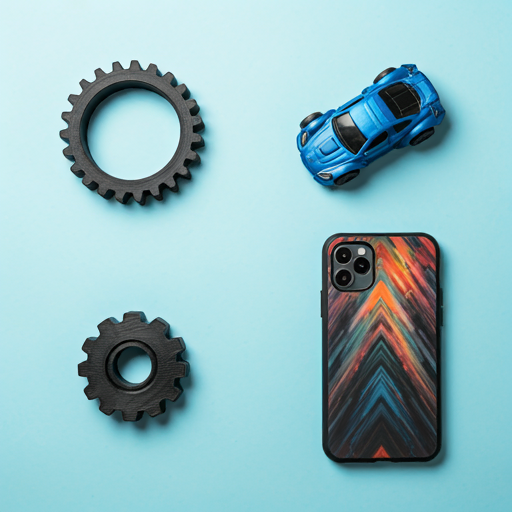
Introduction
Overview of Additive Manufacturing and Post-Processing
Additive manufacturing, also known as 3D Printing, has not just revolutionized but transformed the manufacturing industry. It has the unique ability to swiftly create complex geometries and customized parts. However, the journey from a digital model to a finished product doesn't end with the printing process. Post-processing, a critical step, further enhances the quality, functionality, and aesthetics of 3D printed parts. It involves a range of techniques tailored to different materials and printing technologies, such as support removal, surface smoothing, and part preparation for their intended applications.
Importance of Post-Processing in 3D Printing
Post-processing is not just an option, but often a necessary and one of the final steps required to achieve a customer-ready part. It plays a crucial role in addressing the following key aspects:
- Support Removal is essential for technologies like Fused Deposition Modeling (FDM) and Stereolithography (SLA), which require support structures to maintain the integrity of the build during Printing.
- Surface Finishing is necessary to improve the surface quality of printed parts, making them suitable for end-use applications. Techniques like sanding, bead blasting, and chemical smoothing are commonly used.
- Functional Enhancements Processes such as heat treatment and coating can enhance parts' mechanical properties and durability.
- Aesthetic Improvements Painting, dyeing, and plating can improve the visual appeal of printed parts, making them suitable for consumer products and display models.
Post-processing is crucial because each print technology, material, and intended final use dictate specific steps to achieve the desired part quality.
Types of Additive Manufacturing Processes
Let's quickly understand the different additive manufacturing processes before we delve into their specific post-processing requirements.
Fused Deposition Modeling (FDM)
FDM is one of the most widely used 3D printing technologies, known for its affordability and versatility. It involves extruding thermoplastic filaments layer by layer to build parts.
Stereolithography (SLA)
SLA uses a laser to cure liquid resin into solid parts, offering high precision and smooth surface finishes. It is ideal for detailed prototypes and intricate designs.
Selective Laser Sintering (SLS)
SLS employs a laser to sinter powdered material, typically nylon, into solid parts. It is known for producing durable and functional prototypes without the need for support structures.
Digital Light Processing (DLP)
DLP is similar to SLA but uses a digital light projector to cure resin. It offers high-speed Printing and excellent resolution, making it suitable for detailed and small parts.
Multi Jet Fusion (MJF)
MJF uses a combination of inkjet printing and powder sintering to create parts with fine details and smooth surfaces. It is known for its speed and ability to produce functional prototypes.
Direct Metal Laser Sintering (DMLS)
DMLS is a metal 3D printing technology that uses a laser to sinter metal powder into solid parts. It is ideal for producing complex metal components with high strength and precision.
Post-Processing Techniques
Post-Processing Techniques for FDM
Support Removal

- Manual Removal: Supports can be removed using pliers, cutters, or knives. Care must be taken to avoid damaging the part.
- Soluble Supports: For dual-extruder printers, supports made from soluble materials can be dissolved in a suitable solvent (e.g., water for PVA). read more about soluble supports in our support structures article here.
Surface Finishing

- Sanding: Sanding is a standard method to smooth the surface of FDM prints. Start with coarse-grit sandpaper and gradually move to finer grits for a polished finish.
- Chemical Smoothing: Acetone vapor smoothing is a popular technique for ABS prints. Exposing the part to acetone vapor melts the outer layer, resulting in a glossy finish.
Painting and Coating

- Priming and Painting: Painting FDM parts can enhance their appearance and provide additional protection. To ensure better adhesion, use a primer before applying paint. Use multiple coats for an even finish.
- Epoxy Coating: Coating FDM parts with Epoxy provides a durable and smooth surface.
Heat Treatment

- Annealing: Heat treatment can improve the mechanical properties of FDM parts. Annealing involves heating the part to a specific temperature and cooling it slowly to relieve internal stresses.
Post-Processing Techniques for SLA
Resin Removal

- Isopropyl Alcohol (IPA) Bath: After Printing, SLA parts need to be cleaned to remove excess resin. This can be done using isopropyl alcohol (IPA) and a soft brush to wash away all uncured resin. Ultrasonic cleaning can enhance the process.
UV Curing

- UV Light Chamber: SLA parts require additional UV curing to harden fully. To achieve optimal strength and stability, place the part in a UV curing chamber or under a UV lamp for the recommended time.
- Sunlight: As an alternative, parts can be exposed to direct sunlight for extended periods, though this method is less controlled.
Sanding and Polishing

- Initial Sanding: Sanding SLA parts can remove layer lines and improve surface smoothness. Start with coarse-grit sandpaper and progress to finer grits. Wet sanding can reduce dust and improve results.
- Polishing Compounds: Polishing compounds achieve a glossy finish on SLA parts. Apply the compound with a soft cloth or buffing wheel.
Painting and Coating

- Priming: Apply a primer to ensure the paint adheres to the resin surface.
- Acrylic Paints: Acrylic paints are flexible and durable. Clear coatings can be applied for added protection and shine.
Post-Processing Techniques for SLS
Powder Removal

- Compressed Air: After Printing, SLS parts are covered in unsintered powder. Use compressed air, brushes, or specialized equipment to remove the excess powder from the part's surface.
- Vacuuming: Use vacuum systems to remove residual powder from the part's surface, paying attention to internal cavities.
Surface Smoothing

- Bead Blasting: Bead blasting involves using a high-pressure stream of abrasive media to smooth the surface of SLS parts. It can remove roughness and improve the overall finish.
- Tumbling: Tumbling is a process where parts are placed in a tumbler with abrasive media. The tumbling action smooths the surface and can also add a polished look.
Dyeing and Painting

SLS parts can be dyed to achieve different colors. Dyeing involves immersing the part in a dye solution that penetrates the porous surface. Painting can be done similarly to FDM, with appropriate primers and paints.
Post-Processing Techniques for DLP
Resin Removal
- IPA Washing: Similar to SLA, DLP parts must be cleaned to remove excess resin. Use isopropyl alcohol (IPA) and a soft brush to ensure all uncured resin is washed away. Ultrasonic cleaning can also help remove stubborn resin residues.
UV Curing
- UV Light Chamber: DLP parts require additional UV curing to harden fully. To achieve optimal strength and stability, place the part in a UV curing chamber or under a UV lamp for the recommended time.
Surface Finishing
- Sanding: Sanding DLP parts can remove layer lines and improve surface smoothness. Start with coarse-grit sandpaper and progress to finer grits. Wet sanding can help reduce dust and achieve a finer surface.
- Polishing: Polishing compounds can achieve a glossy finish on DLP parts. Apply the compound with a soft cloth or buffing wheel.
Post-Processing Techniques for MJF
Powder Removal
- Compressed Air: After Printing, MJF parts are covered in unsintered powder. Use compressed air, brushes, or specialized equipment to remove the excess powder from the part's surface.
UV Curing
- Vacuuming: Employ vacuum systems to thoroughly clean parts, ensuring no residual powder affects the finish or function.
Surface Smoothing
- Bead Blasting: Bead blasting involves using a high-pressure stream of abrasive media to smooth the surface of MJF parts. It can remove roughness and improve the overall finish.
- Tumbling: Tumbling is a process where parts are placed in a tumbler with abrasive media. The tumbling action smooths the surface and can also add a polished look.
Surface Smoothing
MJF parts can be dyed to achieve different colors. Dyeing involves immersing the part in a dye solution that penetrates the porous surface. Painting can be done similarly to FDM, with appropriate primers and paints.
Post-Processing Techniques for DMLS
Support Removal
- Cutting Tools: DMLS parts often require support structures to ensure stability during Printing. These supports can be removed using pliers, cutters, or even CNC machines for precise removal.
- Grinding: Grinding tools can remove remnants without damaging the surface for finer support structures.
Heat Treatment
- Stress Relieving: Heat treatment can improve the mechanical properties of DMLS parts. Processes like annealing and stress relieving involve heating the part to a specific temperature and cooling it slowly to relieve internal stresses.
Surface Finishing
- Machining: Machining processes like milling and turning can achieve precise dimensions and smooth surfaces on DMLS parts.
- Polishing: Polishing can enhance the surface finish of DMLS parts, making them suitable for applications requiring high aesthetics. look.
Coating and Plating
Coating and plating can add functional and aesthetic properties to DMLS parts. Techniques like electroplating and anodizing can improve corrosion resistance and appearance.
Advanced Post-Processing Techniques
Electroplating

- Preparation: Electroplating involves depositing a thin layer of metal onto the surface of a 3D-printed part. This can enhance the part's appearance, conductivity, and corrosion resistance. Ensure the part is clean and smooth before electroplating for better adhesion.
- Process: The part is submerged in an electrolytic bath with the plating metal, and an electric current deposits the metal onto its surface.
Anodizing

- Preparation: Anodizing is an electrochemical process that creates a protective oxide layer on the surface of metal parts. Clean and prepare aluminum parts for anodizing.
- Anodizing Bath: Submerge the part in an acid electrolyte bath and pass an electric current to create the oxide layer. This can improve corrosion resistance and allow for dyeing in various colors.
Vapor Smoothing

- Process: Vapor smoothing involves exposing the part to a solvent vapor, which melts the outer layer and results in a smooth, glossy finish. This technique is commonly used for FDM and SLS parts.
- Safety: Conduct this process in a well-ventilated area or fume hood to avoid inhaling toxic fumes.
CNC Machining

- Precision: CNC machining can accurately post-process 3D-printed parts. It can achieve tight tolerances and smooth surfaces, making it suitable for high-precision applications.
- Techniques: Milling, turning, and drilling are used to refine parts to the desired specifications.
Factors Influencing Post-Processing Choices
- Material Type: Different materials require different post-processing techniques. For example, thermoplastics may benefit from sanding and chemical smoothing, while metals may require machining and heat treatment.
- Part Design: The complexity and geometry of the part can influence the choice of post-processing methods. Intricate designs may require more delicate techniques to avoid damaging fine details.
- Intended Application: The part's intended use can dictate the necessary post-processing steps. Functional prototypes may need enhanced mechanical properties, while aesthetic models require a high-quality finish.
- Cost and Time Considerations: Post-processing can add to the overall cost and time of production. Balancing the desired quality with budget and time constraints is crucial for efficient manufacturing.
Best Practices for Post-Processing
- Safety Measures: Always follow safety guidelines when performing post-processing tasks. Wear appropriate personal protective equipment (PPE) and work in well-ventilated areas to avoid exposure to harmful chemicals and dust.
- Quality Control: Implement quality control measures to ensure consistent results. Regularly inspect parts during and after post-processing to identify and address any defects or issues.
- Cost Management: Optimize post-processing workflows to minimize costs. This can include using automated equipment, selecting cost-effective materials, and reducing waste.
Future Trends in Post-Processing for Additive Manufacturing
Automated Post-Processing Techniques in Additive Manufacturing
Automated post-processing in additive manufacturing integrates hardware, software, and chemistry to streamline and enhance the finishing of 3D-printed parts. This approach addresses the limitations of traditional manual methods, such as inconsistency, high labor costs, and time consumption, by providing reliable, repeatable, and efficient solutions.
Why Automated Post-Processing?
Automated post-processing solutions are designed to overcome the challenges associated with traditional methods. These challenges include:
- Time-consuming manual labor: Manual post-processing is labor-intensive and does not scale well with increased production volumes.
- Inconsistent results: Manual methods often lead to variability in the quality of finished parts, which can be problematic for customer-ready products.
- High breakage rates: Handling parts manually increases the risk of damage and breakage.
- High costs: The labor and time required for manual post-processing can significantly increase production costs.
Automated systems offer a comprehensive solution by integrating proprietary software, hardware, and consumables to deliver consistent, high-quality results with faster throughput and a better return on investment (ROI).
Key Automated Post-Processing Techniques
1. Support Removal
- Submersible Systems: These systems use a combination of water and proprietary detergents to dissolve and remove support materials from 3D-printed parts. They are effective for technologies like FDM, SLA, and PolyJet.
- Spray Platforms: High-pressure water jets or chemical sprays remove supports, reducing cycle times and increasing productivity.
2. Surface Finishing
- Vibratory Systems: These systems use vibratory motion combined with abrasive media to smooth the surface of parts. They can be configured to achieve specific surface roughness (Ra) values while maintaining fine-feature details.
- Circular Systems: Similar to vibratory systems, these use circular motion to achieve fast and consistent surface finishing results.
3. Hybrid Systems
- Multi-Function Systems: These systems combine support removal and surface finishing in one compact unit. They use advanced software to control agitation algorithms, ensuring consistent and repeatable results even for complex geometries.
4. Automated Cleaning and De-Powdering
- De-Powdering Systems: These systems use targeted vibrations and automated rotation to remove excess powder from parts printed using powder bed technologies like SLS and DMLS. They ensure thorough cleaning and allow for the reuse of metal powder.
Examples of Automated Systems
1. PostProcess Technologies
DECI Duo: Multifunctional system for automated support removal and surface finishing, optimizing post-processing of various 3D printed materials.
2. DyeMansion
Powerfuse S: Vapor smoothing system for industrial FDM and SLS parts, providing a sealed, injection-molding-like finish.
3. Grenzebach and EOS Collaboration
EOS Shared Modules Concept: Automates unpacking, de-powdering, and setup for parts printed using EOS systems, reducing manual interventions and increasing productivity.
4. Solukon
SFM-AT200: Entry-level de-powdering solution for laser-fused metal parts, suitable for medical and laboratory applications.
5. 3D Nextech
3DFinisher: Provides professional and automated surface finishing for ABS, ASA, and cellulose acetate parts, improving mechanical properties and aesthetics of FFF 3D-printed parts.
Conclusion
In this guide, we have explored the critical role of post-processing in the additive manufacturing workflow, focusing on its significance in enhancing the quality, functionality, and aesthetics of 3D-printed parts. Key points discussed include:
- Essential Processes: Post-processing encompasses vital steps such as support removal, surface finishing, and specialized treatments tailored to different printing technologies and materials.
- Quality Assurance: Effective post-processing techniques ensure that 3D-printed parts meet the requirements for various applications, from prototypes to end-use products.
- Technological Advancements: The field continues to evolve with advancements in automation and the development of new materials, promising improved efficiency and superior outcomes in post-processing.
Final Thoughts on Enhancing 3D Printing Quality Through Post-Processing
Investing in effective post-processing techniques is paramount for achieving superior results in additive manufacturing. By meticulously applying these techniques, manufacturers refine their products' physical properties and elevate their functional and aesthetic characteristics. Integrating automated processes and innovative materials will further optimize post-processing efficiency as technology advances, paving the way for enhanced capabilities and broader application possibilities in 3D Printing.
This comprehensive approach underscores the transformative potential of post-processing in realizing the full benefits of additive manufacturing, ensuring that each printed part meets the highest quality and performance standards.
Want your 3D printed models to be of utmost quality? We are here to help. At iamrapid.com, you get a seamless service experience with our advanced automated quotation system, which gives you the quotation within seconds after you upload your 3D model on our platform. This is followed by our express manufacturing services, which includes all the necessary post- processing work so that you are satisfied with your 3D-printed models with exceptional quality.
Visit iamrapid.com today and get your models 3D printed with just a few simple clicks.