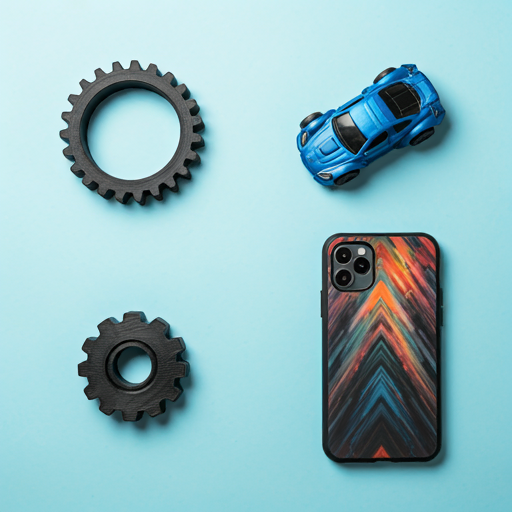
Introduction
Welcome to "Design for Additive Manufacturing," an extensive guide from iamrapid.com, your trusted 3D printing service provider based in Bangalore, India. This guide will delve into the intricacies of designing specifically for additive manufacturing (AM). This transformative approach allows for creating complex geometries, optimized structures, and customized solutions like never before.
Additive manufacturing, also known as 3D printing, is reshaping the way products are conceptualized, designed, and manufactured. Its potential is not limited to rapid prototyping, but extends to full-scale production, making it a game-changer in industries such as aerospace, healthcare, automotive, and consumer goods. To fully exploit the capabilities of this technology, it's essential to grasp the principles and best practices for design that can harness the unique benefits of AM.
Embark on a journey with us as we delve into the crucial considerations, techniques, and tips for designing parts that are not just manufacturable, but also optimized for performance, cost, and innovation. Whether you're a seasoned engineer, a product designer, or an eager enthusiast, this guide is your key to mastering the evolving landscape of additive manufacturing.
Let's unlock the potential of your designs and bring your ideas to life with the power of 3D printing!
What is Additive Manufacturing ?
Additive manufacturing, commonly known as 3D printing, creates objects by adding material layer by layer directly from digital models. Unlike traditional subtractive manufacturing methods that remove material to shape a part, additive manufacturing builds parts with precision and minimal waste. This innovative approach allows for producing complex geometries and customized solutions that were previously unattainable. To understand this further,click here.
Importance of Design in Additive Manufacturing
Design is the cornerstone of successful additive manufacturing (AM), dictating not only the feasibility and functionality of the final product but also its efficiency, cost, and environmental impact. Understanding and leveraging the principles of AM-specific design can significantly enhance the advantages offered by this transformative technology. Below, we explore the various aspects that underscore the critical importance of design in additive manufacturing.
-
Optimizing for Complex Geometries:
AM excels in creating complex geometries that traditional manufacturing methods cannot quickly achieve. Engineers and Designers can develop intricate structures by designing with AM in mind, such as lattice frameworks, organic shapes, and internal channels. These designs improve product performance by enhancing strength-to-weight ratios and integrating multiple functions into a single part.
-
Enhancing Material Efficiency and Sustainability:
Additive manufacturing builds objects layer by layer, allowing for precise material placement and minimal waste. This contrasts sharply with subtractive manufacturing, which often generates significant material waste.Designing parts specifically for AM promotes efficient material use, contributing to sustainability and reducing the overall environmental footprint of manufacturing processes.
-
Facilitating Customization and Personalization:
AM's design flexibility enables the production of customized and personalized products without extensive retooling. This capability is particularly valuable in healthcare, where tailored implants and prosthetics can significantly improve patient outcomes. This flexibility also benefits consumer goods, allowing for personalized designs catering to individual preferences.
-
Reducing Time to Market:
Designing for AM can accelerate the product development cycle. Rapid prototyping allows designers to create quickly and test product iterations, refining designs based on real-time feedback. This process reduces development time and speeds up the transition from concept to market-ready product, giving companies a competitive edge in responding to market demands.
-
Achieving Cost-Effectiveness:
While the initial setup for AM can be expensive, the long-term benefits often outweigh these costs. Optimizing designs for AM can reduce the number of parts, streamline assembly processes, and minimize inventory costs. Additionally, on-demand production eliminates the need for extensive inventories, leading to further cost savings in storage and logistics.
-
Driving Enhanced Performance and Innovation:
Designing for AM encourages innovation by allowing engineers/designers to explore new structures and materials. This can lead to high-performance components with superior mechanical properties, thermal resistance, or other desired characteristics. The ability to experiment and iterate on designs fosters continuous improvement and technological advancement.
-
Overcoming Traditional Manufacturing Constraints:
Traditional manufacturing methods impose various design constraints due to tooling, machining, and fabrication limitations. AM frees designers from these constraints, enabling greater creative freedom. This allows for exploring unconventional designs that offer superior performance, aesthetics, and functionality, leading to more innovative products.
-
Integrating Multifunctional Components:
AM allows for creating multifunctional components that combine several parts into one, reducing the need for assembly and improving overall reliability. Manufacturers can produce more compact and efficient products by designing parts with integrated functions. This integration is particularly advantageous in industries like aerospace and automotive, where space and weight savings are critical.
-
Supporting Distributed Manufacturing:
Designing for AM supports distributed manufacturing, where production can be decentralized and localized. This approach reduces transportation costs, lowers carbon footprints, and enables on-demand production closer to the end user. Distributed manufacturing enhances supply chain resilience and responsiveness, particularly during disruption.
-
Promoting Continuous Improvement and Iteration:
The iterative nature of AM aligns well with continuous improvement methodologies. Designers can rapidly prototype, test, and refine products based on real-world feedback, leading to ongoing enhancements. This iterative process fosters innovation and quality improvement, ensuring products remain competitive and meet evolving customer needs.
By understanding and applying AM-specific design principles, companies can fully harness the potential of additive manufacturing, driving advancements across various industries and shaping the future of production. As you continue to explore and implement AM, thoughtful design will be your key to unlocking its vast possibilities.
Understanding Additive Manufacturing
Types of Additive Manufacturing Processes in Brief
3D printing technologies, also commonly known as additive manufacturing (Are 3D Printing and Additive Manufacturing the same? Click here to know), encompass a variety of processes that create objects layer by layer from digital models. Here is a brief overview of the most common 3D printing technologies:
-
Fused Deposition Modeling (FDM)
FDM, also known as Fused Filament Fabrication (FFF), is one of the most widely used 3D printing technologies. It works by extruding thermoplastic filament through a heated nozzle, layer by layer, to build up the desired object. FDM is popular for its affordability, ease of use, and versatility, making it ideal for prototyping and hobbyist projects. Click here to learn more in-depth about FDM.
-
Stereolithography (SLA)
SLA uses a laser to cure liquid resin into hardened plastic in a process called photopolymerization. This technology is known for producing high-resolution, highly detailed parts with smooth surface finishes. SLA is widely used in industries requiring precision, such as jewelry, dental, and medical device manufacturing. Click here to learn more about SLA.
-
Selective Laser Sintering (SLS)
SLS utilizes a high-powered laser to fuse small particles of polymer powder into a solid structure. Each layer of powder is spread across the build platform and selectively sintered by the laser. SLS is valued for its ability to produce durable, complex geometries without supporting structures, making it suitable for functional prototypes and end-use parts. Click here to learn more about SLS.
-
Digital Light Processing (DLP)
Similar to SLA, DLP uses light to cure resin, but it differs in that it uses a digital projector screen to flash each layer simultaneously rather than tracing it with a laser. This results in faster print times compared to SLA. DLP is known for high speed and accuracy, making it ideal for detailed models and small parts. Click here to learn more in-depth about DLP.
-
Binder Jetting
Binder jetting involves laying down a layer of powder and then selectively depositing a liquid binder to glue the particles together. This process is repeated layer by layer to build the object. Binder jetting can use various materials, including metals, ceramics, and sand, and is often used for full-color prototypes and metal casting molds. Click here to learn more about Binder Jetting.
-
Direct Metal Laser Sintering (DMLS) / Selective Laser Melting (SLM)
DMLS and SLM are similar technologies that create metal parts by sintering or melting metal powder with a laser. DMLS typically operates at lower temperatures and doesn't fully melt the powder. In contrast, SLM fully melts the powder to form solid metal parts. Both are used for producing robust and complex metal components in the aerospace, automotive, and medical industries. Click here to learn more about DMLS/SLM.
-
Multi Jet Fusion (MJF)
Developed by HP, MJF uses an inkjet array to selectively apply fusing agents to a bed of nylon powder, which is then fused by heating elements. This technology allows for the rapid production of highly detailed and durable parts and is particularly effective for functional prototypes and low-volume production runs. Click here to learn more about MJF.
Materials Used in Additive Manufacturing
In DfAM, having prior knowledge about the materials, their properties, and their applications can significantly enhance the design process. This understanding allows for creating more optimal, manufacturable designs, ensuring that the chosen material aligns with the final product's intended use and performance requirements. By integrating material knowledge early in the design phase, designers can better leverage the full potential of additive manufacturing technologies.
Below is a brief overview of the primary material categories used in additive manufacturing, highlighting their overall use case scenarios.
1. Plastics
- Thermoplastics: Commonly used in Fused Deposition Modeling (FDM), thermoplastics like ABS, PLA, and PETG are valued for their ease of use, affordability, and versatility. These materials are ideal for prototyping, hobbyist projects, and functional parts.
- High-Performance Plastics:Materials like Nylon, Polycarbonate (PC), and PEEK are used for more demanding applications due to their enhanced mechanical properties, heat resistance, and chemical stability. These are often used in industrial and engineering applications.
2. Metals
- Stainless Steel: Widely used in Direct Metal Laser Sintering (DMLS) and Selective Laser Melting (SLM), stainless steel offers excellent strength, durability, and corrosion resistance. It is used in the aerospace, automotive, and medical industries.
- Titanium: Known for its high strength-to-weight ratio and biocompatibility, titanium is used in medical implants, aerospace components, and high-performance engineering parts.
- Aluminum: Lightweight and strong, aluminum is used in the AM to produce lightweight parts with good mechanical properties, making it ideal for automotive and aerospace applications.
- Other Metals: Known for its high strength-to-weight ratio and biocompatibility, titanium is used in medical implants, aerospace components, and high-performance engineering parts.
3. Resins
- Standard Resins: Used in Stereolithography (SLA) and Digital Light Processing (DLP), standard resins are ideal for creating high-detail prototypes and models. They offer smooth surface finishes and delicate features.
- Engineering Resins: These resins, including rigid, flexible, and high-temperature variants, enhance mechanical properties for functional prototypes and end-use parts. Applications include dental, medical, and industrial components.
- Biocompatible Resins: Specifically designed for medical and dental applications, these resins meet strict regulatory standards for use in products that come into contact with the human body.
4. Composites
- Fiber-Reinforced Composites: Combining polymers with reinforcing fibers like carbon fiber or fiberglass. These materials offer superior strength and stiffness while remaining lightweight. They are used in aerospace, automotive, and sports equipment.
- Metal Matrix Composites (MMCs): TThese composites combine metal powders with ceramic or carbon fibers, enhancing mechanical properties and wear resistance. They are used in high-performance applications where traditional metals may not suffice.
- Ceramic Composites: These materials combine ceramic powders with polymers or other binders to create parts with high heat resistance and mechanical strength. Applications include aerospace components and high-temperature industrial parts.
Design Principles for Additive Manufacturing
Additive manufacturing (AM) offers unique opportunities for creating complex, customized, and highly functional products. However, designers must understand and apply specific principles tailored to AM to fully leverage these benefits. The following sections outline fundamental design principles for additive manufacturing, focusing on Design for Manufacturability (DFM), Design for Assembly (DFA), Design for Functionality, and Design for Cost Efficiency.
Design for Manufacturability (DFM)

Design for Manufacturability (DFM) involves optimizing a product design to ensure it can be manufactured quickly and efficiently. In the context of AM, DFM principles help maximize the advantages of additive processes while minimizing potential challenges.
- Part Orientation: The orientation of a part during printing affects its strength, surface finish, and print time. Optimal part orientation can improve mechanical properties, reduce the need for supports, and enhance surface quality. Designers should consider the orientation to balance these factors effectively.
- Layer Thickness: The layer thickness in AM influences the resolution, surface finish, and build time. Thinner layers produce finer details and smoother surfaces but increase print time. Designers must choose an appropriate layer thickness based on the required detail and efficiency.
- Support Structures: While AM can create overhangs and intricate features, these often require support structures. Minimizing the need for supports through strategic part orientation and design can reduce post-processing efforts, material waste, and overall print time.
- Surface Finish: The surface finish of AM parts can vary depending on the process and material used. Designers should account for the required surface finish in their designs, considering post-processing steps like sanding, polishing, or coating to achieve the desired result.
- Tolerances and Accuracy: AM processes can produce parts with varying degrees of precision. Designers must understand the specific tolerances of the chosen AM technology to ensure the proper fit and function of assembled components. This involves designing parts with adequate tolerances for their intended applications.
- Post-Processing Requirements: Post-processing can include removing supports, surface finishing, and other treatments to achieve the final part specifications. Designing parts to minimize post-processing can save time and costs, making manufacturing more efficient.
Design for Assembly (DFA)

Design for Assembly (DFA) focuses on simplifying the assembly process of a product. With AM, many traditional assembly constraints can be bypassed, allowing for more integrated and streamlined designs.
- Part Consolidation: The orientation of a part during printing affects its strength, surface finish, and print time. Optimal part orientation can improve mechanical properties, reduce the need for supports, and enhance surface quality. Designers should consider the orientation to balance these factors effectively.
- Snap-Fit and Interlocking Features: The layer thickness in AM influences the resolution, surface finish, and build time. Thinner layers produce finer details and smoother surfaces but increase print time. Designers must choose an appropriate layer thickness based on the required detail and efficiency.
- Modular Design: While AM can create overhangs and intricate features, these often require support structures. Minimizing the need for supports through strategic part orientation and design can reduce post-processing efforts, material waste, and overall print time.
- Ease of Handling: The surface finish of AM parts can vary depending on the process and material used. Designers should account for the required surface finish in their designs, considering post-processing steps like sanding, polishing, or coating to achieve the desired result.
Design for Functionality

Design for Functionality ensures that the product meets its intended purpose and performs reliably under the specified conditions. AM allows designers to incorporate unique functional features directly into the parts.
- Customization and Personalization: AM excels at producing customized and personalized parts without additional cost. Designers can create tailored solutions for individual users or specific applications, such as medical implants, consumer products, and bespoke components.
- Integration of Features: Functional features such as hinges, channels for fluid or airflow, and embedded electronics can be directly integrated into the design. This reduces the need for separate components and enhances the product's overall Functionality.
- Material Selection: The choice of material impacts the final product's Functionality. As discussed earlier, Designers must select materials with the necessary mechanical properties, durability, and environmental resistance for the intended application. AM allows for using a wide range of materials, from plastics and metals to composites and ceramics.
- Performance Optimization: By leveraging AM's capabilities, designers can optimize parts for specific performance criteria, such as weight reduction, improved strength, thermal management, and vibration damping. This often involves advanced simulation and testing to refine the design.
Design for Cost Efficiency

Design for Cost Efficiency involves creating designs that minimize production costs while maintaining quality and performance. AM offers several innovative design strategies for achieving cost efficiency.
- Material Efficiency: Designing parts to use material efficiently can significantly reduce costs. This includes minimizing waste through optimized geometries and internal structures and selecting cost-effective materials that meet performance requirements.
- Production Time: Reducing print time is crucial for cost efficiency. Designers can achieve this by optimizing part orientation, reducing the need for supports, and simplifying geometries where possible. Faster production times lead to lower operational costs and higher throughput.
- Post-Processing Minimization: Post-processing can be a significant cost driver in AM. Designing parts that require minimal post-processing, such as support removal, surface finishing, and assembly, can lower overall production costs and accelerate time-to-market.
- Batch Production and Scaling: While AM is often used for low-volume and customized production, it can also be cost-effective for small to medium quantities batch production. Designing parts for efficient batch processing, including nested arrangements and multi-part builds, can maximize the efficiency of the AM process.
Understanding and applying these design principles is essential for fully leveraging additive manufacturing's capabilities. These principles help navigate AM's unique opportunities and challenges, ensuring designs are practical, feasible, and economically viable. Staying informed and adaptive in design strategies is critical to achieving sustained success and innovation in this evolving field.
In addition to the principles mentioned, countless other highly design-specific optimizations exist. These optimizations often rely on the creativity and logical reasoning of the designer. Whether it's finding innovative ways to reduce material usage, improving structural integrity, or enhancing aesthetic appeal, the possibilities for optimization in additive manufacturing are virtually limitless. Designers play a pivotal role in pushing the boundaries of what's possible, continually exploring new techniques, and moving the technology forward. As AM continues to evolve, the collaboration between advanced software tools and human ingenuity will drive unprecedented design and manufacturing innovation levels.
CAD Software for Additive Manufacturing

Additive manufacturing (AM) heavily relies on Computer-Aided Design (CAD) software to translate innovative ideas into tangible prototypes or end-use products. The CAD software you choose depends on what you are designing. For example, Figurines require freedom to design organic curves and surfaces; another example is Spare parts, which require precision modeling with low tolerances. So, choosing the right software that satisfies your design needs is essential, as it impacts the efficiency, precision, and complexity achievable in your additive manufacturing endeavors. Let's explore some popular CAD software tools.
Popular CAD Software Tools
- Autodesk Fusion 360 : Known for its comprehensive cloud-based CAD/CAM/CAE capabilities, Fusion 360 enables seamless collaboration and iteration throughout the design process. Its robust tools for parametric modeling, mesh editing, and generative design make it a go-to choice for additive manufacturing enthusiasts seeking versatility and integration.
- SolidWorks : Renowned as an industry standard for mechanical design, SolidWorks specializes in providing powerful parametric modeling capabilities paired with intuitive user interfaces. Its extensive library of features and add-ons facilitates intricate part design and assembly, making it ideal for additive manufacturing applications requiring precision and complexity.
- Tinkercad : Tinkercad stands out for its user-friendly, browser-based interface, catering to beginners and educators. Its intuitive drag-and-drop tools allow users to quickly create 3D models suitable for additive manufacturing projects, making it an excellent starting point for early enthusiasts and students exploring the world of 3D design.
- Blender : While primarily recognized as a versatile 3D modeling and animation software, Blender's specialty lies in its robust toolset and open-source nature. Its powerful sculpting and mesh editing features enable users to create complex geometries and organic shapes suitable for various designing & AM processes, making it a compelling choice for artists and designers seeking creative freedom.
Let's take a moment to gather ourselves. We've explored the world of additive manufacturing, including its various processes, available materials, essential design principles, and popular CAD software tools. With this understanding, it's time to examine how you can effectively apply this knowledge as a designer/engineer. So, let's delve into the Design for Additive Manufacturing (DfAM) workflow.
Design for Additive Manufacturing: Workflow
Designing for additive manufacturing (DfAM) involves a systematic approach to leveraging additive manufacturing technologies' unique capabilities. This comprehensive workflow encompasses various stages, from conceptualization and ideation to final design adjustments. Let's explore each phase in detail:
Conceptualization and Ideation

-
Define Objectives and Constraints:
-
- Clearly define the project's goals, including functional requirements, performance targets, and regulatory constraints.
- Consider limitations imposed by the chosen additive manufacturing process, such as minimum feature size, build volume, and material compatibility.
-
Generate and Explore Ideas:
-
- Conduct brainstorming sessions, sketching exercises, and idea-generation workshops to explore various design possibilities.
- Encourage cross-disciplinary collaboration and input from stakeholders to ensure diverse perspectives are considered.
-
Concept Development and Selection:
-
- Refine initial concepts based on feasibility, novelty, and alignment with project objectives.
- Evaluate and prioritize concepts using technical feasibility, market demand, and potential impact criteria.
CAD Modeling

-
Create Detailed 3D Models:
-
- Utilize CAD software to develop detailed digital models of the intended product or part, considering geometry, dimensions, tolerances, and material properties.
- Incorporate features such as fillets, chamfers, and draft angles to improve manufacturability and part quality.
-
Optimize Designs for Additive Manufacturing:
-
- Explore design freedom offered by additive manufacturing, including lattice structures, topology optimization, and organic shapes.
- Consider design considerations specific to additive manufacturing processes, such as support structures, build orientation, and layer thickness.
- Leverage parametric modeling techniques to explore design variations and optimize for performance, cost, and time-to-market.
Simulation and Analysis

-
Virtual Testing and Analysis:
-
- Utilize simulation software to predict and evaluate the behavior of designs under various operating conditions.
- Perform structural analysis, thermal simulations, and fluid flow simulations to identify potential performance issues and optimize designs.
-
Evaluate Manufacturability:
-
- Assess the manufacturability of designs by simulating the additive manufacturing process in slicing software, which includes build orientation, support structures, and material deposition.
- Identify potential issues such as warping, residual stresses, and poor surface finish, and iterate on designs to address them.
Design Optimization

-
Iterative Refinement:
-
- Iterate designs based on simulation results, mock-up feedback, and stakeholder input to address identified issues and optimize performance.
- Balance trade-offs between design complexity, part quality, and manufacturing efficiency to achieve the desired outcomes.
-
Utilize Advanced Optimization Techniques:
-
- Leverage topology optimization, generative design, and machine learning algorithms to explore design spaces and identify optimal solutions.
- Consider multi-objective optimization approaches to simultaneously optimize for conflicting objectives such as weight reduction, stiffness, and cost.
-
Validate Design Changes:
-
- Validate design changes through re-simulation and testing to ensure that proposed modifications achieve the desired improvements without introducing new issues.
Prototyping and Testing

-
Select Appropriate Additive Manufacturing Method and Materials:
-
- Choose the most suitable additive manufacturing process based on factors such as part complexity, material properties, surface finish requirements, and production volume. Which additive manufacturing method is right for you? Click here to know.
-
Fabricate Prototypes:
-
- Utilize the selected additive manufacturing method to fabricate physical prototypes with accuracy and fidelity to the digital design.
- Ensure that the manufacturing parameters, like layer thickness, build orientation, and material selection, are optimized to achieve the desired part quality and performance
-
Conduct Rigorous Testing:
-
- Perform comprehensive testing and validation of the prototypes to assess their functional performance, durability, and reliability under real-world conditions.
- Use a combination of mechanical testing, environmental testing, and functional testing to evaluate the prototypes' suitability for their intended application.
Final Design Adjustments

-
Incorporate Feedback and Lessons Learned:
-
- Incorporate feedback from prototyping, testing, and stakeholder reviews into final design adjustments.
- Address any remaining issues or concerns identified during the development process to ensure the final design meets all requirements and expectations.
-
Document Design Changes:
-
- Utilize the selected additive manufacturing method to fabricate physical prototypes with accuracy and fidelity to the digital design.
- Ensure that the manufacturing parameters, like layer thickness, build orientation, and material selection, are optimized to achieve the desired part quality and performance
-
Document Design Changes:
-
- Document all design changes, revisions, and decisions made throughout the development process to maintain traceability and accountability.
- Create detailed design documentation, including engineering drawings, specifications, and Bill of Materials (BOM), to guide manufacturing and assembly processes.
-
Document Design Changes:
-
- Finalize the design for production, ensuring that all necessary preparations are made for manufacturing, assembly, and quality control.
- Coordinate with manufacturing partners and suppliers to transfer the design into production and ensure a smooth transition from development to deployment.
Final Production through Additive Manufacturing (Optional Step Based on Application of the Design)
-
Scale-Up for Production:
-
- Transition the optimized design from prototyping to full-scale production using additive manufacturing technologies.
- Scale production volumes by optimizing manufacturing processes, streamlining workflows, and maximizing machine utilization.
-
Manufacturing Process Optimization:
-
- Fine-tune manufacturing parameters, such as build speed, layer thickness, and material handling, to optimize production efficiency and part quality.
- Implement continuous improvement initiatives to identify and address bottlenecks, minimize waste, and enhance productivity throughout the manufacturing process.
-
Quality Assurance and Control:
-
- Establish rigorous quality assurance and control measures to ensure manufactured parts' consistency, reliability, and repeatability.
- Implement inspection protocols, quality control checks, and validation procedures to verify compliance with design specifications and regulatory requirements.
-
Supply Chain Integration:
-
- Integrate additive manufacturing into the broader supply chain ecosystem by collaborating with suppliers, manufacturers, and logistics partners.
- Explore opportunities for on-demand manufacturing, distributed production, and agile supply chain strategies to meet evolving market demands and customer requirements.
-
Post-Processing and Finishing:
-
- Implement post-processing techniques, such as surface finishing, heat treatment, Painting, and machining, to enhance manufactured parts' aesthetics, functionality, and performance.
- Develop standardized post-processing workflows and procedures to ensure consistency and quality across production batches.
In summary, the Design for Additive Manufacturing (DfAM) workflow provides a structured framework for designers to create innovative, efficient, and manufacturable designs. By following a systematic approach encompassing conceptualization, CAD modeling, simulation, optimization, prototyping, final adjustments, and final production, designers can harness the full potential of additive manufacturing technologies.
Optimizing Designs for Different 3D Printing Technologies
Here are some concise tips for optimizing designs across various 3D printing methods:
FDM Design Tips
- Minimize Overhangs: Keep overhangs below 45 degrees to reduce the need for support.
- Consider Layer Orientation: Align layers to maximize strength along the load-bearing direction.
- Ensure Adequate Wall Thickness: Use 1-2 mm thick walls for structural integrity.
- Add Filets to Corners: Reduce stress concentrations by rounding corners.
- Use Chamfers: Replace sharp edges with chamfers to improve print quality and reduce support needs.
SLA Design Tips
- Thin Walls and Fine Details: Keep overhangs below 45 degrees to reduce the need for support.
- Include Drainage Holes: Align layers to maximize strength along the load-bearing direction.
- Minimize Supports: Use 1-2 mm thick walls for structural integrity.
- Avoid Large Flat Surfaces: Reduce stress concentrations by rounding corners.
- Prepare for Post-Processing: Replace sharp edges with chamfers to improve print quality and reduce support needs.
SLS Design Tips
- Maintain Minimum Wall Thickness: Use 1-1.5 mm for adequate strength.
- Add Escape Holes: Include 2 mm holes for powder removal in cavities.
- Design for Moving Parts: Allow 0.5 mm clearance for interlocking parts.
- Leverage Surface Texture: Utilize the rough texture for functional or aesthetic purposes.
DMLS Design Tips
- Optimize for Support Removal: Design with easy access for removing supports.
- Maintain Consistent Wall Thickness: Use uniform wall thickness to prevent thermal stress.
- Include Filets and Chamfers: Reduce sharp edges to minimize stress concentrations.
- Plan for Post-Processing: Design for ease of surface finishing and heat treatment.
MJF Design Tips
- Uniform Wall Thickness: Aim for 1-2 mm to prevent warping and ensure strength.
- Clearance for Moving Parts: Ensure at least 0.5 mm clearance for articulated parts.
- Utilize Escape Holes: Design with holes for powder removal in internal cavities.
- Minimize Supports: Use MJF's minimal support requirement by designing self-supporting features.
For a tabulated summary of the design rules for different 3D printing technologies, refer to the chart below.
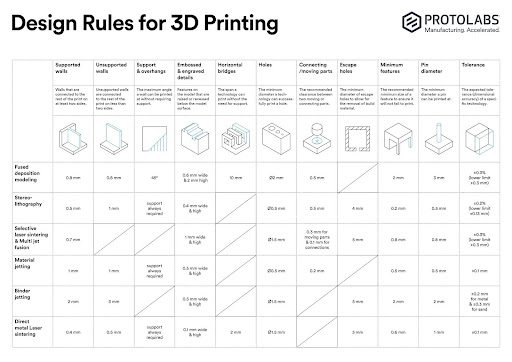
Case Studies and Examples
Successful Design Projects
General Electric (GE) - Jet Engine Fuel Nozzles
- Project Overview: General Electric utilized additive manufacturing to redesign the fuel nozzles for their LEAP jet engines. Traditional manufacturing methods required 20 separate parts to be assembled into a single nozzle.
- For the design for additive manufacturing (DFAM), GE engineers consolidated the design into a single piece using direct metal laser sintering (DMLS). This significantly reduced the nozzle's complexity and weight while enhancing its durability and performance.
- Outcome: The new fuel nozzle design reduced weight by 25% and offered five times the durability of traditionally manufactured nozzles. Integrating multiple components into one streamlined piece also reduced potential points of failure.
Adidas - Futurecraft 4D Shoes
- Project Overview: Adidas collaborated with Carbon, a leading 3D printing company, to produce the midsole for their Futurecraft 4D shoes. The goal was to create a high-performance shoe with customizable features tailored to individual athletes.
- For the design for additive manufacturing (DFAM): Using Digital Light Synthesis (DLS), Adidas created intricate lattice structures in the midsole, optimizing the balance between cushioning and support.
- Outcome: The Futurecraft 4D shoes offered enhanced performance and comfort, with the ability to fine-tune the midsole's properties for specific athletic needs. The project demonstrated the potential of additive manufacturing to revolutionize the footwear industry with bespoke designs and rapid prototyping.
Airbus - A350 XWB Cabin Brackets
- Project Overview: Airbus implemented additive manufacturing to produce over 1,000 parts, including cabin brackets, for its A350 XWB aircraft. These components needed to be lightweight yet strong enough to meet strict aerospace standards.
- For the design for additive manufacturing (DFAM): Airbus used Selective Laser Sintering (SLS) to manufacture the brackets from high-performance thermoplastics. This process allowed for complex geometries and weight-optimized designs that were not feasible with traditional manufacturing.
- Outcome: Using additive manufacturing in the A350 XWB led to significant weight savings, improved fuel efficiency, and reduced manufacturing costs. This project's success has encouraged the broader adoption of additive manufacturing in the aerospace industry.
Common Design Challenges and Solutions
Challenge: Warping in Fused Deposition Modeling (FDM)
Solution: To mitigate warping, designers can use features such as brims and rafts to improve bed adhesion and reduce thermal stress. Additionally, optimizing the part orientation and incorporating gradual transitions in geometry can minimize warping.
Challenge: Surface Finish in Stereolithography (SLA)
Solution: Post-processing techniques, such as sanding, chemical smoothing, and coating, can enhance the surface finish of SLA prints. Designers should also consider using higher resolution settings during printing to reduce the layer visibility.
Challenge: Support Structure Removal in Direct Metal Laser Sintering (DMLS)
Solution: Designing parts with self-supporting angles and minimizing overhangs can reduce the need for support structures. Using lattice structures and strategic support placements can facilitate easier removal and minimize material waste.
Challenge: Inconsistent Material Properties in Multi Jet Fusion (MJF)
Solution: Conduct thorough testing and validation to understand the material properties of MJF-produced parts. Implementing design adjustments, such as uniform wall thickness and consistent part orientation, can enhance material consistency.
The case studies and examples discussed above highlight the transformative potential of additive manufacturing across various industries. From aviation and footwear to complex aerospace components, Overcoming common design challenges through strategic solutions has demonstrated the feasibility and benefits of this technology.
Future Trends in Additive Manufacturing Design
Advances in Materials
The development of new materials, including high-performance polymers, biocompatible resins, and advanced metal alloys, is expanding additive manufacturing applications. These materials offer improved mechanical properties, biocompatibility, and environmental resistance, opening new possibilities for healthcare, aerospace, and automotive industries.
Innovations in 3D Printing Technologies
The relentless progress in 3D printing technologies, such as multi-material printing and hybrid manufacturing, is not just enhancing the capabilities and efficiency of additive manufacturing, but also reshaping the very limits of design and manufacturing. These innovations are empowering the production of more intricate and functional parts, heralding a new era in the industry.
Impact of AI and Machine Learning
Artificial intelligence (AI) and machine learning are revolutionizing additive manufacturing, providing powerful tools to enhance design and production processes.
Text-to-3D Generative Software
Text-to-3D generative software enables users to create 3D models from textual descriptions, significantly streamlining the design process. These tools use natural language processing (NLP) and generative algorithms to interpret textual input and generate accurate, detailed 3D models. This approach simplifies rapid prototyping, allows for extensive customization, and makes 3D design more accessible.
Example: Meshy.ai: Meshy.ai is a leading example of text-to-3D generative software. It allows users to input descriptions, such as "ergonomic office chair," and instantly produces detailed 3D models that can be refined and printed. This tool reduces the time and expertise required for initial model creation, making it a valuable resource for designers and manufacturers.
Generative Design
Generative design utilizes AI to create multiple options based on specified parameters and constraints, such as material type, weight, and strength. This process involves using algorithms to explore and optimize designs, often producing innovative solutions that human designers might not conceive. Generative design enhances the creation of complex geometries, optimizes performance, and promotes sustainability by reducing material waste.
Example: Autodesk Fusion 360: Autodesk Fusion 360 is a prominent generative design tool. Engineers can input design goals and constraints into the software, generating numerous design iterations that meet these criteria. This allows for selecting the most optimal solution, streamlining the design process, and enhancing efficiency.
Conclusion
Designing for additive manufacturing (AM) isn't just a new approach, it's a transformative one. It opens up possibilities for creating complex, customized, and efficient products that were once unimaginable.
By understanding various AM processes and materials, designers can fully leverage AM's unique advantages, sparking a new era of design and manufacturing. This guide has covered essential design principles, key considerations, and a comprehensive workflow for AM. AM's benefits, such as customization, complex geometries, reduced material waste, faster prototyping, and cost-effective production, highlight its potential to revolutionize manufacturing.
As a leading 3D printing partner, iamrapid.com offers online 3D printing services with an instant quotation system, providing transparent quotes within seconds. At iamrapid.com, you don't just get instant quotations; our advanced quotation software also performs model analysis, including wall thickness analysis, orientation optimization, and repairing parts for optimal printing.
Moreover, iamrapid.com excels in complete product design development services, handling the entire design process from ideation to final production-ready design. For further assistance, iamrapid.com is here to support you every step of the way, ensuring your additive manufacturing journey is smooth and successful.
In summary, designing for additive manufacturing (AM) is a dynamic field with significant opportunities for innovation and efficiency. By following the principles and best practices outlined in this guide, designers can harness AM's full potential to create groundbreaking products.