly with metal polymers, which enable the production of complex metal parts with reduced waste and lower costs compared to traditional manufacturing .
Another trend is the development of innovative, eco-friendly materials, such as biodegradable plastics, that prioritise sustainability and reduce environmental impact . Advanced materials like ceramics and composites are also gaining pull, offering enhanced durability and unique properties for a wide range of applications .
Common 3D printing materials
3D printing uses a wide range of materials, each with unique properties suited for different applications.
Material | Properties | Examples |
---|---|---|
Plastics/Polymers | Lightweight, affordable, and versatile. Suitable for prototypes and some end-use parts. | PLA, ABS, Nylon, PC, TPU |
Metals | Strong, durable, and heat-resistant. Used for functional parts in industries like aerospace and automotive. | Stainless steel, titanium, aluminium |
Ceramics | Hard, brittle, and heat-resistant. Offer unique properties for specialized applications. | Alumina, silicon nitride |
The choice of material depends on the specific requirements of the application, such as strength, flexibility, heat resistance, and cost. As 3D printing technologies advance, the range of compatible materials continues to expand, enabling new possibilities for additive manufacturing.
3D printing : Post Processing
3D printing has revolutionised manufacturing, but creating high-quality parts often requires an essential step after printing: post-processing. Post-processing techniques enhance the quality, appearance, and mechanical properties of 3D printed parts, addressing issues like layer lines, support marks, and rough surfaces to ensure parts meet the desired functionality and aesthetics.

Techniques for smoothing layer lines
- Surface Finishing : To make the surface of a 3D print smooth, you can sand it with sandpaper, starting with rough paper and moving to finer paper. You can fill any gaps or rough spots with putty or resin, then apply a primer to prepare it for painting. Polishing can also make the surface shiny, especially for plastic and metal prints.
- Applying Paint : Spray painting provides a uniform colour coat and may require multiple layers for full coverage.Dyeing is effective for materials like nylon from SLS printing, where textile dyes are used to impart vibrant, consistent colours throughout the part.
- Chemical Treatment : Chemical treatments can make a 3D print look better and last longer. Vapour smoothing, especially for ABS plastic, uses solvent vapours like acetone to melt the outer layer and make it smooth.
- Heat Treatment : Heat treatments change the internal structure of a 3D print to make it stronger. Annealing heats the print to relieve stress and improve strength. In metal printing, sintering heats the part just below melting to bond the particles together more strongly.
- Infiltration : Infiltration makes a 3D print stronger and smoother. Resin infiltration involves filling porous prints with resin to improve strength and appearance. In metal printing, metal infiltration fills the part with another metal, like bronze, to make it more robust.
3D printing software :
Selecting best software for 3D printing
Selecting the right software for 3D printing is crucial for achieving high-quality results. The software ecosystem for 3D printing typically includes three main types: modelling software, slicing software(Cura ,Simplify3D, etc.), and printer control software(Tinkercad , Cura , etc.) .
Surface Modeling Software for 3D Printing
Surface modelling software is ideal for creating complex, organic shapes and intricate designs with smooth surfaces. Blender is a highly recommended option in this category. It’s an open-source software that provides extensive tools for detailed surface modelling, making it perfect for artistic projects. Rhinoceros (Rhino) is another excellent choice, offering precise control over surfaces and curves, commonly used in industrial design and jewellery. Both these tools excel in handling freeform designs.
Solid Modelling Software for 3D Printing
Solid modelling software focuses on creating precise, mathematically-defined geometric shapes, making it ideal for engineering and mechanical parts. Fusion 360 by Autodesk stands out in this category, providing robust CAD/CAM capabilities, including parametric modelling, which is essential for functional prototypes and detailed mechanical components. These programs (Fusion 360 , Solidworks , etc.) allow users to create highly accurate and functional parts, ensuring the final 3D printed object meets specific performance requirements.
Safety Precautions in 3D printing
Health Precautions
3D printing, also known as additive manufacturing, has revolutionised the way objects are designed and produced, but it comes with significant safety risks.
When using a 3D printer, safety is very important because of the high temperatures, moving parts, and potentially harmful fumes. Make sure your printing area is well-ventilated to avoid breathing in dangerous particles.
Keep in mind that the printer's parts, especially the print head and heated bed, get very hot, so avoid touching them to prevent burns.
Always wear safety glasses to protect your eyes, and gloves when handling chemicals like solvents or resin to protect your skin.
Have a fire extinguisher nearby, never leave the printer running unattended, and place it on a stable, non-flammable surface.
Regularly check the printer's wiring to ensure it's not damaged, store materials like filaments and resins in a cool, dry place, and dispose of waste properly.
Keep your hands away from moving parts to avoid injury, and use ear protection if the printer is noisy.
Make sure the printer’s software is up-to-date to avoid bugs that could cause unsafe behaviour, and always read the manual to understand the risks and follow recommended safety guidelines.
Legal Consideration while 3D printing :
Key Regulations That Could Impact 3D printing
Using designs that are protected by patents, copyrights, or trademarks without permission is illegal. Always check if a design is protected and obtain the necessary permissions to use, modify, or distribute it.
If you sell 3D printed products, you could be held responsible if the product causes harm. Ensure that your products meet safety standards and regulations to avoid liability issues.
Ensure that 3D printed objects are safe and do not pose risks to users. Avoid creating items that could cause harm, such as weapons or hazardous devices.
Consider the environmental impact of the materials you use. Strive to use sustainable, biodegradable, or recyclable materials to minimise environmental harm.Use eco-friendly materials and manage waste responsibly to reduce the negative impact on the environment.
Application of 3D printing
Aerospace Industry
The aerospace industry spends a lot of money on designing and testing new concepts and ideas. Since, the parts used in aeroplanes and rockets require a lot of effort and time to be manufactured. This is mainly because it involves making and testing of the large and complicated parts.
Nowadays , 3D printing has affected the aerospace industry in a huge manner. This is because of its ability to create lighter and stronger parts.Aerospace manufacturers use 3D printing to produce functional parts quickly, experiment with new materials, and consolidate multiple parts into single components, enhancing performance and energy efficiency. Additionally, 3D printing supports the development of custom tooling fixtures and low-volume production, making it a versatile tool for both commercial and military aerospace applications .

Industrial Prototyping
3D printing, also known as additive manufacturing, is a technology that has been rapidly advancing in recent years. One of the most exciting applications of this technology is in the field of industrial prototyping. This is the process of creating a physical model of a product or design, which can be used to test and evaluate its design, function, and performance.
3D printing has revolutionised the way industrial prototypes are created, as it allows for rapid prototyping and the ability to create complex, intricate designs that would be difficult or impossible to produce using traditional manufacturing methods.

Consumer Electronics
3D printing is transforming the consumer electronics industry by enabling rapid prototyping, customization, and efficient production of components and accessories. This technology allows manufacturers to quickly bring innovations to market, meeting the high demand for new models and features at competitive prices . Major brands like Apple, Samsung, and Sony utilise 3D printing for developing prototypes, custom cases, and even circuit boards, which can be produced faster and more cost-effectively than traditional methods.

Medical Health
3D printing in the medical field has revolutionised patient care by enabling the creation of customised medical devices, implants, and prosthetics tailored to individual anatomies. This technology allows for the production of patient-specific surgical models, which enhance preoperative planning and surgical precision, ultimately improving patient outcomes and reducing operating times. Additionally, 3D printing facilitates the rapid prototyping of new medical devices, accelerating the development and testing of innovative treatments . For instance, 3D-printed prosthetics can be designed to match the exact anatomy of a patient, providing a better fit and greater comfort.

Automotive 3D printing
One of the key advantages of 3D printing in the automobile industry is the ability to quickly and easily create complex, customized parts. For example, a car manufacturer can use 3D printing to create a prototype part that is designed to fit a specific make and model of car. This not only speeds up the design process, but also allows for greater flexibility in the final product. Additionally, 3D printing can be used to create tooling, such as molds and jigs, which can be used in the manufacturing process.

Another advantage of 3D printing in the automobile industry is the ability to reduce costs. Traditional manufacturing methods, such as injection moulding, can be expensive and time-consuming. With 3D printing, manufacturers can create parts and tooling in a fraction of the time and at a fraction of the cost. This not only saves money but also allows for greater experimentation and innovation in the design process.
3D printing Jewellery
3D printing in the jewellery industry is revolutionising the way jewellery is designed and produced. By using 3D printing technology, jewellery designers and manufacturers can create complex and intricate designs with ease, bringing their creative visions to life. 3D printing also allows for greater customization and personalization of jewellery pieces. Additionally, it can reduce production costs and lead time, allowing for more efficient and cost-effective production. This technology also enables more sustainable practices by reducing waste and the need for certain types of mining. Overall, 3D printing in the jewellery industry is opening up new possibilities for design and production, making it an exciting and innovative field to be a part of.

Benefits of 3D printing
-
Time :
Conventional manufacturing methods use crude and subtractive
manufacturing techniques to develop a design into a part
that has to be used, probably taking weeks from ordering to
being able to be put into use.
But with 3D printing you get :
- quick manufacturing which takes just hours to do
- no time wasted in transporting
- no time wasted in quality control
- no time wasted replacing parts too
-
Materials :
Another advantage of using this method of Additive
manufacturing .
- A wide variety of products containing different materials can be easily produced .
- different coloured materials can be used to produce 1 product
- Metal components can be printed too
To put it into perspective , a complete car can be 3D printed , that's how cool this tech is ,trust me it just gets cooler trying to imagine the kind of materials you could have 3D printed .
-
Single Step Manufacturing :
When compared to conventional methods of manufacturing which
normally consists of many steps of processes, it is very
advantageous that Additive manufacturing , practically
involves only a single step of Manufacturing process to get
the desired component ready .
In most cases the components that are 3D printed can be directly used for the desired applications without any post processing .
-
Risk Mitigation : Every component that is
manufactured using 3D printing is completely accurate and
precise in terms of dimensions and tolerances , the need to
unnecessarily test and verify the accuracy of the
manufactured component is reduced and hence a lot of
production / testing time is reduced.
This advantage is definitely something you will not find in traditional manufacturing techniques.
-
Customisation : The biggest boon that we have
with additive manufacturing is that customised designs based
on personal choices and demands can be meet.
For example : Prosthetic limbs for specially abled individuals can be made , taking into consideration their body structure and different material combinations for light weight super strong and long lasting components.

- Material Limitations : Limited range of materials compared to traditional manufacturing.
- Surface Finish : requires post-processing to achieve a smooth surface finish.
- Size constraints : Limited by the build volume of the 3D printer.
- Strength and Durability : Layer adhesion and unbalanced curing issues can lead to weaker parts.
- Cost : High initial investment for quality 3D printers and materials.
- Environmental Impact : Some 3D printing materials are not recyclable.
The future of 3D printing holds promise as it continues to evolve and integrate into various industries, transforming manufacturing processes and product customization.
How mature is the technology, and what barriers need to be overcome for widespread adoption?
The hype around 3D printing has indeed evolved over the years, transitioning from initial excitement to a more grounded perspective on its capabilities and limitations. Initially hailed as a technology that would revolutionise manufacturing and consumer markets overnight, the reality has shown a more gradual integration into various industries. While the sensationalism may have subsided, interest and investment in 3D printing persist, driven by ongoing advancements in materials, software, and applications. "The initial hype created unrealistic expectations, but the technology's potential remains significant," comments industry analyst Sarah Lee. As the technology matures and finds practical niches in fields like aerospace, healthcare, and customised consumer products, its impact continues to grow steadily, albeit with a more realistic understanding of its strengths and challenges.
Despite advancements, challenges remain in material diversity, speed, and cost-effectiveness.
Step by step guidelines for 3D printing
Should you buy a 3D printer or use a 3D printing service?
Factors to consider | Using a Personal 3D Printer | Using Online 3D Printing Services |
---|---|---|
Initial Cost | High capital expenditure | No capital expenditure: pay per print |
Versatility | Limited range of materials and technologies | Wide range of materials and technologies are available |
Quality | Decent output using desktop printers (provided printers are maintained) | High quality output, along with inspection reports (if required) |
Material Handling | Requires storage and management of materials | Handled by the service provider |
Batch Production | Takes a lot of time and linear to quantity | Parallel processing makes it ideal for batch production |
Lead Time | Immediate (Print Time) | Delayed (shipping + Print time) |
Customization | Low (Limited to the printer type) | High (multiple printing technologies are available) |
Maintenance | User responsible for maintenance and repairs | No maintenance required by the user |
Cost per Unit | Low for small quantities, not feasible for large quantities. | Economical for large quantities, high for small quantities |
Space Requirement | Requires dedicated space for printer and materials | No space required by the user |
Steps to use 3D printing services
The steps for utilizing 3D printing services in our company, iamrapid.com, typically involve several key stages to ensure a smooth and efficient process.
- First, create or obtain a 3D model using CAD software, ensuring the design meets the required specifications and is free of errors.
- Next, generate an STL file from the model, which contains the necessary surface geometry.
- Now , Upload this file in our instant quotation system provided by us in our website iamrapid.com . You will get instant quotes related to material , cost , colour , printing process etc.
- You can also contact our sales representatives if you cannot get sufficient information from our quotation system. Also, please provide feedback on our Instant Quotation system .