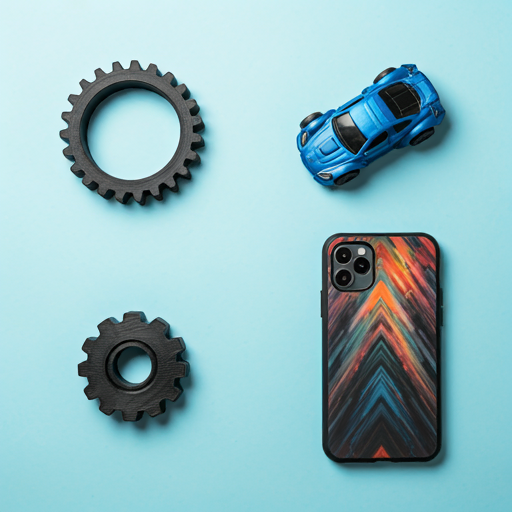
-
How it works
-
Industries
-
Services
-
Material
-
Company
-
Resources
Omni is a state-of-the-art fingertip oximeter designed to deliver fast, accurate, and real-time health insights in a sleek and modern form. Crafted with a focus on ease of use and advanced technology, Omni offers a seamless health monitoring experience.
Its compact design houses a high-resolution AMOLED touch display, providing clear and vibrant data visualization. Whether for everyday wellness tracking or specific health management, Omni brings professional-grade monitoring to the convenience of your home.
Designed with both style and function in mind, Omni stands out for its innovative features, intuitive usability, and commitment to accurate health tracking. It’s the ideal companion for fitness enthusiasts, individuals managing health conditions, or anyone prioritizing well-being.
With Omni, you’re not just monitoring your health—you’re empowering yourself with data-driven wellness, presented through cutting-edge technology and thoughtful design.
iamRapid Engineering Design Services specializes in advanced mechanical and electromechanical CAD design, providing expert support for projects of any scale. Our experienced design team guides you in choosing the right design approach, ensuring high-quality CAD services at the best affordable prices.
Understanding customer requirements is our top priority in product design and development. We begin by gathering all necessary data to initiate the process, ensuring a strong foundation for success. Our team leverages their expertise to offer valuable insights and recommendations, helping customers refine their products and make informed decisions.
Through brainstorming and ideation sessions, our research team evaluates all potential concepts, conducts market and feasibility studies, and compiles a comprehensive report. This document is then shared with the customer, allowing them to select the best idea to move forward into the concept development phase.
Once the concept is finalized, it is meticulously designed using CAD software, undergoes simulations for testing, and is then optimized for manufacturability. After the customer approves the CAD design, we proceed to production using the chosen additive manufacturing method. Following production, we perform necessary post-processing to ensure quality and precision before delivering the final product right to the customer’s doorstep.
The transition from concept to a refined digital model was a crucial step in the development of Omni. Using advanced CAD software, we translated our ideation sketches into a precise 3D model, ensuring every curve, edge, and opening was optimized for both aesthetics and functionality. The triangular cylindrical shape was carefully modeled to maintain ergonomic comfort while efficiently housing the necessary sensors, electronic components, and clamping mechanism.
With its unique form factor, special attention was given to the design of the finger-clamping system, ensuring a secure yet comfortable fit for accurate readings. We also focused on the seamless integration of the AMOLED touch display, maintaining a smooth and minimalistic exterior. Structural analysis was conducted to validate the model’s durability, ensuring the device remains lightweight yet robust for everyday use.
This stage was essential in refining the design and preparing it for prototyping, balancing visual appeal with practical performance and user comfort.
To bring the digital model of Omni into the physical world, we leveraged 3D printing for rapid prototyping. This approach allowed us to translate our CAD designs into tangible objects quickly, enabling hands-on evaluation of the product’s form, fit, and ergonomics. The unique triangular cylindrical shape and buttonless design were tested extensively to ensure user comfort and ease of use.
3D printing also helped us test the integration of essential components like the finger opening, AMOLED touch display, and internal sensors. Multiple iterations allowed us to refine the device’s size and form without sacrificing functionality.
While 3D printing served well for prototyping, the next phase focuses on transitioning to mass production methods that offer greater efficiency and cost-effectiveness.
After successfully validating the Omni’s design through 3D-printed prototypes, the next step is to plan for scalable, cost-efficient mass manufacturing. While 3D printing was invaluable for form, fit, and function testing, mass production demands a different approach — one focused on material selection, manufacturing precision, and market positioning.
The transition from prototyping to mass production directly influences the cost structure and market positioning of the Omni. Careful material and process selection will determine production efficiency, product quality, and overall pricing strategy.
Economies of Scale: Batch manufacturing acts as a crucial intermediary step, refining production techniques and evaluating market readiness. This phase ensures cost-effective, high-quality output before committing to full-scale production.
In conclusion, this case study highlights the crucial role of 3D printing in accelerating design validation through rapid prototyping. This approach enabled swift evaluation of form, fit, and function, helping refine the oximeters design efficiently.
As we transition toward mass production, the manufacturing method will depend on product positioning. Premium models may use CNC machining with high-grade metals, while mid-range and budget versions could adopt injection molding and cost-effective metal fabrication.
This transition involves balancing quality, cost, and production volume. Future steps will focus on optimizing the design for manufacturability (DfM) and conducting batch production for market testing, ensuring the product’s economic viability and readiness for full-scale manufacturing.